Rubber Seal Joint Molds: Enhancing Precision and Efficiency
Introduction: Rubber seal joint molds are crucial components in the manufacturing process of rubber seals used in various industries, including automotive, construction, and engineering. These molds facilitate the production of high-quality rubber seal joints that ensure efficient and effective sealing in a wide range of applications. In this article, we will explore the significance of rubber seal joint molds, their key features, and the impact of their precision on the final product.
Key Features of Rubber Seal Joint Molds:
Accuracy and Precision: Rubber seal joint molds are engineered with a high degree of precision to ensure that the resulting seal joints meet exacting specifications, providing reliable sealing properties.
Customization Capabilities: These molds offer the flexibility to produce a diverse range of seal joint designs and sizes, catering to the specific requirements of different applications and industries.
Durability: High-quality rubber seal joint molds are constructed from robust materials capable of withstanding the pressures and temperatures involved in the rubber molding process, ensuring longevity and consistency in production.
Consistency in Output: The molds enable the replication of identical seal joint designs and dimensions, ensuring consistency in the quality and performance of the manufactured rubber seals.
Efficient Production: With streamlined manufacturing processes and optimized design features, rubber seal joint molds contribute to efficient production cycles, allowing for increased output and reduced lead times.
Significance of Precision in Rubber Seal Joint Molds:
Sealing Performance: The precision of the mold directly impacts the sealing performance of the rubber seals, influencing their ability to withstand pressure differentials, environmental conditions, and chemical exposures.
Product Quality: Precise molds contribute to the production of high-quality rubber seal joints with uniform dimensions, smooth surfaces, and accurate profiles, meeting or exceeding industry standards and specifications.
Cost Efficiency: Accurate molds minimize material wastage and production errors, leading to cost savings and improved overall operational efficiency.
Reliability and Safety: Precision-molded rubber seal joints provide reliable sealing properties, reducing the risk of leaks, contamination, and operational malfunctions across various applications, thereby enhancing safety and performance.
Customer Satisfaction: Consistent precision in the manufacturing of rubber seal joints meets the expectations of end-users, contributing to increased customer satisfaction and trust in the product's reliability and longevity.
Conclusion: Rubber seal joint molds play a pivotal role in the production of high-quality rubber seals with dependable sealing attributes. The precision and customization capabilities of these molds influence the overall quality, efficiency, and performance of the manufactured rubber seal joints, underscoring their significance in diverse industrial settings. By investing in precision-engineered molds, manufacturers can enhance the integrity of their products, optimize production processes, and meet the stringent requirements of modern applications, ultimately fostering trust and satisfaction among end-users.
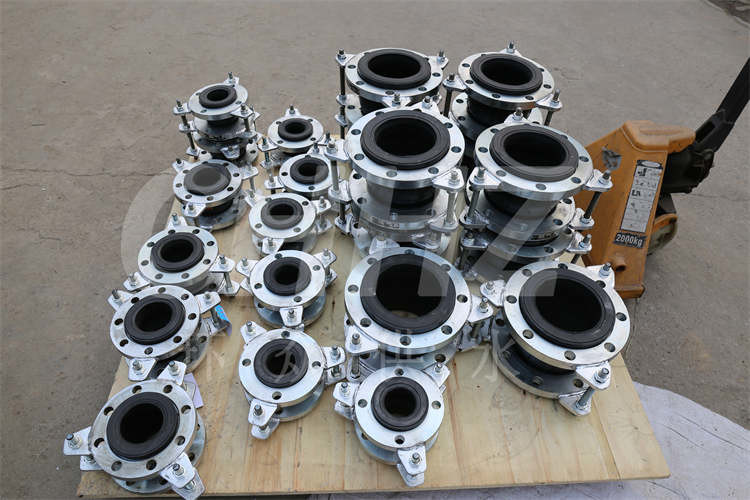