High-Temperature Resistant Rubber Expansion Joints: Manufacturing and Applications
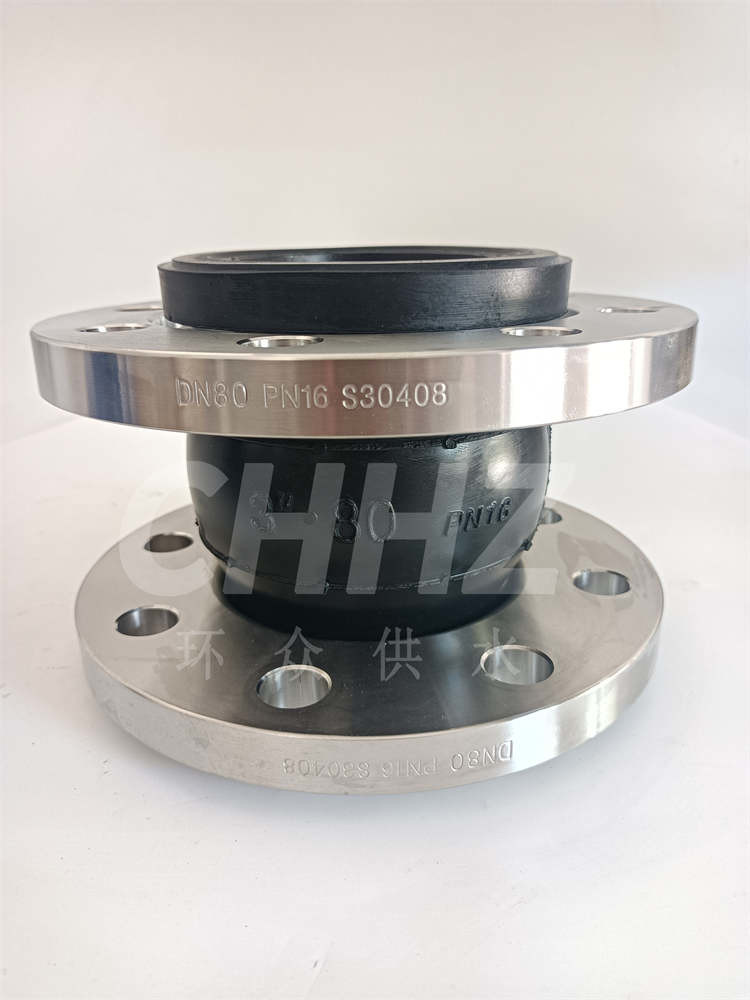
Introduction High-temperature resistant rubber expansion joints play a critical role in various industrial applications where exposure to elevated temperatures is a constant challenge. These specialized components are designed to withstand extreme heat conditions while providing flexibility and vibration isolation in piping systems.
Manufacturing Process The manufacturing of high-temperature resistant rubber expansion joints involves the selection of premium elastomers capable of withstanding elevated temperatures without compromising their mechanical properties. The process includes precision molding, vulcanization, and quality control checks to ensure the product's durability and performance under high-temperature conditions.
Material Selection The choice of elastomeric materials for high-temperature resistant expansion joints is crucial. Silicone, fluorocarbon, and EPDM rubber compounds are commonly used due to their exceptional heat resistance, chemical compatibility, and flexible characteristics. These materials undergo rigorous testing to meet industry standards and performance requirements.
Design and Engineering The engineering of high-temperature resistant rubber expansion joints entails careful consideration of thermal expansion, pressure fluctuations, and operational conditions. Advanced design features, such as multiple plies, heat-resistant reinforcements, and specialized flange configurations, are incorporated to ensure long-term reliability and integrity in high-temperature environments.
Applications High-temperature resistant rubber expansion joints find diverse applications across industries such as power generation, petrochemical plants, steel mills, and industrial furnaces. These components are utilized in critical areas including exhaust systems, steam lines, hot water piping, and thermal fluid handling, where the demand for reliable heat-resistant solutions is paramount.
Performance and Maintenance The performance of high-temperature resistant rubber expansion joints is contingent upon proper installation, regular maintenance, and adherence to temperature and pressure limits. Maintenance protocols encompass periodic inspections, replacement of worn components, and monitoring of thermal cycling effects to mitigate potential failures and ensure optimal performance.
Adherence to Standards Compliance with industry standards and regulations, such as ASTM, ASME, and ISO requirements, is fundamental in the production and application of high-temperature resistant rubber expansion joints. Adhering to these standards guarantees the quality, safety, and performance of these specialized components in high-temperature environments.
Conclusion In conclusion, the manufacturing and application of high-temperature resistant rubber expansion joints signify a critical aspect of industrial infrastructure. Their ability to endure extreme heat conditions while accommodating movement and vibration in piping systems underscores their significance in high-temperature applications across various industrial sectors. Awareness of their manufacturing process, material selection, design considerations, and performance requirements is essential to ensure their effective deployment in high-temperature environments.
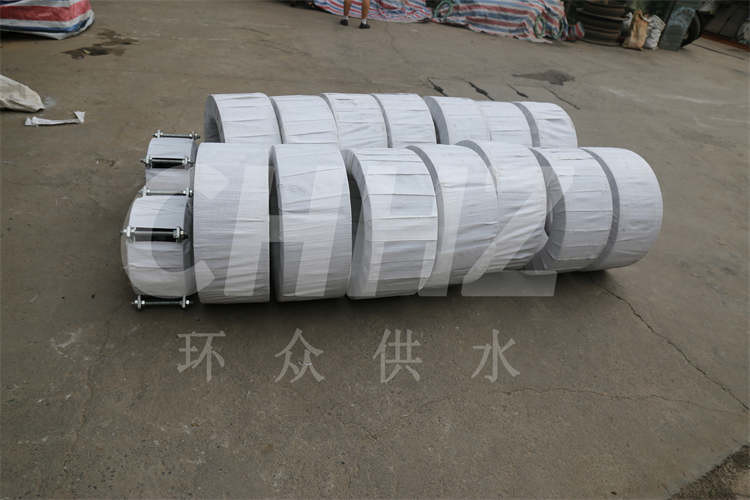