Rubber Expansion Joint Blanking Process Equipment
Introduction The production process of rubber expansion joint blanks involves a series of precision manufacturing steps, necessitating the utilization of specialized equipment. The machinery employed in the blanking process plays a crucial role in ensuring the dimensional accuracy, surface quality, and material integrity of the final product. This article provides an overview of the essential equipment used in the fabrication of rubber expansion joint blanks.
Cutting Machine The cutting machine is a fundamental piece of equipment in the production of rubber expansion joint blanks. It is equipped with specialized cutting tools such as die-cutting presses or water jet cutters. Die-cutting presses utilize custom-designed dies to stamp out the required shapes from rubber sheets, ensuring precise and uniform cutting. Water jet cutters, on the other hand, use high-pressure water mixed with an abrasive substance to precisely cut through rubber materials, offering versatility in shape cutting and minimizing material waste.
Molding Press Molding presses are employed in the vulcanization process, where the rubber blanks are formed and cured under controlled temperature and pressure conditions. These presses are equipped with heating elements and mold cavities designed to impart the required geometry and physical properties to the rubber expansion joint blanks. The application of heat and pressure during the vulcanization process ensures the cross-linking of polymer chains within the rubber material, resulting in enhanced strength, elasticity, and chemical resistance.
Surface Treatment Equipment Surface treatment is a critical aspect of the rubber expansion joint blank production process, enhancing the adhesion and bonding properties of the material. Equipment such as buffing machines, sanding stations, and surface cleaning systems are utilized to prepare the surface of the rubber blanks for subsequent processes like bonding or coating. These machines ensure that the surface of the rubber blanks is free from contaminants, roughness, and imperfections, promoting optimal adhesion and finishing quality in the final product.
Quality Control Systems Quality control systems and testing equipment are integral to the blanking process, ensuring that the manufactured rubber expansion joint blanks meet the required specifications and standards. Equipment such as dimensional gauges, hardness testers, and visual inspection stations are employed to verify the dimensional accuracy, physical properties, and surface quality of the fabricated blanks. These quality control measures are essential in identifying and rectifying any deviations or defects in the manufactured rubber expansion joint blanks.
Conclusion The production of rubber expansion joint blanks involves the use of specialized equipment designed to facilitate precise cutting, shaping, vulcanization, surface treatment, and quality control processes. The selection and utilization of appropriate machinery are essential in ensuring the dimensional accuracy, material quality, and performance characteristics of the final product. By employing advanced equipment and adhering to stringent manufacturing standards, the production of rubber expansion joint blanks can meet the demanding requirements of various industrial applications.
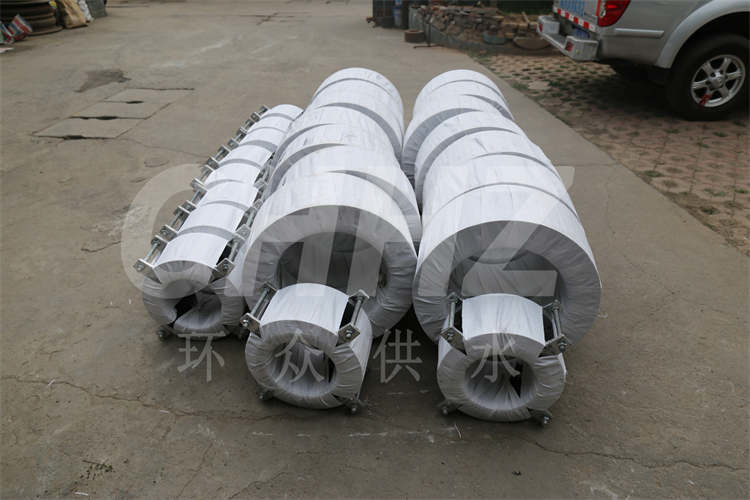