Rubber Flexible Coupling Mold
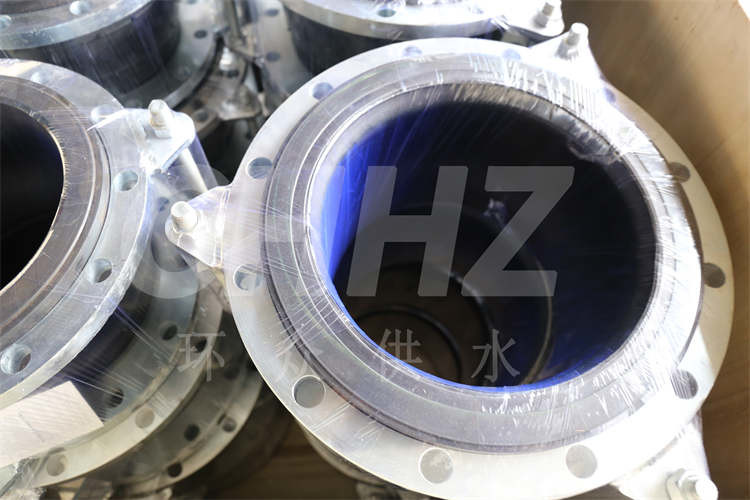
Rubber flexible couplings are widely used in various industries to connect pipes or devices with different diameters. The mold used for producing rubber flexible couplings plays a crucial role in ensuring the accuracy and quality of the final product. This article provides an overview of the design and production process of a rubber flexible coupling mold, highlighting the key considerations and challenges involved.
Design Considerations: The design of a rubber flexible coupling mold requires careful consideration of various factors such as the dimensions of the coupling, material flow dynamics, and mold release characteristics. The mold must be designed to accommodate the specific variations in diameter, ensuring a seamless transition from one size to another. The choice of material for the mold is critical, with hardened steel being a commonly preferred option due to its durability and heat resistance. Additionally, the mold design should incorporate features that allow for precise control of the rubber injection process, ensuring uniformity and consistency in the final product.
Production Process: The production process of a rubber flexible coupling mold typically begins with the design phase, where specialized software is used to create a detailed 3D model of the mold. Once the design is finalized, the mold components are manufactured using CNC machining or other precision manufacturing techniques to ensure high accuracy. Careful attention is paid to the surface finish of the mold components, as this directly impacts the quality of the finished product. The mold is then assembled, and the rubber injection equipment is set up for the production run.
Challenges and Quality Control: One of the primary challenges in the production of rubber flexible coupling molds is maintaining the dimensional accuracy and consistency of the final product. Variations in mold temperature, material flow, and curing process can result in defects such as uneven wall thickness or surface imperfections. To address this, quality control measures such as dimensional checks, material hardness tests, and visual inspections are implemented throughout the production process. Any deviations from the specified tolerances are promptly identified and corrected to ensure that the mold produces high-quality rubber flexible couplings.
Customization and Adaptability: An essential aspect of rubber flexible coupling molds is their ability to accommodate customization and adaptability to different product specifications. This requires the mold to be designed with interchangeable components or adjustable features that allow for quick reconfiguration to produce couplings with varying diameter transitions. The versatility of the mold design contributes to its flexibility in meeting diverse industry requirements and product variations.
In conclusion, the design and production of a rubber flexible coupling mold involve careful consideration of various factors to ensure the accuracy, consistency, and adaptability of the final product. The meticulous attention to design details, material selection, and quality control measures is critical in producing high-quality rubber flexible couplings that meet the demands of diverse industrial applications. By addressing the challenges and implementing rigorous quality control, manufacturers can ensure that their rubber flexible coupling molds yield superior products that adhere to stringent standards and specifications.
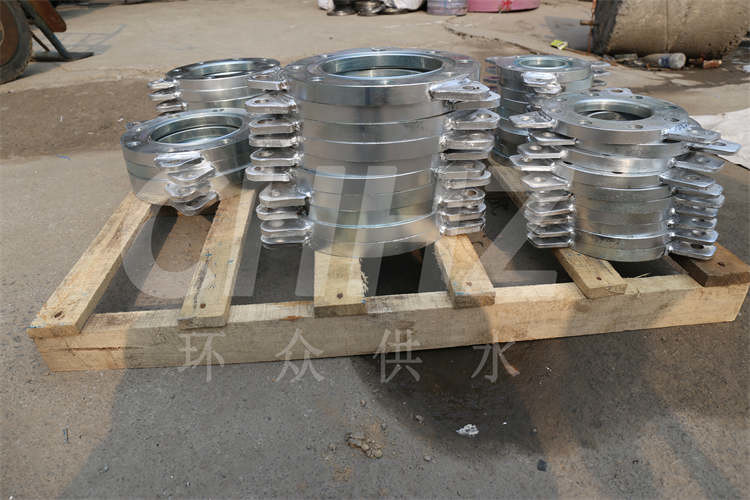