Requirements for Plastic and Rubber Waterstop Joint
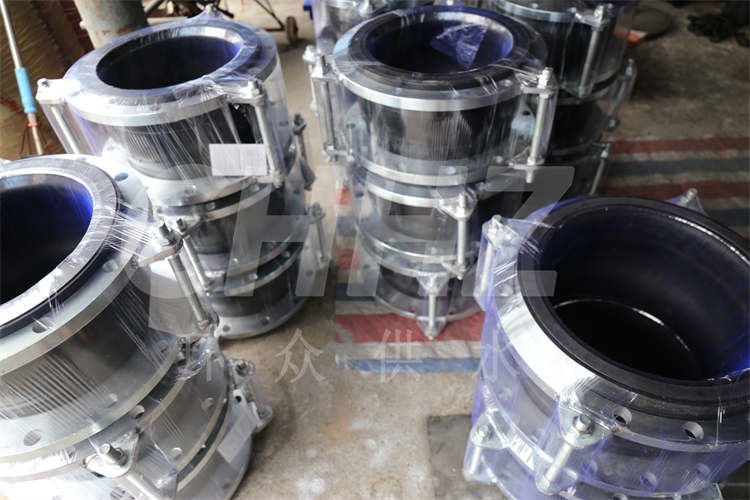
Plastic and rubber waterstops play a crucial role in modern construction, providing an essential barrier against water ingress in concrete structures. The joints used for connecting these waterstops are held to rigorous standards to ensure their effectiveness in preventing water seepage and maintaining structural integrity. This article outlines the key requirements for joints used in plastic and rubber waterstops, emphasizing the necessary qualities that enable them to withstand hydraulic pressure, accommodate structural movement, and deliver long-term waterproofing performance in diverse construction applications.
The jointing of plastic and rubber waterstops demands precision and reliability to effectively seal construction joints, expansion joints, and other vulnerable areas in concrete structures. A crucial requirement for waterstop joints is compatibility with the specific waterstop profiles, ensuring seamless integration and consistent sealing throughout the formwork installation and concrete pouring process. This compatibility allows for the construction of watertight joints that serve as an effective barrier against water infiltration while accommodating the dynamic forces and movements that occur within the concrete structure.
Furthermore, high-quality joint materials, such as PVC, rubber, or thermoplastic elastomers, must exhibit excellent durability, flexibility, and chemical resistance to ensure long-term performance in demanding construction environments. The joint materials should be capable of withstanding exposure to aggressive chemicals, UV radiation, and temperature variations, thereby preserving their sealing properties and mechanical integrity over the lifespan of the concrete structure.
Moreover, the jointing method and accessories used in plastic and rubber waterstop installation are paramount in achieving reliable and watertight connections. The use of specialized welding equipment, adhesives, or mechanical connectors is crucial for ensuring the proper bonding and sealing of waterstop joints, thereby mitigating the risk of water penetration and ensuring the sustainability of waterproofing measures.
Additionally, the joint design must consider the structural movement, settlement, and loading conditions that the concrete structure may experience during its service life. Adequate provision for expansion, contraction, and lateral movement should be incorporated into the design of waterstop joints to accommodate the dynamic nature of concrete structures and prevent the formation of cracks or gaps that could compromise the water-resisting capabilities of the waterstops.
In conclusion, the requirements for joints used in plastic and rubber waterstops revolve around compatibility, durability, effective sealing, and adaptability to structural movements. By adhering to stringent standards and selecting high-quality materials, construction professionals can ensure the effective integration and long-term performance of waterstop joints, thus safeguarding concrete structures against water infiltration and preserving their integrity. The implementation of reliable jointing solutions is essential for delivering durable and watertight construction joints, culminating in the successful waterproofing of concrete structures in various civil engineering and building projects.
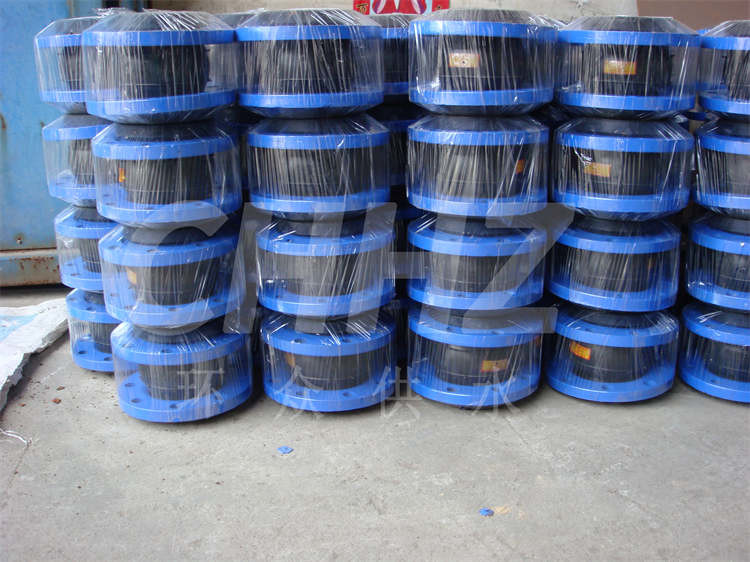