Intermidate Joint for Rubber Cables
An integral component of rubber cable systems, the intermediate joint plays a crucial role in ensuring the effective transmission of electrical power and signals. This article delves into the key aspects of intermediate joints for rubber cables, highlighting their significance, design considerations, and installation procedures.
Significance:
The intermediate joint serves as a connection point between two separate lengths of rubber cables, enabling the continuation of electrical conductivity without compromising performance or safety. It plays a critical role in maintaining the integrity and reliability of the cable network, particularly in applications where long-distance power transmission or signal distribution is required.
Design Considerations:
Material Selection: The materials used in the construction of intermediate joints must exhibit high electrical conductivity, mechanical strength, and resistance to environmental factors such as moisture, heat, and abrasion. Common materials may include specially formulated rubber compounds, insulating materials, and metal components designed to withstand the rigors of electrical use.
Compatibility: The intermediate joint must be designed to seamlessly integrate with the specific type and specifications of the rubber cables being joined. Compatibility with cable insulation, conductor materials, and shielding configurations is essential to ensure optimal electrical performance and reliability.
Sealing and Insulation: Effective sealing and insulation mechanisms are essential to protect the joint from ingress of moisture, contaminants, and other environmental hazards. This involves the use of specialized insulating materials, heat-shrinkable sleeves, and sealing compounds to create a durable and reliable protective barrier around the joint.
Flexibility: Given the dynamic nature of cable installations, intermediate joints should be designed to accommodate bending, movement, and environmental stress without compromising their electrical performance or structural integrity. Flexible materials and mechanical designs that allow for movement and expansion are critical for long-term reliability.
Installation Procedures:
Cable Preparation: Prior to joint installation, the cable ends must be carefully prepared by stripping the insulation, shielding, and conductor layers to expose the necessary length of conductors for connection.
Joint Assembly: The intermediate joint components, including connectors, insulation materials, and sealing elements, are carefully assembled in accordance with the manufacturer's specifications and installation guidelines.
Connection and Termination: The exposed conductors from the cable ends are securely connected and terminated within the joint assembly using appropriate crimping, soldering, or compression techniques to ensure reliable electrical continuity.
Sealing and Protection: Once the joint is assembled and the connections are made, protective insulation and sealing elements are applied and secured to create a robust barrier against environmental factors and mechanical stresses.
In summary, the design and installation of intermediate joints for rubber cables involve a meticulous approach to ensure electrical performance, environmental resilience, and long-term reliability. By adhering to best practices and industry standards, engineers and installation professionals can effectively implement intermediate joints that contribute to the overall integrity and functionality of rubber cable systems.
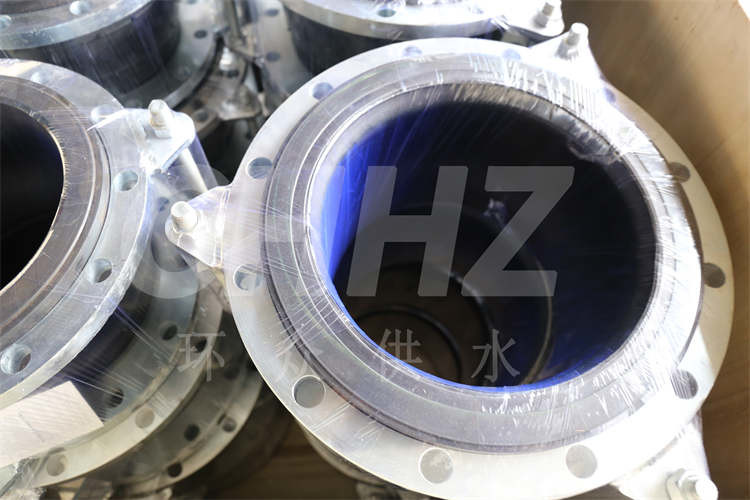