Rubber Hose Joint Compression Mold
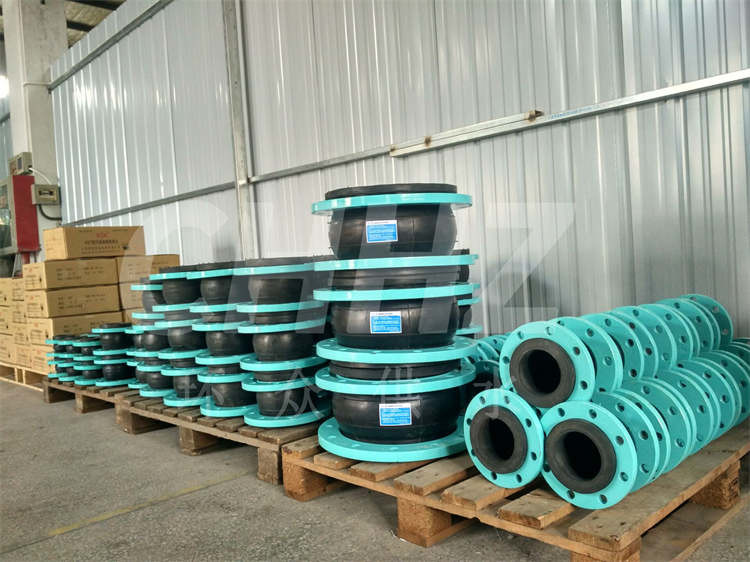
Rubber hose joints are an essential component used in a wide variety of industrial and commercial applications. These joints enable the connection of rubber hoses to different equipment and piping systems, allowing for the efficient transfer of liquids, gases, and other substances. To ensure the proper functioning of rubber hose joints, it is crucial to use high-quality compression molds during the manufacturing process.
Compression molds play a vital role in the production of rubber hose joints, as they are responsible for shaping and forming the rubber materials into the desired joint configuration. When designing compression molds for rubber hose joints, several key factors need to be taken into consideration to ensure optimal performance and durability.
First and foremost, the material used in the construction of the compression mold must be able to withstand the high pressure and temperature conditions involved in the rubber molding process. Typically, materials such as high-grade steel or aluminum are chosen for their robustness and heat resistance, ensuring that the mold can endure the rigors of repetitive use.Precision in mold design is another critical aspect that should not be overlooked. The mold must be meticulously engineered to accurately replicate the specific dimensions and features of the rubber hose joint. This precision is essential in ensuring the proper fit and functionality of the joint when connected to other components. Additionally, the mold design should allow for easy release of the formed joint, thus facilitating a smooth and efficient manufacturing process.
Furthermore, the surface finish of the compression mold is crucial in achieving a high-quality final product. A smooth and polished surface finish is essential to impart a flawless appearance to the molded rubber hose joint, as well as to facilitate easy release of the finished part from the mold.
In addition to the physical aspects of the mold, the manufacturing process itself must also be carefully regulated to ensure consistent quality. This includes controlling parameters such as temperature, pressure, and curing time to achieve the desired material properties and structural integrity in the final product.
In conclusion, the design and fabrication of compression molds for rubber hose joints are vital aspects of ensuring the production of high-quality components. By utilizing high-quality materials, precision engineering, and meticulous manufacturing processes, manufacturers can produce durable and reliable rubber hose joints that meet the demands of various industrial and commercial applications.
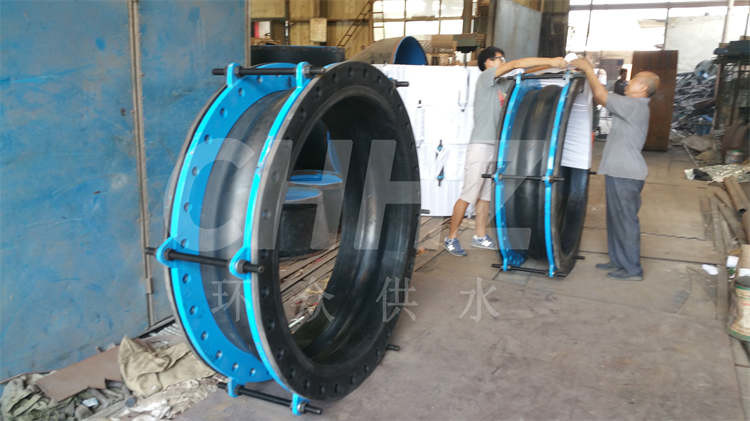