Rubber Hose Joints for Automotive Applications
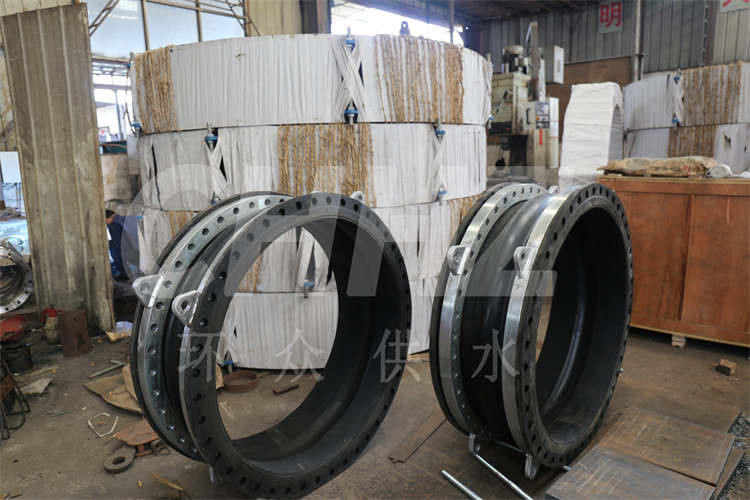
Rubber hose joints are integral components in automotive systems, playing a critical role in facilitating fluid and air transfer within various vehicle systems. These components are designed to withstand dynamic operating conditions, ensuring reliable performance in diverse automotive applications. Below is an overview of the key aspects and uses of rubber hose joints in automotive systems.
Sealing and Flexibility: Rubber hose joints are employed in automotive systems for their exceptional sealing properties and flexibility. These components are designed to effectively seal connections and interfaces, preventing leakages of fluids and gases in critical systems such as fuel delivery, coolant circulation, and hydraulic power steering. Additionally, the inherent flexibility of rubber enables hose joints to accommodate dynamic movements and vibration within the vehicle, contributing to the overall durability and reliability of automotive systems.
Fluid and Air Transfer: In an automotive context, rubber hose joints are used to facilitate the transfer of various fluids and gases. For instance, in the engine compartment, these components are utilized for conveying coolant between the radiator, engine block, and heater core. Similarly, fuel hose joints play a crucial role in providing a reliable conduit for transporting gasoline from the tank to the engine, ensuring optimal combustion and engine performance. Furthermore, vacuum hose joints serve as essential connectors for managing air pressure in systems such as the braking and HVAC systems.
Resistance to Environmental Factors: Automotive rubber hose joints are engineered to withstand a wide range of environmental factors encountered during vehicle operation. They must exhibit resilience to temperature variations, exposure to engine fluids, and resistance to degradation from ozone and ultraviolet (UV) radiation. By maintaining their structural integrity and sealing capacity under such conditions, these components ensure the safe and efficient operation of automotive systems across diverse driving environments.
Integrated Functionality and Design: The design of rubber hose joints incorporates features that enhance their functionality and performance within automotive systems. These can include reinforced layers for increased pressure resistance, specially formulated rubber compounds to withstand specific fluids, and the integration of molded shapes for precise fitment and connection. These design elements contribute to the overall reliability and longevity of the hose joints in demanding automotive applications.
Regulatory Compliance and Safety: The use of rubber hose joints in automotive systems is subject to stringent regulatory standards and safety considerations. Manufacturers adhere to industry-specific regulations and quality assurance protocols to ensure that these components meet safety, environmental, and performance requirements. Compliance with standards such as SAE (Society of Automotive Engineers) specifications is essential to guarantee the reliability and safety of rubber hose joints in vehicle applications.
In conclusion, rubber hose joints are vital components in automotive systems, serving as essential conduits for the transfer of fluids and gases while providing reliable sealing and flexibility. Their resilience to environmental factors, integrated functionality, and compliance with regulatory standards make these components indispensable for safe and efficient vehicle operation.
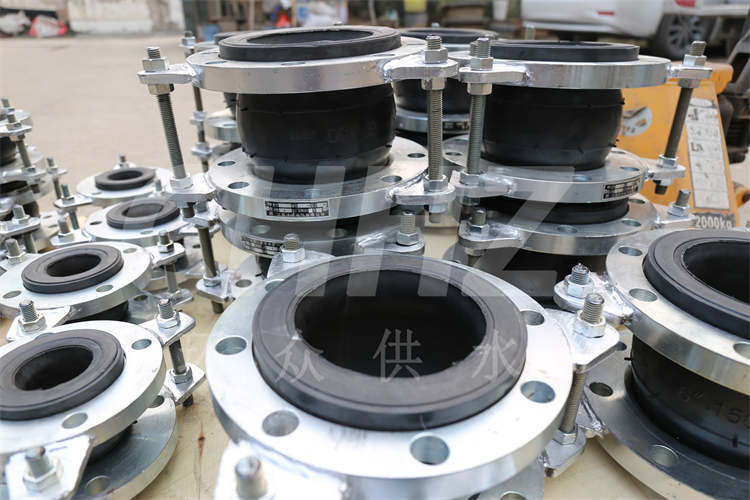