Design of Metal-Rubber Hose Joint Surfaces
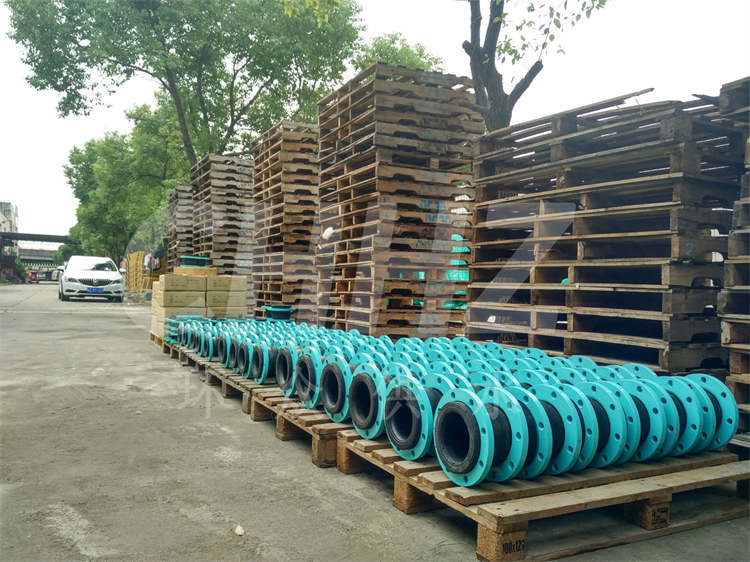
The design of metal-rubber hose joint surfaces is pivotal in ensuring the efficiency and longevity of fluid transfer systems. Proper surface design and treatment contribute to the prevention of leakage, corrosion, and mechanical failure, thereby enhancing the overall reliability and safety of the joint. Consideration of material compatibility, surface finish, and manufacturing processes is crucial in achieving optimal performance. Here is a comprehensive guide to the surface design of metal-rubber hose joints:
Material Selection: The choice of materials for the metal-rubber hose joint surfaces plays a central role in determining their performance. Select materials that are chemically compatible, exhibit suitable mechanical properties, and withstand environmental conditions. The metal should be corrosion-resistant and capable of providing a secure foundation for the rubber hose, while the rubber should be resilient, capable of maintaining a tight seal, and resistant to degradation.
Surface Roughness: The surface finish of both the metal and rubber components significantly impacts the performance of the joint. For metal surfaces, an appropriate level of roughness, typically achieved through processes like sandblasting or grinding, promotes enhanced adhesion and bonding with the rubber. Conversely, the rubber surface should have a textured or roughened profile to facilitate strong interlocking with the metal, thereby ensuring a reliable and durable union.
Surface Treatment: Surface treatment methods such as chemical etching, plasma treatment, or application of adhesion promoters can be employed to enhance the bonding characteristics of the metal and rubber surfaces. These treatments improve the surface energy and reactivity, promoting a robust bond between the two materials, increasing the joint's resistance to separation under stress, vibration, and other external forces.
Adhesive Application: The application of suitable adhesives tailored for metal-to-rubber bonding plays a pivotal role in ensuring a strong and durable joint. Properly chosen adhesives should exhibit compatibility with both metal and rubber, providing an effective interface for bonding while accommodating the unique thermal and mechanical properties of the materials.
Quality Control: Implementation of rigorous quality control measures throughout the manufacturing process is essential to verify the surface characteristics and properties of the metal-rubber hose joint surfaces. This includes non-destructive testing, dimensional inspection, and adhesion testing to confirm the integrity and reliability of the joint.
By meticulously considering the material properties, surface roughness, treatment processes, and quality assurance, the design of metal-rubber hose joint surfaces can be optimized for superior performance. An effectively designed and executed joint not only ensures the efficient transfer of fluids but also contributes to the longevity, reliability, and safety of the entire fluid transfer system.
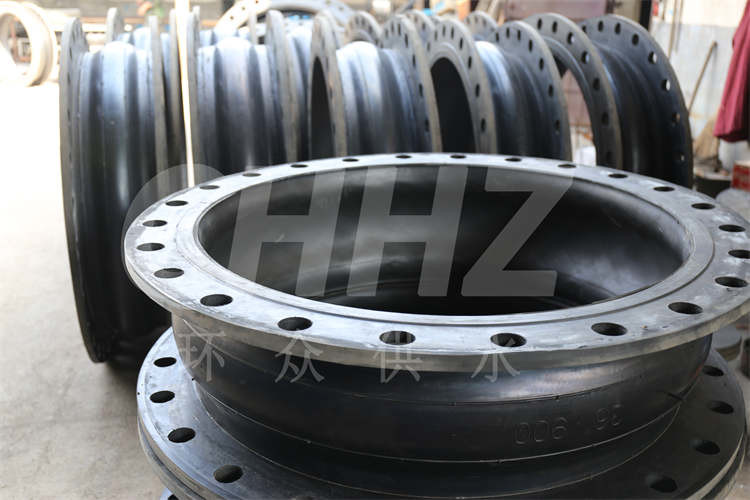