Plastic and Rubber Waterproof Seals: Best Practices for Applications
When it comes to waterproofing applications, the choice between plastic and rubber seals depends on the specific requirements and environmental conditions of the project. Understanding the characteristics, benefits, and best practices for using plastic and rubber waterproof seals is essential for ensuring effective moisture protection in various construction and industrial settings.
Plastic waterproof seals, such as PVC and thermoplastic elastomers, offer several advantages in terms of durability, chemical resistance, and ease of installation. These seals are commonly used in applications that require resistance to harsh chemicals, UV exposure, and extreme temperatures. Additionally, plastic seals are often preferred in environments where flexibility, low permeability, and dimensional stability are critical factors for maintaining effective waterproofing.
On the other hand, rubber waterproof seals, including EPDM and neoprene, are prized for their elasticity, resilience, and excellent resistance to weathering. Rubber seals are widely employed in applications where flexibility, impact resistance, and long-term performance under outdoor conditions are paramount. Moreover, rubber seals exhibit strong resistance to aging, ozone exposure, and are often the material of choice for sealing joints and connections in roofing, infrastructure, and automotive applications due to their superior sealing properties.
Selecting the most suitable material for waterproof seals is contingent on the specific demands of the project. Factors such as exposure to weather elements, anticipated movement in the structural components, and the chemical environment will dictate the optimal choice between plastic and rubber seals. For instance, outdoor construction projects subject to UV exposure and temperature fluctuations may benefit from the use of rubber seals, while indoor applications with chemical exposure might favor plastic seals. Understanding the unique requirements of the project environment is crucial for making an informed decision.
Additionally, proper installation and maintenance practices are essential regardless of the material chosen. Following manufacturer guidelines, ensuring proper surface preparation, and employing compatible adhesives or fastening systems are crucial steps for achieving reliable and long-lasting waterproofing performance.
In conclusion, the selection of plastic or rubber waterproof seals depends on the specific performance requirements and environmental conditions of the project. By carefully evaluating the unique properties of each material and adhering to best practices for installation and maintenance, construction, and industrial professionals can ensure effective moisture protection and long-term durability in their waterproofing applications.
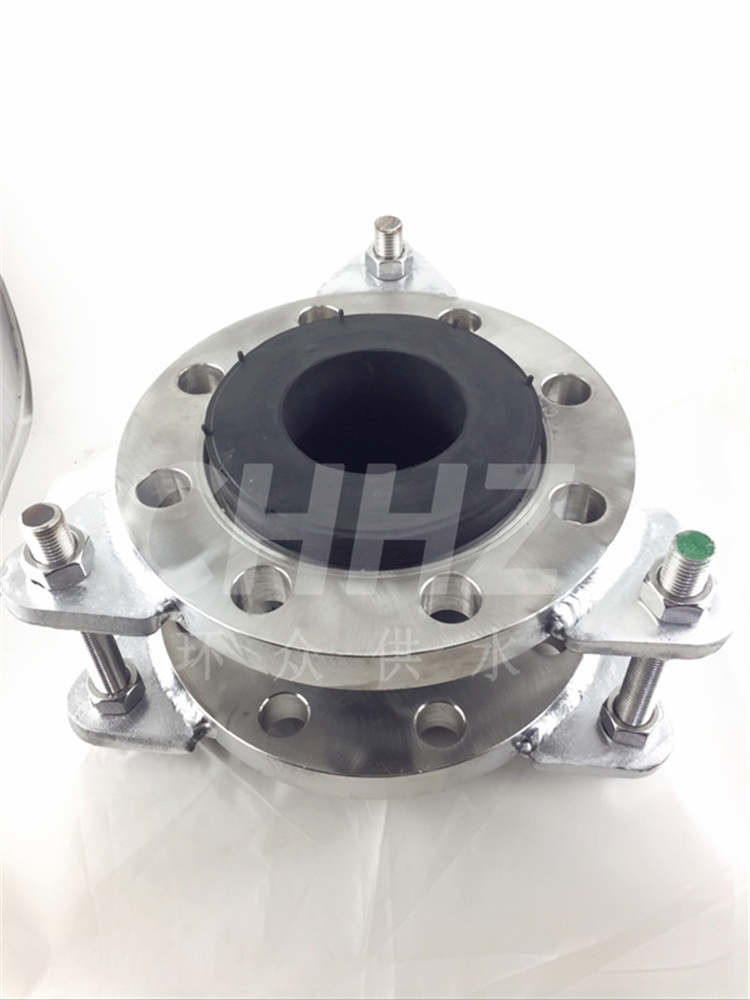