Plastic Joint Connections for Automobile Rubber Hoses
Plastic joint connections play a critical role in the automotive industry, particularly in connecting rubber hoses for fluid and air transfer within vehicles. This article focuses on the significance of plastic joint connections for attaching rubber hoses in automobiles, highlighting their functionality, durability, and impact on vehicle performance and safety.
Functionality and Design: Plastic joint connections serve as the interface between various rubber hoses in automotive systems, facilitating the transfer of fluids, such as coolant, fuel, and air. These connections are engineered to provide secure, leak-free seals, ensuring efficient flow of fluids throughout the vehicle's hydraulic, pneumatic, and cooling systems. Their design encompasses features such as barbed ends, threaded fittings, and compression mechanisms to securely grip and seal the rubber hoses.
Material Composition: The plastic used in joint connections for rubber hoses is typically a high-strength, engineered thermoplastic material, chosen for its resistance to chemical abrasion, temperature fluctuations, and mechanical stresses. Polypropylene, polyamide (nylon), and polyoxymethylene (acetal) are commonly employed due to their durability, lightweight nature, and compatibility with automotive fluids.
Resistance to Environmental Conditions: Automobiles operate in diverse environmental conditions, including temperature extremes, exposure to road salts, and engine bay heat. Plastic joint connections are designed to withstand these challenges, providing resistance to corrosion, UV degradation, and thermal expansion, ensuring the integrity and longevity of the fluid transfer system.
Weight Reduction and Cost Efficiency: The use of lightweight plastic joint connections contributes to overall weight reduction in vehicles, supporting fuel efficiency and reduced emissions. Furthermore, the cost-effective nature of plastic materials compared to traditional metal fittings contributes to the cost efficiency of manufacturing and maintenance of automobiles.
Performance and Safety: The reliable performance of plastic joint connections is critical to the safe and efficient operation of automotive systems. Securely connected rubber hoses, using these joints, guarantee the proper functioning of cooling, fuel delivery, and air intake systems, preventing leaks and ensuring optimal performance of the vehicle.
Ease of Installation and Maintenance: The design of plastic joint connections often incorporates user-friendly features, such as quick-connect mechanisms or simple, tool-free installation. This facilitates assembly during vehicle manufacturing and simplifies maintenance and repair procedures for automotive technicians, reducing downtime and labor costs.
Customization and Compatibility: Plastic joint connections are available in a variety of configurations and sizes, accommodating diverse hose diameters and system requirements in vehicles. Customized designs and connection types ensure compatibility with specific automotive applications, allowing for flexibility in the integration of fluid transfer systems within different vehicle models.
In conclusion, plastic joint connections for automobile rubber hoses are indispensable components that enable the efficient and reliable transfer of fluids and gases within automotive systems. Their resilience, lightweight construction, and cost-effectiveness contribute to the functionality, safety, and environmental performance of modern vehicles. By continually advancing materials and designs, plastic joint connections continue to play a pivotal role in enhancing the performance, efficiency, and sustainability of automotive technology.
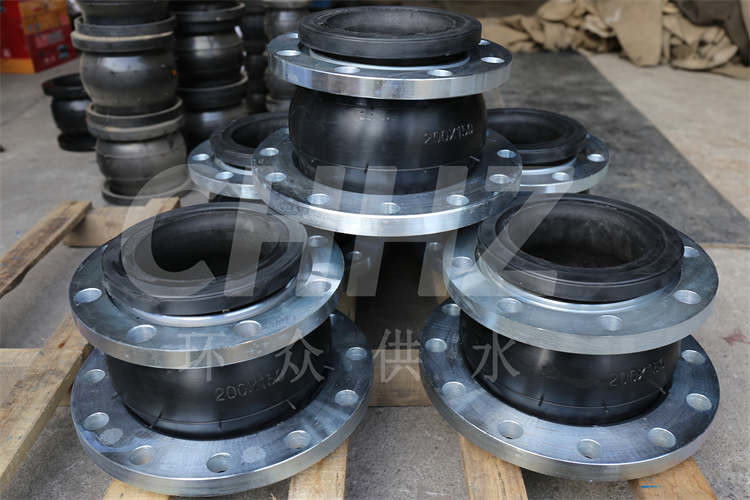