Creating a high-quality rubber-bonded joint
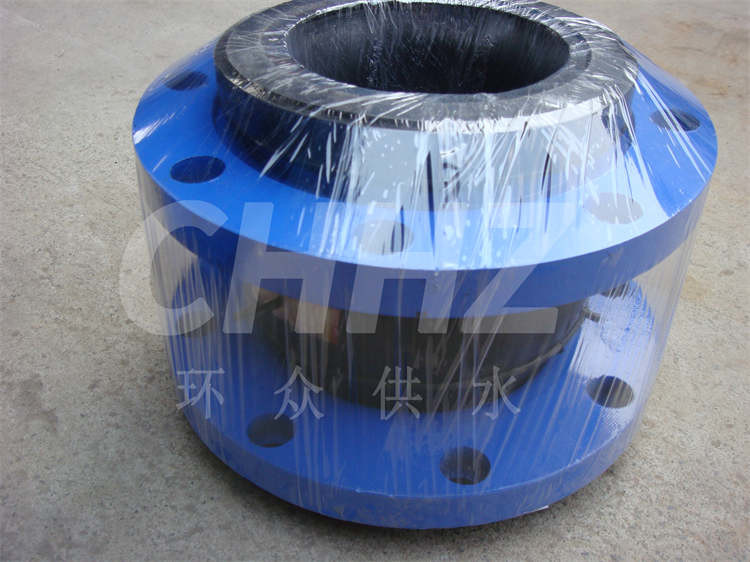
Creating a high-quality rubber-bonded joint requires careful attention to both the material properties and the mold used for the bonding process. The mold plays a crucial role in shaping and forming the rubber material to achieve the desired joint characteristics. In this article, we will discuss the key considerations and techniques for designing and using molds for rubber-bonded joints.
Mold design is a critical aspect of the rubber-bonding process. The mold must be carefully engineered to produce a joint that meets the required specifications for size, shape, and performance. The choice of mold material is essential, as it must be capable of withstanding the heat and pressure involved in the vulcanization process.
In addition to material selection, the design of the mold cavity and its features are vital for achieving a successful rubber-bonded joint. The mold cavity must be precisely shaped to create the desired geometry of the joint. This includes considerations for any undercuts, grooves, or other specific features required for the final joint configuration.
Furthermore, proper venting and gating in the mold are crucial to ensure the uniform flow of the rubber material and the release of air during the molding process. Adequate venting prevents trapped air from forming bubbles or voids in the final joint, leading to a more reliable bond.
The surface finish of the mold cavity is another critical factor. A smooth surface finish helps to achieve a quality rubber-bonded joint by providing a clean and precise mold release. It also minimizes the risk of imperfections or surface defects in the finished joint.
The selection of molding techniques, such as compression molding or transfer molding, also influences the design and use of the mold. Each technique requires specific considerations, and the mold design must be tailored to the chosen method to ensure optimal results.
In conclusion, the design and use of molds for rubber-bonded joints are essential for achieving high-quality and reliable joint products. Careful consideration of mold material, cavity design, venting, and gating, as well as the surface finish, is crucial for successful rubber bonding. By paying close attention to these factors and tailoring the mold to the specific requirements of the joint, manufacturers can consistently produce superior rubber-bonded joints that meet the highest standards of performance and durability.
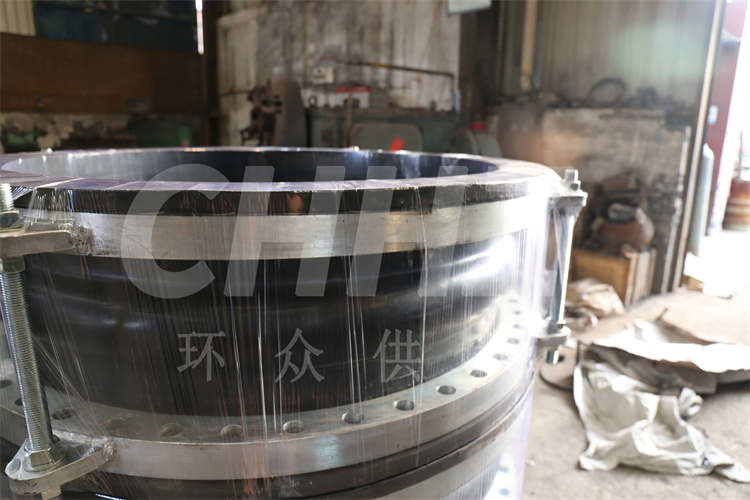