Concrete Joint Sealing with Rubber Waterstop: Construction Methods
Introduction: Concrete structures require effective joint sealing to prevent water infiltration and ensure structural integrity. Rubber waterstops serve as vital components in the construction of watertight concrete joints. This article discusses the methods and best practices for utilizing rubber waterstops to seal concrete joints, emphasizing the importance of proper installation techniques and material selection for long-term performance.
Material Composition and Design: Rubber waterstops are specially formulated to exhibit high elasticity, durability, and resistance to water pressure and chemical exposure. These waterstops are commonly manufactured from synthetic rubber compounds, PVC, or thermoplastic elastomers, providing robustness and flexibility to accommodate concrete movements while effectively sealing joints. The design of rubber waterstops includes various profiles and configurations tailored to different joint types and load requirements, ensuring compatibility with diverse concrete construction applications.
Installation Techniques: The successful installation of rubber waterstops in concrete joints is crucial to achieving effective waterproofing and preventing leakages. Prior to installation, the joint surfaces must be clean, dry, and free from contaminants to facilitate proper adhesion and sealing. The rubber waterstop is then positioned within the joint gap, ensuring sufficient embedment depth to secure it in place. Proper anchoring and termination details, such as heat welding or mechanical fixing, are employed to ensure continuous and secure sealing along the joint length. Careful attention to corner and intersection details is essential to maintain the integrity of the waterproofing system.
Integration with Formwork and Concrete Placement: During concrete pouring, the rubber waterstop must be integrated seamlessly with the formwork to maintain its position and alignment. Formwork design and construction should allow for the correct placement of waterstops without compromising their integrity. Concrete placement around the waterstop should be carried out with care to avoid displacing or damaging the sealing material. Vibrating the concrete ensures proper consolidation around the waterstop, promoting optimal adhesion and contact with the joint surfaces.
Post-Placement Quality Checks: Following the concrete curing process, thorough quality checks of the sealed joints are conducted to verify the effectiveness of the rubber waterstop installation. Visual inspections and, if necessary, water or air pressure testing are performed to detect any leaks or defects in the joint sealing. Any identified issues are addressed promptly to rectify potential vulnerabilities and uphold the watertight integrity of the concrete structure.
Long-Term Performance and Maintenance: Properly installed rubber waterstops contribute to the long-term waterproofing and durability of concrete joints, minimizing the risk of water-related damage and preserving the structural stability of the construction. Regular maintenance inspections are recommended to monitor the condition of the waterstops, ensuring their continued effectiveness in preventing water ingress and sustaining the performance of the concrete elements.
Conclusion: Effective sealing of concrete joints with rubber waterstops is fundamental to achieving watertight and durable structures. By adopting appropriate installation methods, integrating waterstops seamlessly with formwork, and conducting thorough quality checks, construction professionals can ensure the reliable performance of rubber waterstops in concrete joint sealing. These practices contribute to the longevity and integrity of concrete structures, offering essential protection against water infiltration and promoting sustainable construction practices.
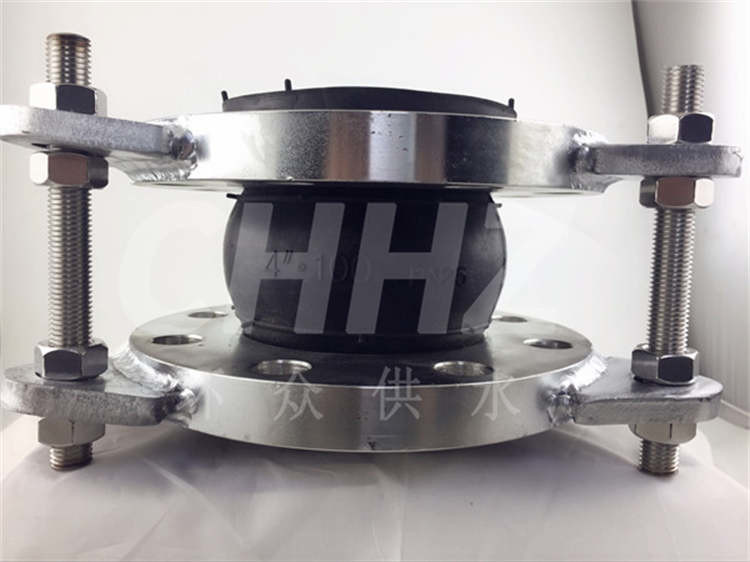