Connecting Industrial Rubber Belts: Methods and Considerations
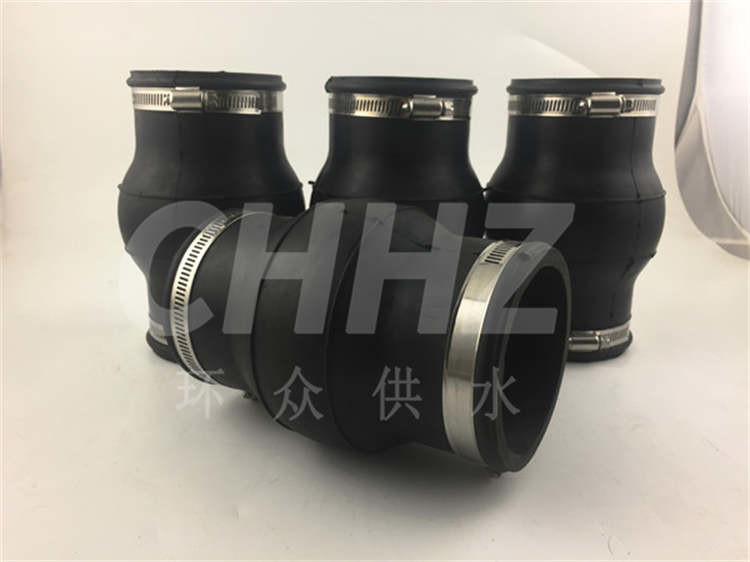
Industrial rubber belts are integral components in various manufacturing, mining, and processing applications. Connecting these belts appropriately is crucial to ensure smooth operation and minimize downtime. In this article, we will discuss various methods and considerations for connecting industrial rubber belts.
Mechanical Fasteners: Mechanical fasteners are a popular choice for joining rubber belts. These fasteners typically consist of metal or plastic plates with rivets or bolts. They offer quick and easy installation and are suitable for a wide range of belt widths. However, proper alignment and tensioning are crucial for optimal performance.
Vulcanized Splicing: Vulcanized splicing involves using heat, pressure, and adhesive materials to create a strong, seamless joint between the belt ends. This method offers excellent strength and integrity, making it suitable for heavy-duty applications. It ensures smooth belt operation and reduces the risk of belt creep or slippage.
Overlapping and Bonding: Overlapping the belt ends and bonding them using adhesives is another method for connecting rubber belts. This approach creates a continuous and flexible joint, particularly suitable for applications with smaller pulleys or where mechanical fasteners may not be ideal.
Step-Lap Splicing: Step-lap splicing involves shaping each belt end to interlock with the other, creating a larger contact area for bonding or vulcanization. This method improves load distribution and reduces stress concentration at the joint, enhancing the longevity of the spliced belt.
Considerations for Belt Connection: When connecting industrial rubber belts, several factors must be considered to ensure a reliable and efficient joint.
Belt Alignment: Proper alignment of the belt ends is critical to prevent uneven tension and premature wear. Misaligned belts can also lead to tracking issues and increased maintenance requirements.
Tensioning: Achieving the correct tension in the spliced belt is essential for optimal performance. Overly tight or loose belts can result in excessive stress on the joint or slippage during operation.
Application-Specific Factors: The operating environment, load conditions, and speed of the conveyor or processing equipment should influence the choice of belt connection method. For example, heavy-duty applications may require vulcanized splicing for superior strength and durability.
In conclusion, connecting industrial rubber belts involves a careful assessment of the application requirements and the selection of an appropriate splicing method. Mechanical fasteners, vulcanized splicing, overlapping and bonding, and step-lap splicing are common techniques, each offering unique advantages depending on the application. Attention to alignment, tensioning, and specific operational factors is crucial for ensuring optimal belt performance and longevity.
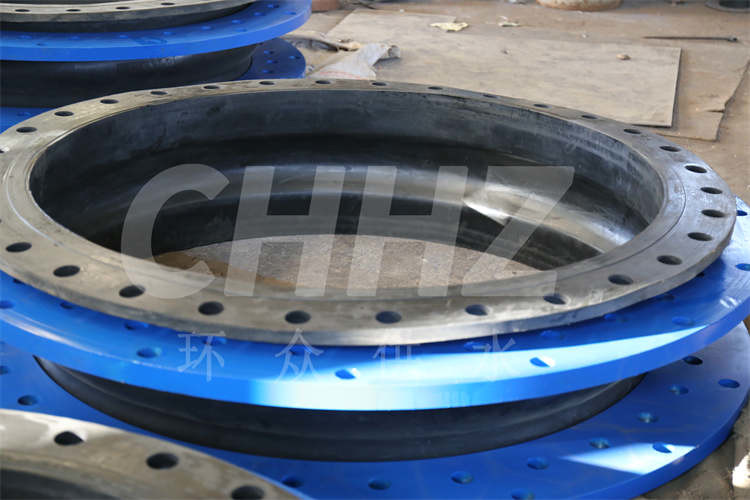