Manufacturing Process of Rubber Cable Joints
Introduction: The manufacture of rubber cable joints involves a precise and detailed process to ensure the production of reliable and durable electrical components. This article provides an overview of the essential molding techniques and steps involved in the fabrication of rubber cable joints.
Molding Techniques:
Compression Molding: The process involves placing the rubber material into a heated mold cavity and applying pressure to achieve the desired shape and dimensions. The application of heat and pressure allows the rubber to flow and conform to the mold, resulting in a uniform and tightly compacted cable joint component.
Injection Molding: This process involves injecting molten rubber material into a closed mold under high pressure. The material fills the mold cavity, taking its shape, and then cools and solidifies to form the cable joint component. Injection molding offers precise control over the molding process, resulting in complex and intricate cable joint designs.
Transfer Molding: In this technique, the rubber material is preheated in a chamber before being pushed into the mold cavity. The application of pressure forces the material to flow into the mold to form the cable joint component. Transfer molding is suitable for producing cable joints with detailed features and consistent dimensions.
Vulcanization: Following the molding process, the rubber cable joint undergoes vulcanization, which involves subjecting the component to heat and pressure. This crucial step enhances the properties of the rubber, such as its strength, elasticity, and resistance to environmental factors. Vulcanization ensures that the rubber cable joint achieves the necessary mechanical and electrical characteristics for its intended application.
Reinforcement and Insulation: Depending on the specific requirements of the cable joint, additional reinforcement materials such as fibers or textiles may be incorporated into the rubber during the molding process. These reinforcements enhance the mechanical strength and structural integrity of the cable joint. Furthermore, the insulation properties of the rubber are critical in ensuring the electrical safety and performance of the cable joint assembly.
Curing and Finishing: Upon completion of the molding and vulcanization processes, the cable joint undergoes curing to allow the rubber material to set and attain its final properties. Subsequently, the finished cable joint may undergo surface treatments, such as coatings or protective layers, to enhance its resistance to environmental factors such as moisture, chemicals, and abrasion.
Quality Assurance and Testing: Throughout the manufacturing process, stringent quality control measures are implemented to ensure the dimensional accuracy, material consistency, and electrical properties of the rubber cable joints. In addition, the finished cable joints undergo rigorous testing, including electrical conductivity, insulation resistance, and environmental exposure tests, to verify their performance and compliance with industry standards.
Conclusion: In conclusion, the manufacturing process of rubber cable joints encompasses a series of molding, vulcanization, and finishing techniques to produce high-quality electrical components. The precision and attention to detail in each stage of fabrication result in durable and reliable cable joints that meet the demanding requirements of electrical installations and applications.
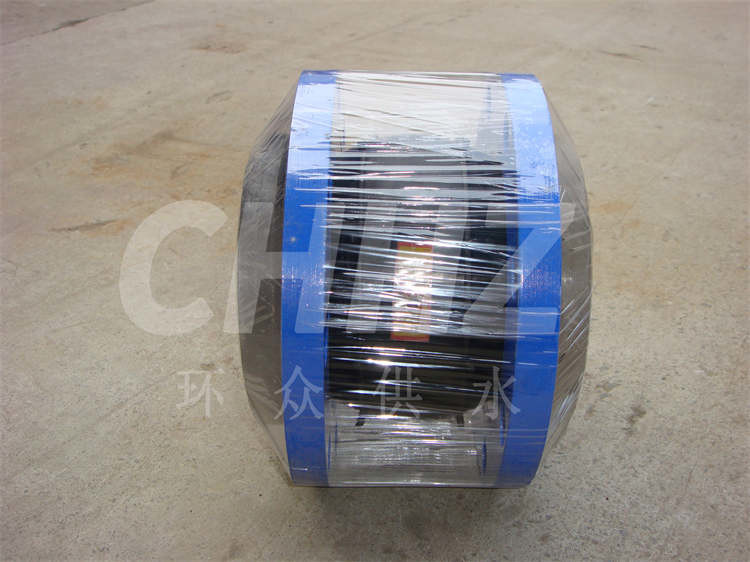