Requirements for Rubber Joint Vulcanization Workshop
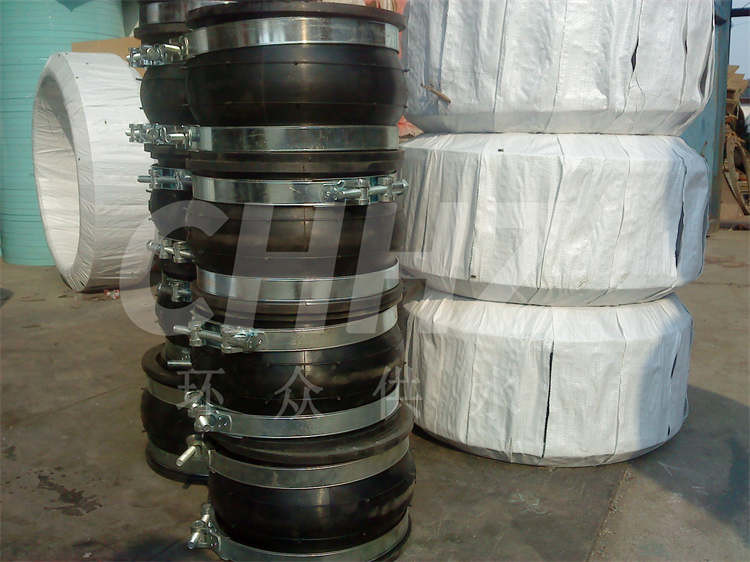
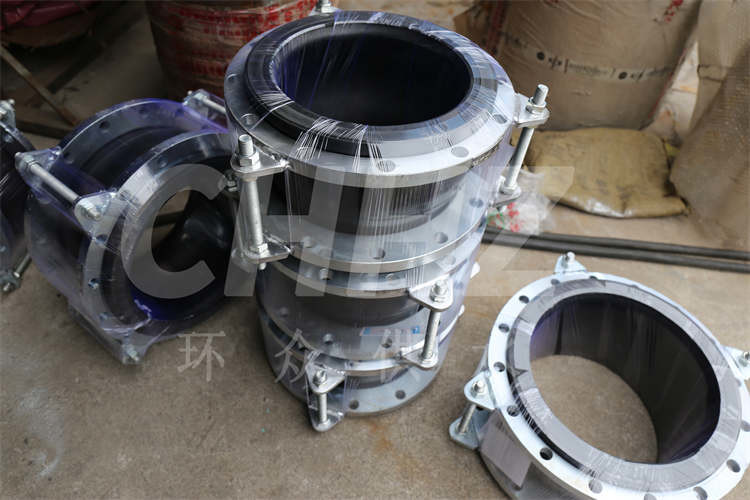
A rubber joint vulcanization workshop is an essential part of the rubber manufacturing process, where raw rubber materials are transformed into durable and versatile rubber joint products. The successful operation of such a workshop depends on a range of requirements encompassing safety, equipment, processes, and quality control. Adhering to these requirements is crucial for ensuring the production of high-quality rubber joints and maintaining a safe and efficient working environment.
Safety is paramount in a rubber joint vulcanization workshop. Employees must adhere to strict safety protocols, including the proper use of personal protective equipment such as gloves, goggles, and face shields. Additionally, the workshop should be equipped with safety features such as emergency shut-off controls, ventilation systems, and fire suppression equipment to mitigate potential hazards.
Furthermore, the workshop must be outfitted with state-of-the-art equipment to effectively carry out the vulcanization process. This includes vulcanizing machines, autoclaves, and molds designed to withstand the high temperatures and pressures necessary for the vulcanization of rubber compounds. Regular maintenance and calibration of this equipment are essential to ensure consistent and reliable performance.
The vulcanization process itself requires strict adherence to established procedures and best practices. This includes precise control of temperature, pressure, and curing time to achieve the desired physical properties of the rubber joints. Proper documentation of process parameters and a robust quality control system are essential for monitoring and maintaining product consistency and reliability.
Quality assurance is a critical aspect of a rubber joint vulcanization workshop. Quality control measures involve extensive testing of raw materials, in-process samples, and finished products to ensure compliance with industry standards and customer requirements. This may encompass tests for tensile strength, elongation, hardness, and resistance to various environmental conditions.
An effective quality management system, such as ISO 9001 certification, can help formalize and streamline quality control processes in the workshop. By adhering to recognized quality management standards, the workshop can demonstrate its commitment to producing high-quality rubber joint products, thereby enhancing customer confidence and satisfaction.
In addition to these requirements, the workshop should also prioritize environmental sustainability by implementing practices for waste management, energy efficiency, and the responsible use of resources. This may involve recycling and reusing materials, optimizing energy consumption, and complying with environmental regulations to minimize the workshop's ecological footprint.
Moreover, continuous improvement and innovation are crucial for the long-term success of a rubber joint vulcanization workshop. By investing in research and development, as well as ongoing training for employees, the workshop can stay at the forefront of technological advancements and industry best practices, driving product innovation and operational excellence.
In conclusion, a rubber joint vulcanization workshop requires a comprehensive approach to safety, equipment, processes, and quality control to ensure the production of high-quality rubber joint products. By meeting these requirements and embracing a commitment to safety, efficiency, and innovation, the workshop can maintain its competitive edge and contribute to the advancement of the rubber manufacturing industry.
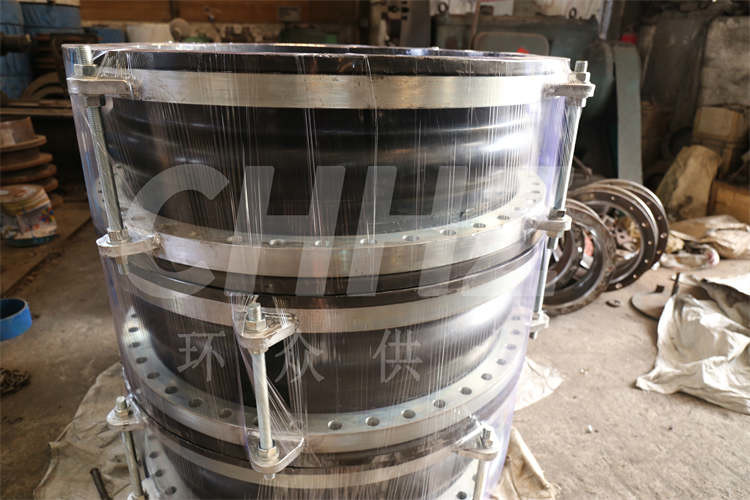