Rubber Hose Joint Processing Explained
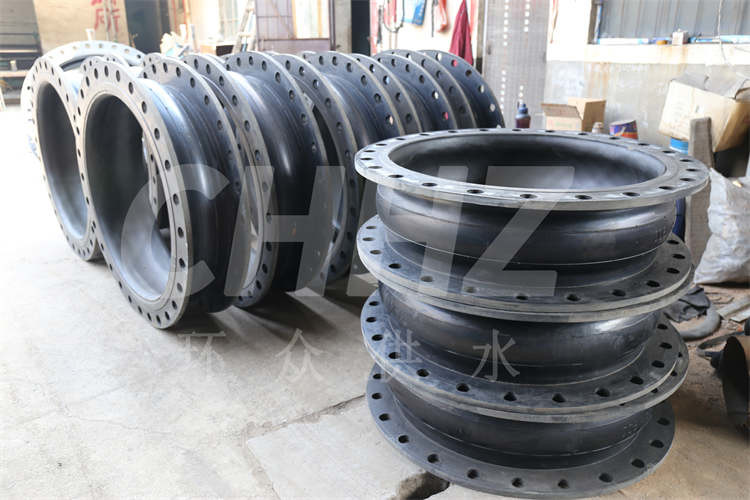
When it comes to creating a durable and reliable connection in a piping system, the processing of rubber hose joints is a crucial aspect that requires precision and attention to detail. In this article, we will delve into the essential steps involved in the processing of rubber hose joints, outlining the key techniques and considerations employed in ensuring the quality and functionality of these critical components.
Material Selection: The first step in the processing of rubber hose joints is the careful selection of materials. High-quality rubber compounds that offer excellent flexibility, resilience, and chemical resistance are preferred. The specific material chosen depends on the intended application, with considerations for factors such as temperature, pressure, and the nature of the conveyed fluid.
Cutting and Shaping: Once the suitable rubber material is chosen, the next step involves cutting and shaping the material to form the desired joint. Precision cutting techniques, such as die-cutting or water jet cutting, are employed to create uniform and accurate shapes. The rubber material is then shaped and molded to achieve the required dimensions and contours, ensuring a secure and effective fit within the piping system.
Reinforcement and Layering: In many cases, rubber hose joints require additional reinforcement to enhance their structural integrity and resistance to pressure and mechanical stress. This involves the incorporation of fabric or wire reinforcements within the rubber material, providing added strength and durability. Multiple layers of rubber may also be applied, each serving a specific purpose such as weather resistance, abrasion protection, or fluid containment.
Vulcanization: Vulcanization is a critical process in the production of rubber hose joints, involving the application of heat and pressure to the rubber material. This results in the cross-linking of polymer chains within the rubber, leading to improved strength, elasticity, and resistance to environmental factors. The vulcanization process is carefully controlled to ensure uniformity and consistency across the entire joint, contributing to its overall performance and longevity.
End Fitting Attachment: The final step in the processing of rubber hose joints involves the attachment of end fittings, which provide the means for connecting the joint to the piping system. This may involve techniques such as crimping, swaging, or the use of adhesive bonds, depending on the specific requirements of the application. The attachment of end fittings must be performed with precision to ensure a leak-free and secure connection.
Quality Control and Testing: Throughout the entire processing of rubber hose joints, stringent quality control measures are implemented to verify the dimensional accuracy, material integrity, and overall performance of the finished components. Furthermore, testing procedures such as pressure testing, leak testing, and visual inspection are conducted to ensure that the joints meet the necessary standards and specifications.
In conclusion, the processing of rubber hose joints requires a meticulous approach to ensure the production of high-quality components that meet the stringent demands of modern piping systems. By carefully selecting materials, employing precise cutting and shaping techniques, incorporating reinforcement, and adhering to strict quality control measures, manufacturers can produce rubber hose joints that exhibit superior performance, durability, and reliability in diverse industrial applications.
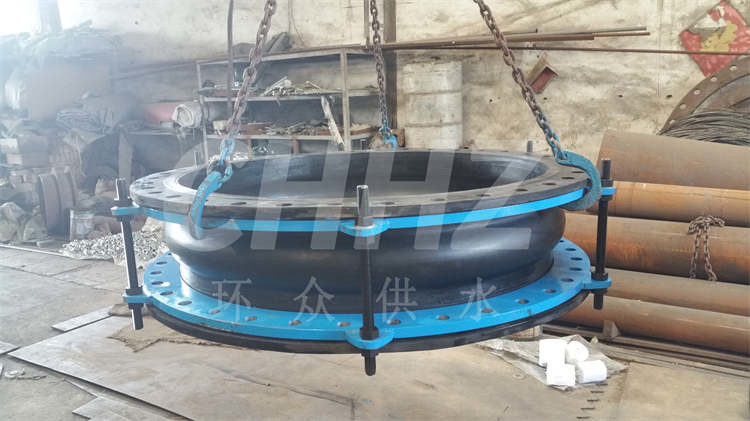