Designing a Flexible Rubber Joint Mold
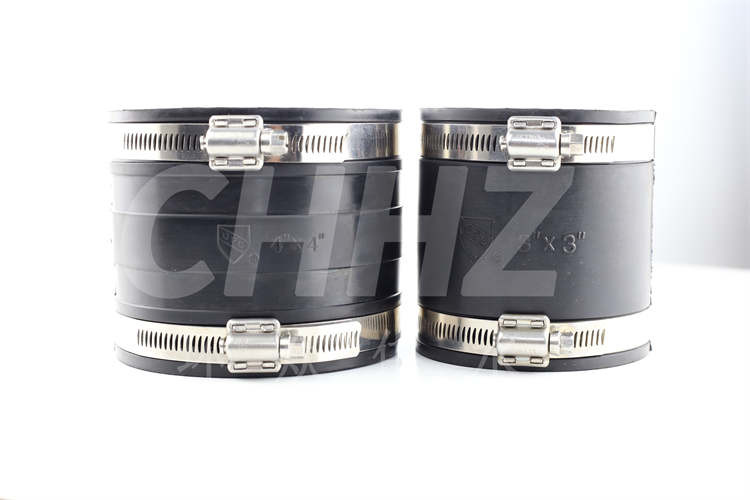
The design and manufacture of a mold for flexible rubber joints is a critical component of the production process. Ensuring that the mold is meticulously crafted is essential to achieving high-quality and consistent rubber joints. This article provides a comprehensive guide for designing a mold for flexible rubber joints.
Design Considerations:
Material Selection: The chosen material for the mold must possess high heat resistance, durability, and dimensional stability to withstand the molding process and produce accurate and reproducible results. Common materials for mold construction include metal alloys, such as aluminum or steel, and various elastomers.
Mold Geometry: The mold's geometry should accurately reflect the desired dimensions, shape, and surface finish of the flexible rubber joint. Consideration should be given to the parting line, draft angles, and venting to facilitate the release of air and gases during the molding process.
Incorporating Flexibility: Given the nature of flexible rubber joints, the mold design should allow for the accommodation of elasticity and flexibility in the final product. This may involve the inclusion of features that enable controlled expansion and contraction of the rubber during molding.
Runners and Gates: The mold should incorporate runners and gates that facilitate the controlled flow of the rubber material into the mold cavity. Proper design of these features contributes to the uniform distribution of the material and minimizes the risk of defects in the finished product.
Heat Transfer: Effective heat transfer within the mold is vital for ensuring consistent curing and vulcanization of the rubber. The design should enable optimal heat distribution to achieve uniform material properties across the joint.
Manufacturing Process:
CAD Modeling: Begin the mold design process by creating a detailed 3D model of the flexible rubber joint mold using computer-aided design (CAD) software. The model should accurately capture all dimensions, features, and specifications of the intended mold.
Prototyping and Testing: Utilize rapid prototyping techniques to create a physical prototype of the mold for evaluation and testing. This step allows for the assessment of form, fit, and function prior to full-scale production.
Precision Machining: Once the design has been validated, precision machining processes, such as CNC milling or EDM (electrical discharge machining), are employed to produce the mold from the selected material. Attention to tolerances and surface finishes is crucial at this stage.
Surface Treatment: Surface treatments, such as polishing, coating, or texturing, may be applied to the mold to enhance release properties, surface finish, and overall durability.
Quality Assurance: Rigorous inspection and testing of the completed mold ensure that it meets all design specifications and regulatory requirements. This includes dimensional checks, material integrity, and functionality assessments.
By meticulously adhering to the aforementioned considerations and manufacturing processes, the resulting mold for flexible rubber joints will demonstrate the precision, durability, and performance required to consistently produce high-quality rubber joints for various industrial applications.
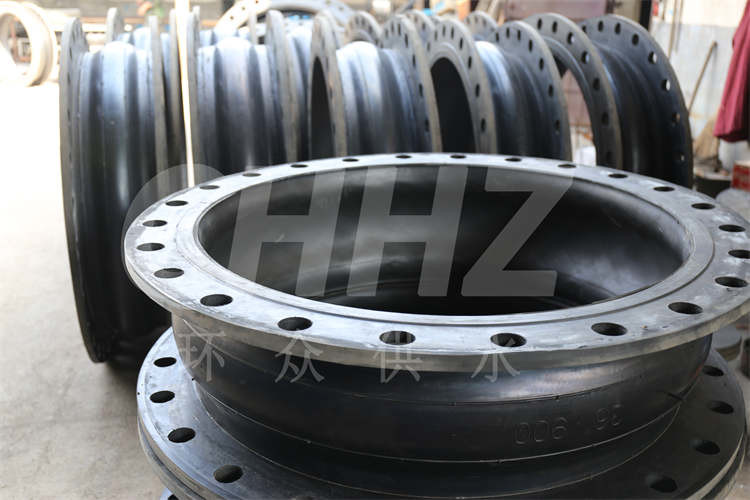