Proper Crimping of Rubber Insulated Cable Copper Connectors
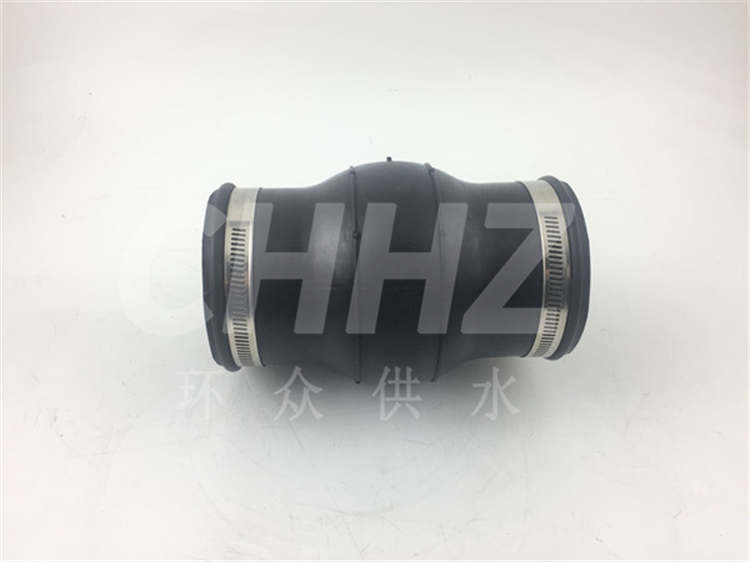
Crimp connections play a fundamental role in ensuring secure and reliable electrical connections. When dealing with rubber insulated cable copper connectors, employing proper crimping techniques is essential to maintain the integrity of the electrical system. This article focuses on the correct crimping method for rubber insulated cable copper connectors, highlighting the importance of adherence to standard practices for reliable electrical conductivity and safety.
Equipment and Materials:
Crimping Tool: Select a high-quality crimping tool designed for the specific dimensions of the copper connector and the rubber insulated cable. The tool must provide sufficient force to create a robust and enduring crimp connection.
Copper Connectors: Utilize copper connectors with appropriate dimensions, designed to accommodate the gauge and insulation of the rubber cable. The connectors must be of high conductivity and durability, ensuring minimal electrical resistance and long-term performance.
Rubber Insulated Cable: Ensure the rubber insulated cable is appropriately sized for the application, with insulation suited to the electrical voltage and environmental conditions. The cable should be free from damage and securely stripped to allow seamless crimping.
Proper Crimping Procedure:
Stripping the Cable: Strip the rubber insulation from the cable end, exposing the bare conductor. The length of the exposed conductor should align with the requirements specified by the connector manufacturer.
Insertion of Cable: Insert the stripped cable end into the copper connector, verifying that it makes full contact with the connector's surface. Proper positioning within the connector is essential to establish an effective electrical connection.
Crimping Process: Place the connector and cable assembly into the crimping tool, ensuring that the connector is aligned with the appropriate crimping cavity. Apply firm, uniform pressure to the tool's handles, creating a complete crimp onto the connector without deforming or causing damage to the connector or conductor.
Visual Inspection: Upon completion of the crimping process, visually inspect the crimped connection for any signs of irregularities, such as surface deformities, exposed conductors, or incomplete crimps. Any deficiencies should warrant rework or replacement of the connection.
Adherence to Standards: It is imperative to comply with industry standards and manufacturer specifications when crimping rubber insulated cable copper connectors. These standards outline the acceptable dimensions, crimping profiles, and performance criteria that ensure the conductivity and mechanical strength of the connections.
A proper crimping process for rubber insulated cable copper connectors guarantees the establishment of reliable electrical connections essential for safe and efficient electrical systems. By following prescribed techniques and utilizing suitable tools and materials, electrical installers and maintenance personnel can uphold the quality and reliability of electrical connections within diverse applications.
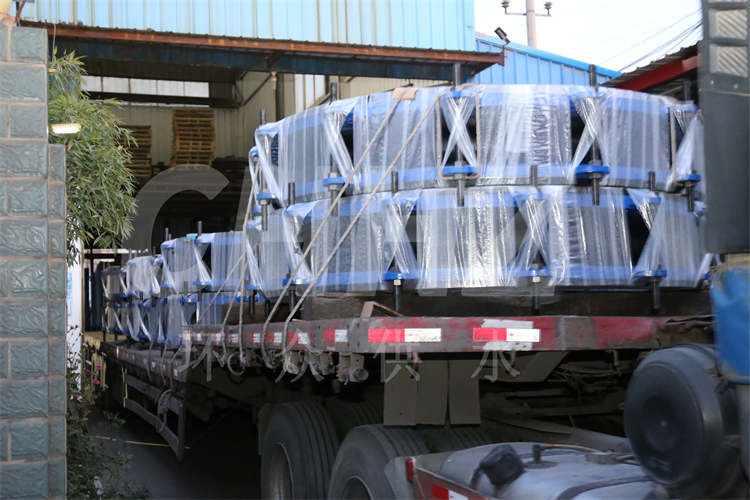