Forms of Plastic or Rubber Waterproof Strip Joints
Plastic and rubber waterproof strips are essential components in construction and civil engineering projects, serving to prevent water seepage and ensure the integrity of building structures. This article explores the various forms of joints used in plastic or rubber waterproof strips, highlighting their importance, characteristics, and applications in diverse construction scenarios.
Types of Joints:
Adhesive Bonding Joints: Adhesive bonding joints involve the use of specialized adhesives to secure the plastic or rubber waterproof strips to different structural elements. This form of joint provides a seamless and water-tight connection, effectively sealing gaps and crevices to prevent water intrusion. Adhesive bonding joints are particularly suitable for joining waterproof strips to concrete, metal, or other building materials, offering a durable and reliable waterproofing solution.
Heat Welding Joints: In heat welding joints, plastic waterproof strips are fused together using heat, creating a strong and impermeable bond. This method is commonly employed for joining thermoplastic waterproof strips, such as PVC or TPO membranes, and is especially effective in roofing and underground waterproofing applications. Heat welding joints ensure airtight and watertight connections, enhancing the overall resilience of the waterproofing system.
Mechanical Fastening Joints: Mechanical fastening joints utilize mechanical fixings, such as screws, bolts, or fasteners, to secure rubber or plastic waterproof strips to structural elements. This form of joint offers ease of installation, maintenance, and retro-fitting, making it suitable for a wide range of applications, including façade cladding, expansion joints, and curtain wall systems. Mechanical fastening joints provide a robust and adaptable solution for joining waterproof strips in construction projects, accommodating variations in substrate materials and surface conditions.
Importance in Construction: The joints in plastic or rubber waterproof strips are crucial for ensuring the effectiveness and longevity of waterproofing systems in buildings, bridges, tunnels, and other infrastructure projects. Properly executed joints play a pivotal role in preventing water ingress, minimizing the risk of structural deterioration, mold growth, and damage to interior spaces. By selecting the appropriate joint form based on the specific application and performance requirements, construction professionals can enhance the waterproofing performance and durability of the overall building envelope.
Applications: Plastic or rubber waterproof strip joints find wide-ranging applications in various construction scenarios, including but not limited to roof waterproofing, basement and foundation waterproofing, expansion joint sealing, and façade cladding. The versatility and adaptability of different joint forms make them suitable for addressing diverse waterproofing challenges, contributing to the construction industry's efforts in creating resilient and sustainable built environments.
Conclusion: In conclusion, plastic and rubber waterproof strip joints are integral to the effectiveness and performance of waterproofing systems in construction and civil engineering projects. The selection of the appropriate joint form is essential in ensuring the durability, water-tightness, and structural integrity of the building envelope. By understanding the significance and application of different joint forms, architects, engineers, and construction professionals can make informed decisions to optimize the waterproofing performance and longevity of their projects.
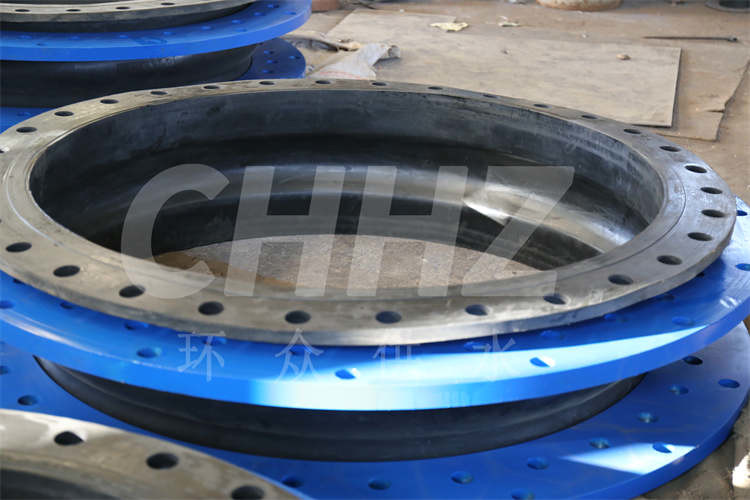