Connections of Plastic or Rubber Waterstops: A Technical Overview
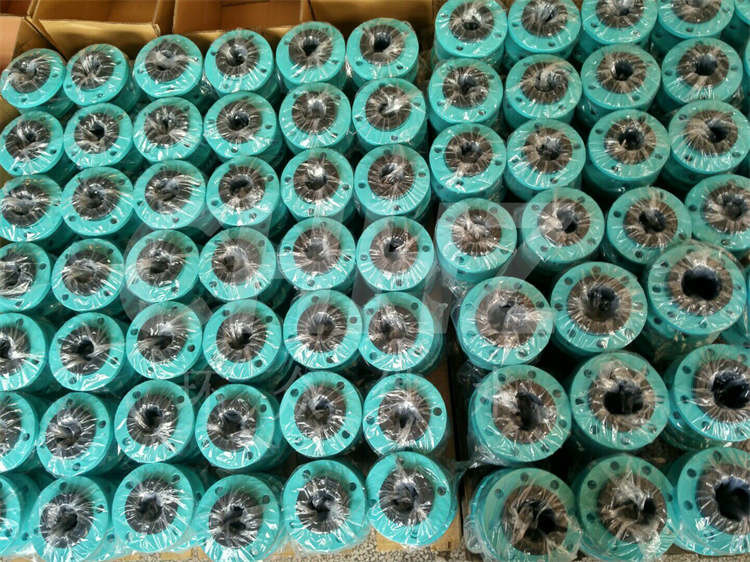
Introduction Waterstops are crucial elements in construction and civil engineering projects, designed to prevent the passage of water through concrete joints and expansion or construction joints. In this article, we will focus on the technical aspects of connecting and joining plastic or rubber waterstops, providing insight into the methods and considerations involved in ensuring effective waterproofing solutions.
Connecting Plastic Waterstops Plastic waterstops are commonly used to create watertight seals in construction joints and expansion joints. To achieve reliable connections, the ends of the plastic waterstops need to be securely joined. Common methods for connecting plastic waterstops include heat welding, solvent welding, and mechanical connections. Heat welding involves using a hot air gun to melt and fuse the ends of the waterstops, creating a seamless and durable joint. Solvent welding utilizes chemical adhesives to bond the waterstop ends together, ensuring a strong and waterproof connection. Mechanical connections, such as interlocking or clamping systems, provide an alternative approach for joining plastic waterstops, offering flexibility in installation and allowing for movement accommodation.
Joining Rubber Waterstops Rubber waterstops are highly flexible and durable, making them suitable for various construction applications. When joining rubber waterstops, the use of vulcanization or adhesive bonding is common. Vulcanization involves applying heat and pressure to the adjoining ends of the rubber waterstops, causing them to bond and create a robust, integrated joint. Adhesive bonding, using specialized adhesives optimized for rubber materials, provides an efficient and effective method of joining rubber waterstops, ensuring secure connections and excellent water resistance.
Considerations for Effective Connections When connecting plastic or rubber waterstops, it is essential to consider factors such as joint design, compatibility of materials, and environmental conditions. Proper joint design, including overlapping and chamfering of the waterstop ends, facilitates robust connections and prevents potential water leakage. Additionally, ensuring that the materials used for joining are compatible with the waterstops is critical for achieving durable and long-lasting connections. Environmental conditions, such as temperature variations and exposure to chemicals, should also be taken into account to select appropriate connection methods that maintain the integrity of the waterstops under all circumstances.
Conclusion The connections of plastic or rubber waterstops play a pivotal role in establishing effective waterproofing solutions in construction projects. Understanding the methods and considerations involved in joining waterstops is essential for achieving watertight seals and preventing water ingress through concrete joints. By employing suitable connection techniques and ensuring proper installation, the performance and longevity of plastic or rubber waterstops can be maximized, contributing to the overall durability and water resistance of concrete structures.
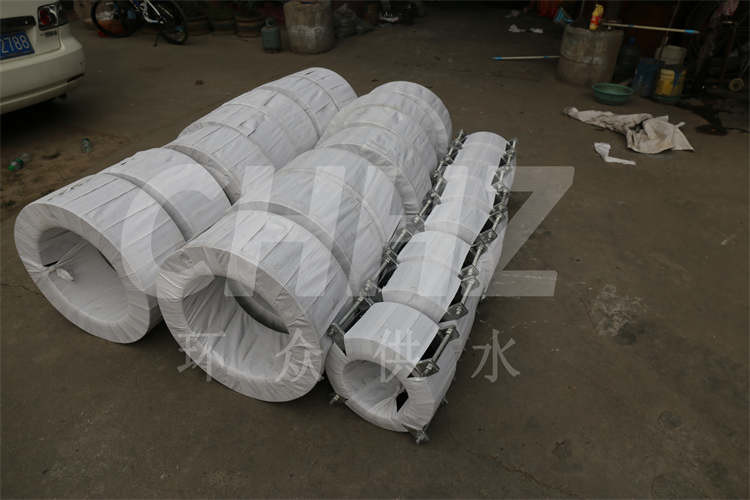