Rubber Hose Joint Manufacturing Process
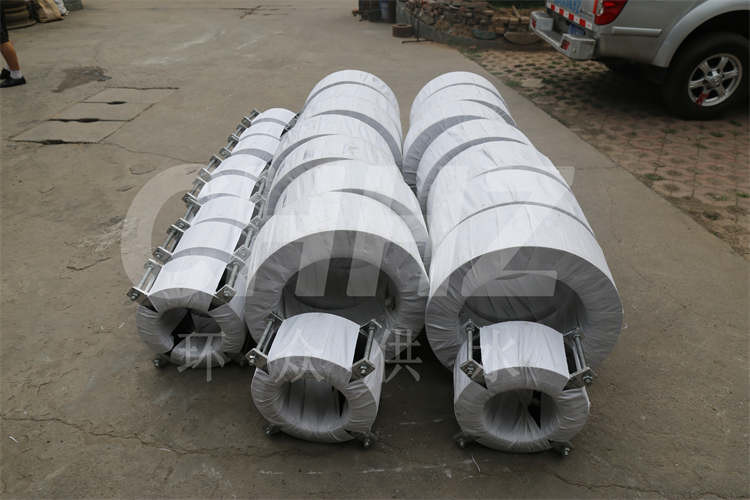
The manufacturing of rubber hose joints involves a series of intricate processes to ensure the production of high-quality, durable components. This article provides an overview of the key steps involved in the manufacturing process of rubber hose joints, highlighting the critical stages and techniques employed to achieve precision and reliability.
Material Selection: The manufacturing process begins with the careful selection of high-quality rubber materials that possess the necessary characteristics, such as resilience, flexibility, and chemical resistance. The choice of materials is critical to ensuring that the finished rubber hose joints meet the specific performance requirements for different applications.
Blending and Preparation: Once the raw materials are selected, they undergo a blending process to achieve the desired properties and consistency. This involves precise mixing of rubber compounds, additives, and curing agents to create a homogeneous blend that will exhibit the required mechanical and chemical properties. Subsequently, the blended material undergoes careful preparation, which may include milling and extrusion, to form continuous strips or sections of rubber ready for molding.
Molding and Vulcanization: The pre-processed rubber material is then shaped using specialized molding techniques to form the desired configurations of rubber hose joints. This may involve compression molding, injection molding, or transfer molding, depending on the complexity and specifications of the joints. Following the molding process, the rubber hose joints undergo vulcanization, a key step that imparts durability and stability to the rubber compound. Vulcanization involves subjecting the molded components to controlled heat and pressure to induce cross-linking of polymer chains, resulting in improved strength, elasticity, and resistance to environmental factors.
Surface Treatment and Assembly: Surface treatment processes, such as trimming and polishing, are carried out to refine the appearance and dimensions of the rubber hose joints, ensuring that they meet precise tolerances and aesthetic standards. In cases where metal or other components are integrated into the joints, assembly processes, such as bonding or mechanical fixation, are employed to create robust and functional interfaces between the rubber and other materials.
Quality Control and Testing: Throughout the manufacturing process, stringent quality control measures are implemented to assess the dimensional accuracy, material integrity, and performance attributes of the rubber hose joints. This includes the inspection of physical properties, such as hardness, tensile strength, and elongation, as well as conducting tests to evaluate resistance to pressure, temperature, and chemical exposure. Additionally, dimensional inspections and leak tests are performed to ensure the reliability and safety of the finished joints.
The meticulous execution of these manufacturing processes, from material selection to quality control, is essential in producing rubber hose joints that meet the demanding requirements of diverse industrial and commercial applications. By adhering to stringent production standards and leveraging advanced fabrication techniques, manufacturers can ensure the consistent delivery of high-performance and reliable rubber hose joints.
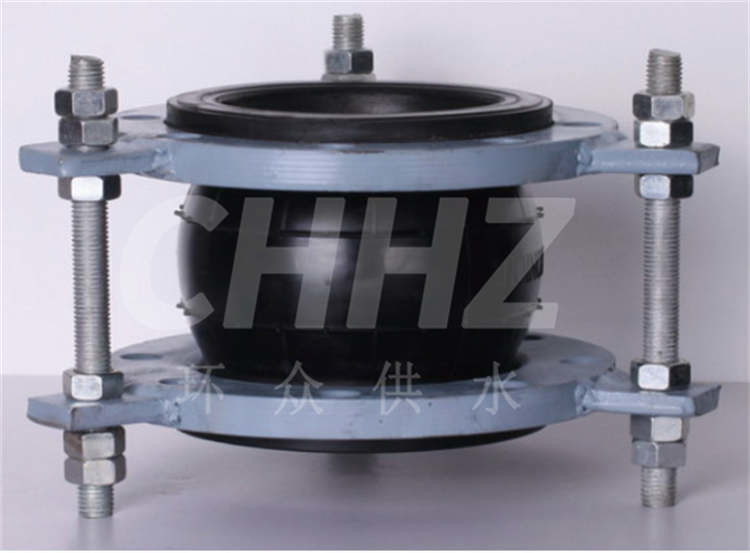