How to Joint a Two-Core Rubber Cable
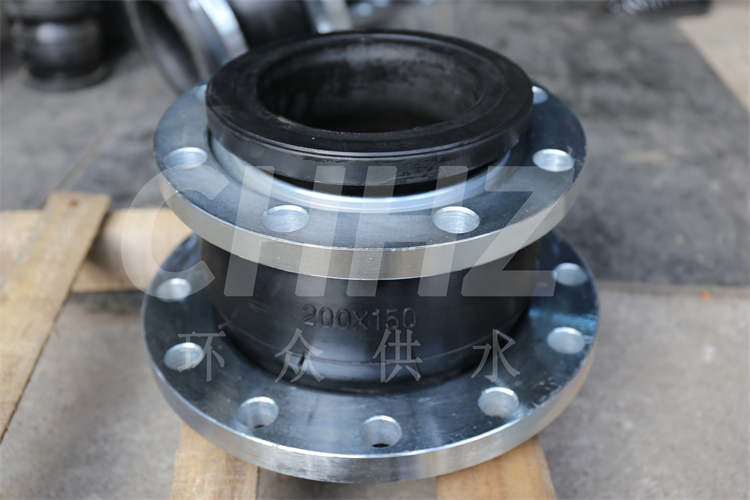
In electrical engineering and construction, the proper jointing of cables is crucial for maintaining electrical continuity and ensuring the safe and efficient transmission of power. When it comes to two-core rubber cables, the jointing process plays a vital role in establishing secure and reliable electrical connections. This article provides a comprehensive guide to jointing a two-core rubber cable, outlining the key steps and considerations for achieving a sound and durable cable joint.
Preparation and Inspection: Before commencing the jointing process, it is essential to prepare the two-core rubber cable and conduct a thorough inspection to ensure its integrity. The cable ends should be carefully cleaned and stripped to expose the conductors, and the insulation should be inspected for any signs of damage or aging. It is imperative to verify that the cable cores are free from any contaminants or moisture, as these factors can compromise the quality of the joint.
Selection of Jointing Method: There are various methods for jointing two-core rubber cables, including cold shrink, heat shrink, and resin jointing techniques. The choice of method depends on factors such as the application environment, the desired level of insulation, and the specific requirements of the cable joint. Each jointing method offers distinct advantages and may be tailored to suit the unique needs of the project.
Cold Shrink Jointing Process: In the cold shrink jointing method, a pre-expanded silicone rubber sleeve is positioned over the cable joint, and once the joint is made, the sleeve is unwound, allowing it to shrink and form a tight seal around the cable joint. This method requires no heat source for installation, offering simplicity and ease of use. It provides excellent electrical insulation and sealing properties while eliminating the need for specialized equipment.
Heat Shrink Jointing Process: Heat shrink jointing involves the use of a heat shrink sleeve, typically made of cross-linked polyolefin, which is placed over the cable joint and then heated using a heat gun or torch. The application of heat causes the sleeve to shrink tightly around the joint, forming a secure and robust insulation and sealing layer. Heat shrink jointing is known for its high mechanical strength, resistance to environmental factors, and compatibility with different cable types and sizes.
Resin Jointing Process: Resin jointing entails the use of a specially formulated resin compound that is applied to the cable joint to encapsulate and insulate the conductors. The resin is poured into a mold or encapsulation chamber, where it cures to form a solid and protective barrier around the joint. Resin jointing offers excellent resistance to moisture, chemicals, and mechanical stress, making it suitable for harsh and demanding environments.
Conclusion: The jointing of a two-core rubber cable requires careful preparation, adherence to best practices, and the selection of an appropriate jointing method. Whether employing cold shrink, heat shrink, or resin jointing techniques, engineers and electricians must prioritize the quality and reliability of the joint to ensure the long-term performance and safety of electrical installations. By following the recommended procedures and utilizing quality materials, a well-executed cable joint will contribute to the seamless transmission of power and the integrity of electrical systems.
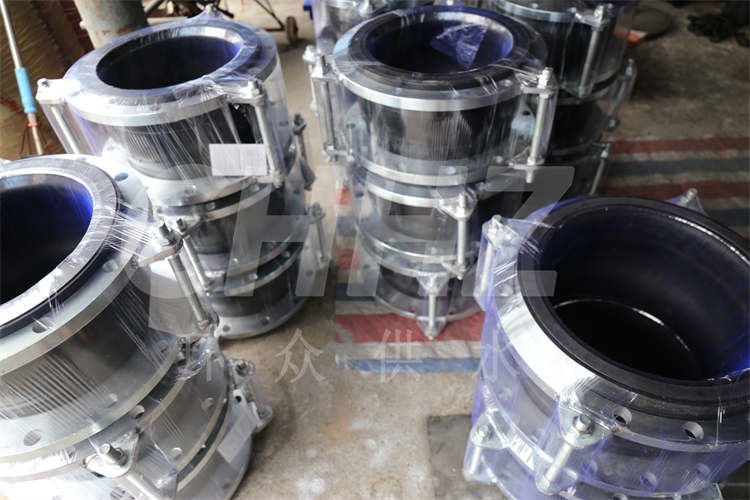