Creating Automotive Air Conditioning Rubber Hose Connections
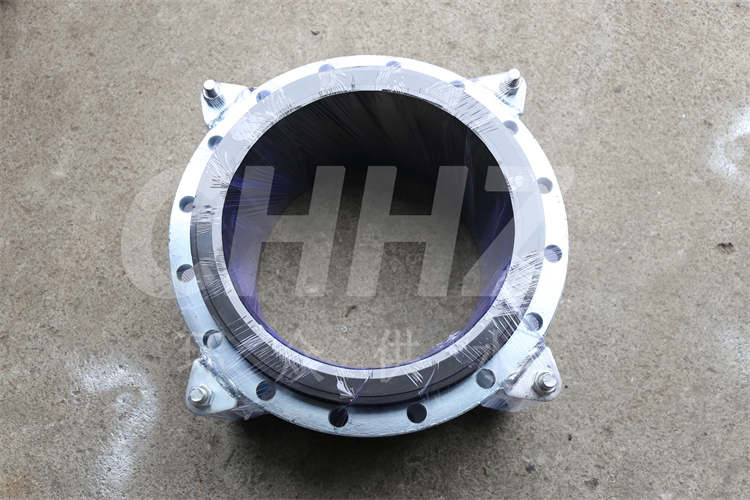
Introduction: The production of rubber hose connections for automotive air conditioning systems involves a series of precise manufacturing processes to ensure the reliability and efficiency of the final product. This article provides an overview of the key steps and equipment involved in the fabrication of rubber hose connections used in automobile air conditioning systems.
Rubber Compound Mixing: The manufacturing process begins with the precise blending of rubber compounds alongside additives and reinforcement materials in mixing equipment. This step is crucial for achieving the desired physical and chemical properties, such as flexibility, durability, and resistance to heat and chemical agents. The mixed compounds are then processed to form the base material for the rubber hoses.
Extrusion: The mixed rubber compounds are then fed into extruders to create continuous lengths of rubber tubes. Extrusion equipment shapes the rubber material into the required cross-sectional profile, maintaining consistent dimensions and physical properties throughout the length of the hose. This process ensures uniformity and accuracy in the production of rubber hoses for air conditioning systems.
Cord Fabrication: In some cases, reinforcement cords or layers are incorporated into the rubber hoses to enhance strength and pressure resistance. Cord fabrication equipment is employed to manufacture high-strength textile or metal cords, which are then integrated into the hose construction during the assembly process.
Braiding or Spiral Winding: For added reinforcement, the rubber hose may undergo a braiding or spiral winding process. Braiding machines or winders are used to apply textile or metal reinforcement layers around the rubber tube, further enhancing its structural integrity and resistance to internal pressure and external forces.
Hose Assembly: The assembled rubber hose is then fitted with the necessary end fittings or connectors, which are securely attached using specialized crimping or swaging equipment. This step ensures leak-free connections and structural integrity between the hose and the accompanying components of the air conditioning system.
Pressure and Leak Testing: Quality validation is critical in the production of automotive air conditioning rubber hose connections. Pressure testing equipment is used to subject the assembled hoses to specified pressures, confirming their ability to withstand operating conditions without any compromise in integrity. Leak testing further ensures the absence of any microscopic imperfections that could lead to refrigerant leaks.
Surface Finishing and Packaging: Upon successful validation, the rubber hose connections undergo surface finishing processes to remove any imperfections and ensure a smooth, clean appearance. The finished hoses are then carefully packaged to protect them from contaminants and mechanical damage, ready for distribution and installation in automotive air conditioning systems.
In conclusion, the fabrication of rubber hose connections for automotive air conditioning systems involves a sequence of specialized processes, including rubber compound mixing, extrusion, cord fabrication, braiding or winding, assembly, testing, surface finishing, and packaging. The integration of precision equipment and rigorous quality control measures ensures the production of high-performance rubber hose connections that meet the stringent requirements of modern automobile air conditioning applications.
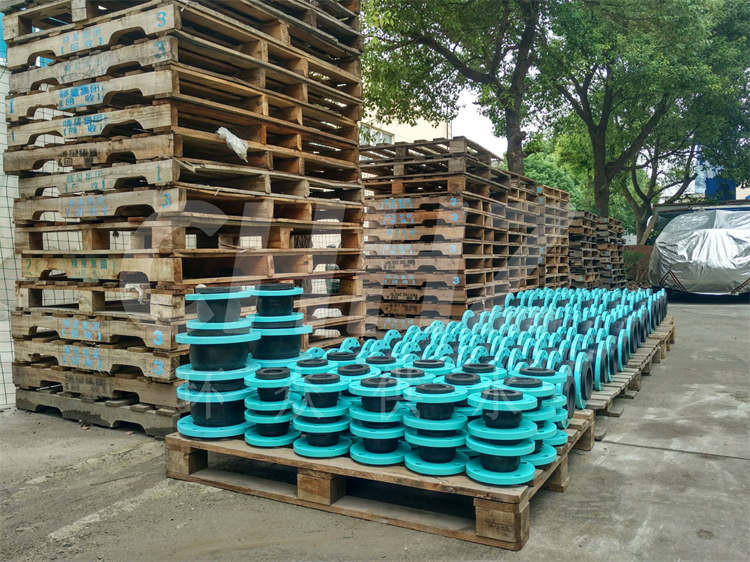