The Importance of Rubber Water Hose Joint Molds in Manufacturing: A Comprehensive Overview
Rubber water hose joint molds play a crucial role in the manufacturing process of rubber water hose joints, enabling the production of high-quality components for various fluid transfer applications. Understanding the significance of these molds is essential for optimizing the manufacturing process and ensuring the quality and performance of the final products.
Precision and Consistency: Rubber water hose joint molds are designed to provide the precise shape, dimensions, and features required for manufacturing standardized hose joints. The molds ensure consistency in the production process, resulting in uniform and reliable components that meet industry standards and customer specifications.
Material Compatibility: Molds for rubber water hose joints are engineered to accommodate the specific material properties of rubber, including elasticity, flexibility, and resilience. The design and construction of the molds account for the unique characteristics of rubber, ensuring that the manufacturing process does not compromise the integrity and functionality of the end products.
Customization and Versatility: Manufacturers of rubber water hose joint molds offer customization options to meet diverse industry needs and product requirements. Mold designs can be tailored to produce a wide range of hose joint variations, including different sizes, shapes, and end connections. This versatility allows manufacturers to cater to specific applications and design preferences.
Durability and Longevity: High-quality rubber water hose joint molds are engineered for durability and longevity, capable of withstanding the pressures, temperatures, and repetitive use associated with the manufacturing process. The use of robust materials and precision engineering ensures that the molds maintain their integrity over extended production cycles, minimizing downtime and maintenance requirements.
Efficiency and Productivity: The use of well-designed molds enhances the efficiency and productivity of the manufacturing process, reducing cycle times and maximizing output. By streamlining the molding process and optimizing tooling designs, manufacturers can achieve higher production volumes without compromising on quality, ultimately driving cost-effectiveness and competitiveness in the market.
Quality Assurance and Regulatory Compliance: Mold designs are developed to meet industry standards and regulatory requirements, ensuring that the manufactured rubber water hose joints adhere to quality, safety, and performance benchmarks. The molds play a critical role in maintaining product consistency, precision, and compliance with relevant standards, bolstering the reputation of manufacturers and the reliability of their products.
In summary, rubber water hose joint molds are integral to the production of high-quality components for fluid transfer applications. They embody precision, material compatibility, customization, durability, efficiency, and quality assurance, ultimately contributing to the overall success of manufacturers in delivering reliable and resilient rubber water hose joints to a diverse range of industries.
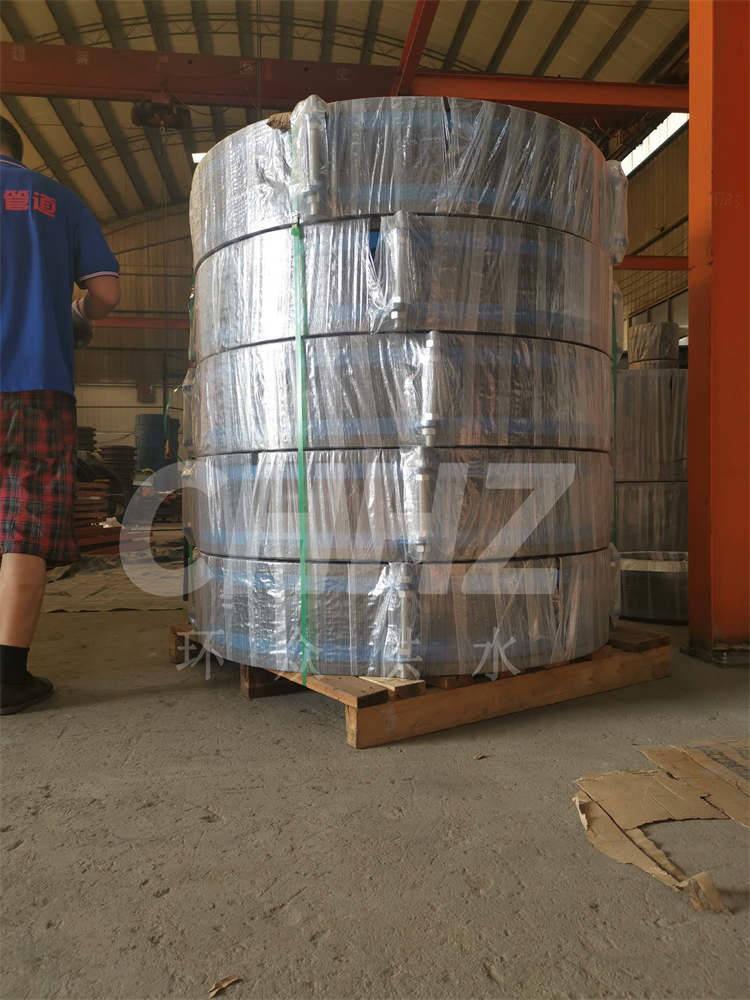