A Fully Electric Injection Molding Machine with Rubber Elastic Joints
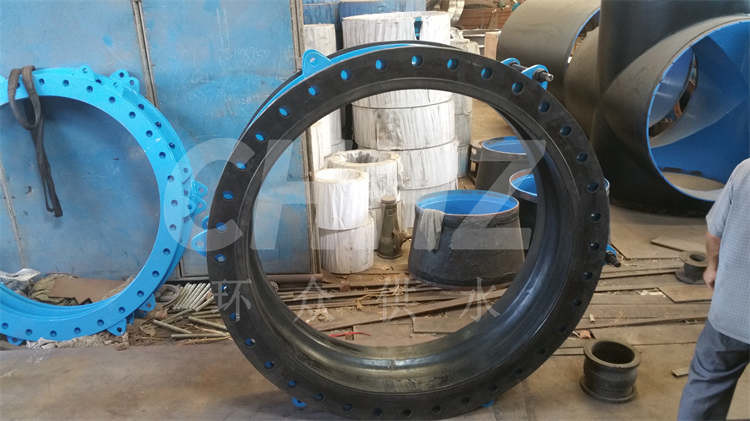
Introduction: A fully electric injection molding machine represents the cutting-edge technology in the plastic molding industry. As manufacturing processes continue to evolve, the demand for enhanced precision, energy efficiency, and operational flexibility has driven the development of fully electric injection molding machines. In this article, we explore the integration of rubber elastic joints in a fully electric injection molding machine and the benefits they offer.
Utilization of Rubber Elastic Joints: The incorporation of rubber elastic joints in a fully electric injection molding machine serves multiple purposes. These joints act as flexible connectors within the machine's structure, allowing for vibration absorption, sound dampening, and mitigating the impact of dynamic forces during operation. Moreover, the use of rubber elastic joints contributes to the overall structural integrity of the machine, reducing stress concentration and enhancing durability.
Vibration Absorption and Noise Reduction: During the operation of an injection molding machine, various mechanical components are prone to generating vibrations and acoustic emissions. By utilizing rubber elastic joints strategically placed within the machine's framework, vibrations are effectively absorbed, and noise levels are significantly reduced. This is especially crucial in maintaining a favorable working environment and meeting stringent noise level regulations.
Improved Dynamic Performance: Rubber elastic joints contribute to improving the dynamic performance of fully electric injection molding machines. They enable a degree of flexibility within the machine's structure, allowing it to better adapt to dynamic loads, rapid accelerations, and decelerations. By mitigating the stress and impact on critical components, the rubber elastic joints help optimize the overall performance and longevity of the machine.
Enhanced Precision and Stability: In precision-oriented processes such as injection molding, maintaining the stability of the machine is paramount. Rubber elastic joints play a key role in providing the necessary damping effect to minimize the oscillation and resonance, thereby enhancing the stability of the machine. This, in turn, facilitates precise control over the injection and molding processes, resulting in superior product quality and consistency.
Energy Efficiency: The utilization of rubber elastic joints contributes to the energy efficiency of fully electric injection molding machines. By mitigating the effects of vibration and dynamic forces, the machine's power consumption is optimized. Furthermore, the enhanced stability and reduced mechanical stress contribute to lower maintenance requirements, ultimately resulting in improved operational efficiency and reduced downtime.
Conclusion: In conclusion, the integration of rubber elastic joints in a fully electric injection molding machine offers multifaceted benefits, encompassing vibration absorption, noise reduction, improved dynamic performance, enhanced precision, stability, and energy efficiency. As the industry continues to prioritize operational excellence and sustainability, the utilization of rubber elastic joints stands as a testament to technological innovation and continual advancement in the field of plastic molding machinery.
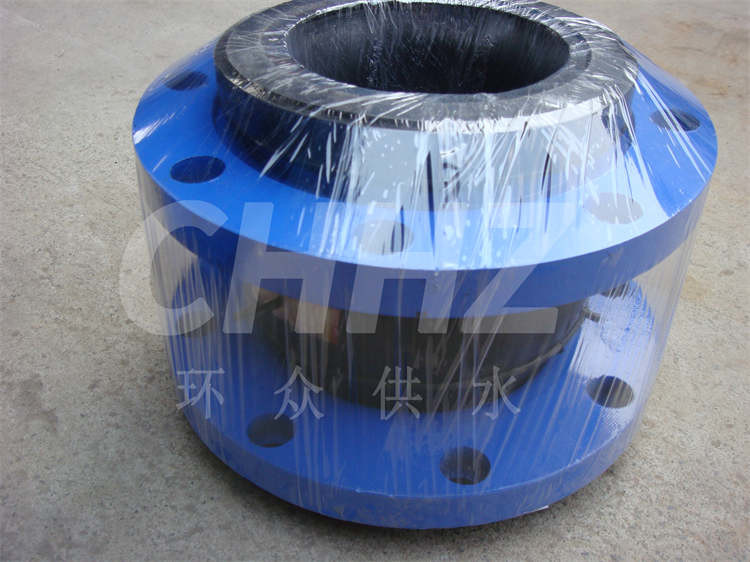