Cable Penetrations with Rubber Seals for Panel Joints
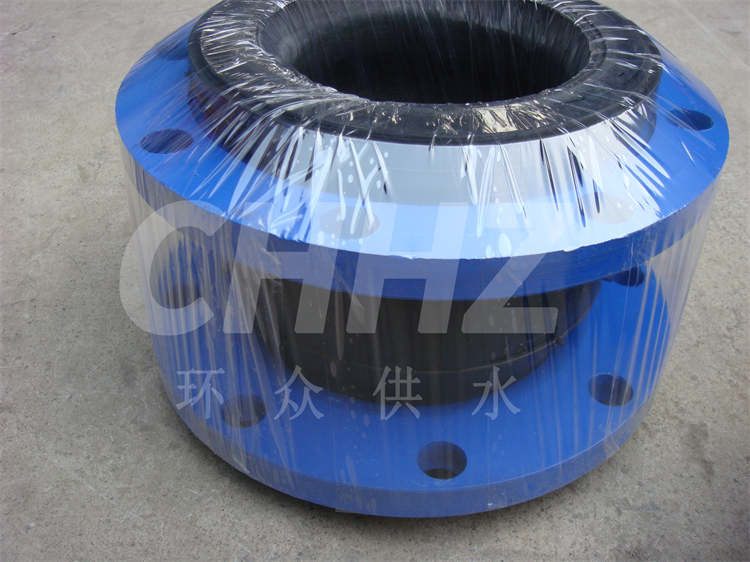
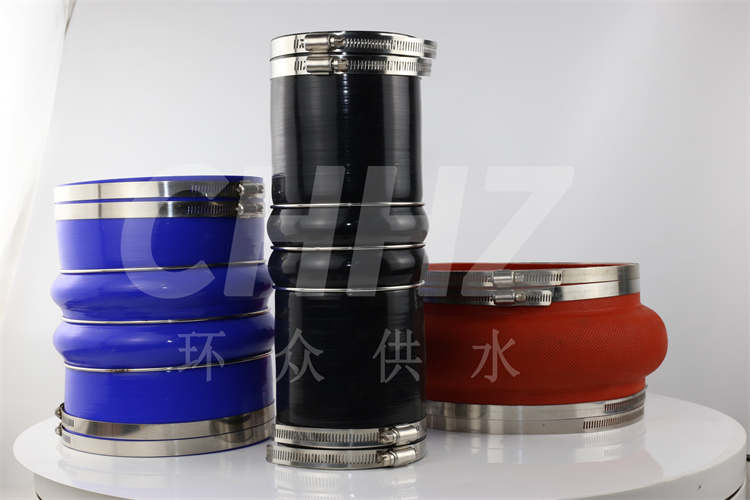
Cable penetrations are utilized in various industries to safely and effectively route cables through panel joints while maintaining the integrity of the enclosure. This article focuses on the importance of using rubber seals in cable penetrations for panel joints, emphasizing their function, design considerations, installation, and maintenance.
The use of rubber seals in cable penetrations for panel joints is essential to prevent the ingress of dust, water, and other contaminants, thus safeguarding electrical systems and equipment from potential damage. When designing and implementing cable penetrations with rubber seals, several key factors must be considered to ensure their optimal performance and reliability.
Seal Material and Compatibility: Selecting the appropriate rubber material for the seals is crucial to ensure their compatibility with the cable insulation, panel materials, and environmental conditions. The rubber seals should exhibit resistance to abrasion, temperature variations, and exposure to chemicals or UV radiation. Additionally, they should maintain their elasticity and sealing properties over an extended period.
Design and Construction: The design of cable penetrations with rubber seals must facilitate a secure and water-tight connection between the cable and the panel joint. This includes the use of high-quality rubber grommets, sleeves, or gaskets that are specifically designed for cable penetrations. The seals should be flexible enough to accommodate different cable diameters while maintaining a snug fit to prevent the passage of contaminants.
Installation and Sealing: Proper installation and sealing techniques are essential for the effective performance of rubber seals in cable penetrations. Prior to installation, the panel cutouts and cable openings should be clean and free from any debris or sharp edges that could compromise the integrity of the seals. The rubber seals should be installed with precision, ensuring a firm and uniform compression around the cables to create a reliable seal.
Inspection and Maintenance: Regular inspection and maintenance of cable penetrations with rubber seals are imperative to identify any signs of wear, degradation, or damage to the seals. Visual checks for cracks, shrinkage, or disintegration should be conducted, and any damaged seals should be promptly replaced to uphold the integrity of the cable penetrations and prevent potential ingress of contaminants.
In summary, utilizing rubber seals in cable penetrations for panel joints is a critical aspect of maintaining the protective properties of enclosures while accommodating the passage of cables. Selecting suitable seal materials, employing proper design and installation practices, and adhering to routine maintenance protocols are fundamental in ensuring the effectiveness and longevity of cable penetrations with rubber seals. By implementing these measures, industries can mitigate the risk of environmental ingress and uphold the safety and functionality of their electrical systems.
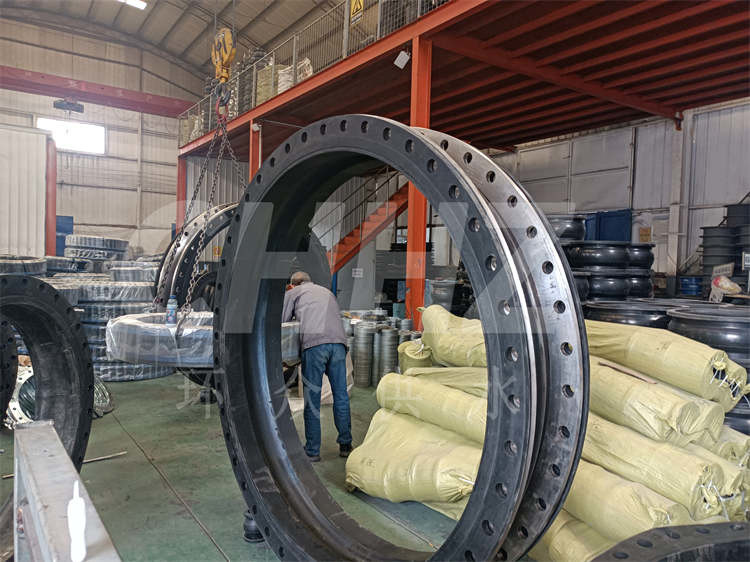