Food-Grade Rubber Flexible Joints for Flanges
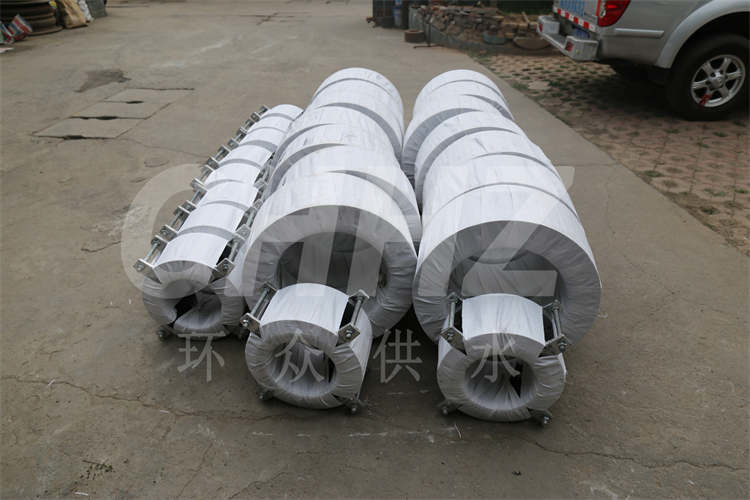
In various food processing and pharmaceutical industries, the use of food-grade rubber flexible joints for flanges is paramount. These joints play a crucial role in connecting and sealing pipelines while ensuring compliance with stringent hygiene and safety standards. In this article, we will delve into the characteristics, installation, and benefits of food-grade rubber flexible joints, highlighting their significance in maintaining sanitary and efficient fluid handling systems.
Characteristics of Food-Grade Rubber Flexible Joints: Food-grade rubber flexible joints are designed to withstand the demanding requirements of food and pharmaceutical applications. These joints are typically fabricated from high-quality, non-toxic elastomers such as EPDM (Ethylene Propylene Diene Monomer), silicone, or nitrile rubber, which are compliant with FDA (Food and Drug Administration) and/or 3A sanitary standards. Key characteristics of food-grade rubber flexible joints include:
Hygienic properties: The materials used in these flexible joints are resistant to microbial growth, can be easily sanitized, and do not impart odors or flavors to the conveyed products, ensuring the integrity of the food or pharmaceutical substances.
Flexibility and resilience: The rubber composition allows the joints to absorb vibrations, compensate for misalignments, and withstand thermal expansion, thereby protecting the overall piping system from stress and damage.
Chemical resistance: Food-grade rubber flexible joints exhibit excellent resistance to a wide range of chemicals, cleaning agents, and sterilization methods commonly used in food and pharmaceutical processing.
Installation of Food-Grade Rubber Flexible Joints: Proper installation of food-grade rubber flexible joints is critical to maintain a hygienic and secure fluid transfer system. The following steps outline the best practices for installing these joints:
a. Inspection: Thoroughly examine the flexible joints for any defects or contamination before installation. Ensure that the joints meet the required specifications and are free from any damage that may compromise their performance.
b. Alignment: Ensure that the flanges to be connected are properly aligned and the gasket seating surfaces are clean and smooth.
c. Gasket placement: Position the food-grade rubber flexible joint between the mating flanges, ensuring that it is centered and aligned with the bolt holes.
d. Bolting: Insert the bolts through the flange holes and hand-tighten them in a crisscross pattern to apply uniform pressure and compress the joint evenly.
e. Torqueing: Gradually torque the bolts in a sequential pattern, following the recommended torque values to achieve proper compression and create a leak-free seal.
Benefits of Food-Grade Rubber Flexible Joints: The utilization of food-grade rubber flexible joints offers several advantages in food and pharmaceutical processing environments, including:
Compliance with regulatory standards: These joints contribute to maintaining the hygienic conditions required by regulatory authorities, ensuring that food and pharmaceutical products remain untainted and safe for consumption.
Enhanced system longevity: By absorbing vibrations and accommodating thermal movement, the flexible joints reduce stress on the pipeline, flanges, and equipment, consequently prolonging the lifespan of the entire system.
Minimized maintenance: The resilient nature of the joints reduces the occurrence of leaks, flange damage, and associated maintenance requirements, leading to improved operational efficiency and cost savings.
In summary, the use of food-grade rubber flexible joints for flanges is crucial in ensuring the integrity and safety of fluid handling systems within food and pharmaceutical processing facilities. By understanding their characteristics, correct installation methods, and associated benefits, industry professionals can optimize the performance and compliance of their piping systems in line with industry standards and regulations.
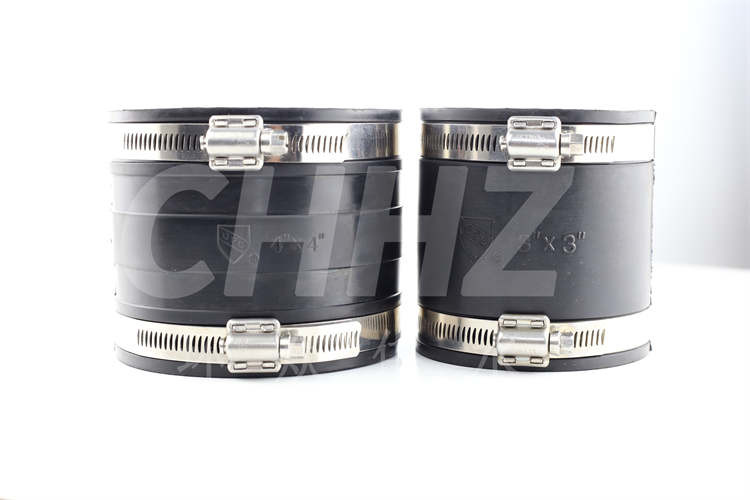