Rubber Expansion Joints for Chemical Pipeline Systems
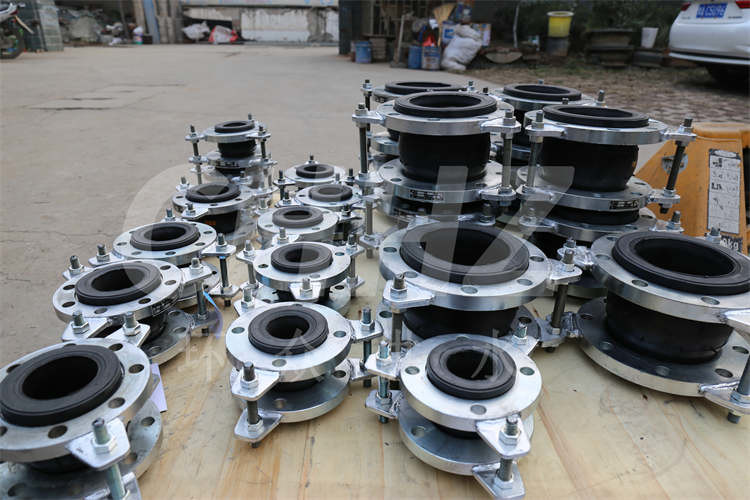
Rubber expansion joints are essential components in chemical pipeline systems, as they provide flexibility, vibration isolation, and compensation for movements caused by thermal expansion, mechanical vibration, and misalignment. This article aims to highlight the significance of rubber expansion joints in chemical pipeline applications, their benefits, and the recommended practices for their installation and maintenance.
Significance of Rubber Expansion Joints: In chemical pipeline systems, rubber expansion joints play a critical role in mitigating the detrimental effects of thermal expansion and contraction, as well as absorbing vibrations. These joints accommodate lateral, axial, and angular movements, thereby reducing stress on the pipeline and its associated equipment. By allowing movement in multiple directions, they help to prevent premature wear and damage to the piping system, ensuring its longevity and reliability.
Benefits of Rubber Expansion Joints: Rubber expansion joints offer several key benefits in chemical pipeline applications. Their inherent flexibility and resilience enable them to absorb movements and vibrations, thereby extending the service life of the piping system and associated equipment. Furthermore, they provide sound attenuation and damping of fluid-borne noise, contributing to a quieter and safer working environment. The ability of rubber expansion joints to isolate vibration and shock helps in safeguarding sensitive equipment and structures from potential damage, enhancing overall operational safety and efficiency.
Installation and Maintenance Practices: Proper installation and maintenance are crucial for ensuring the effective performance of rubber expansion joints in chemical pipeline systems. During installation, it is essential to adhere to manufacturer specifications and industry standards to ensure correct alignment and anchorage of the expansion joints. Regular inspection and monitoring of the expansion joints are necessary to detect signs of wear, fatigue, or damage, which may compromise their functionality. Routine maintenance tasks, including cleaning, lubrication, and visual inspection, should be carried out in accordance with recommended guidelines to prolong the service life and performance of the expansion joints.
In conclusion, rubber expansion joints are indispensable components in chemical pipeline systems, providing flexibility and vibration isolation while compensating for movements caused by various factors. Their ability to reduce stress on the piping system, absorb vibrations, and mitigate noise makes them essential for ensuring the reliability and safety of chemical fluid transfer applications. By following best practices for installation and maintenance, the effective performance and longevity of rubber expansion joints can be sustained, contributing to the overall integrity and efficiency of chemical pipeline systems.
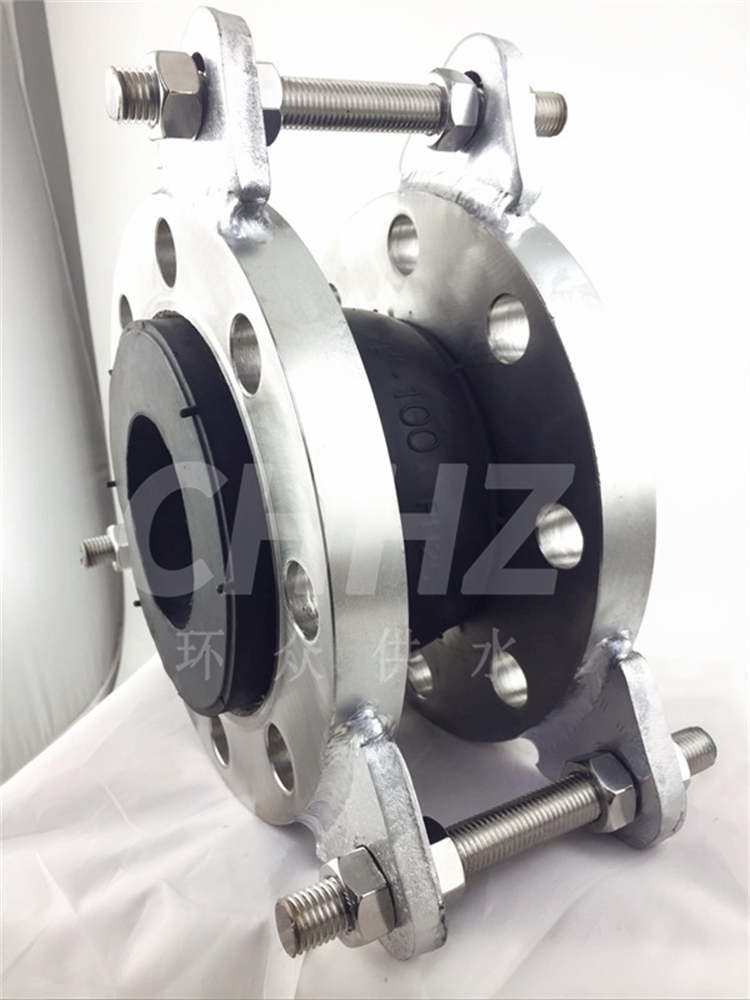