Installation Method for Food-Grade Rubber Hose Connectors
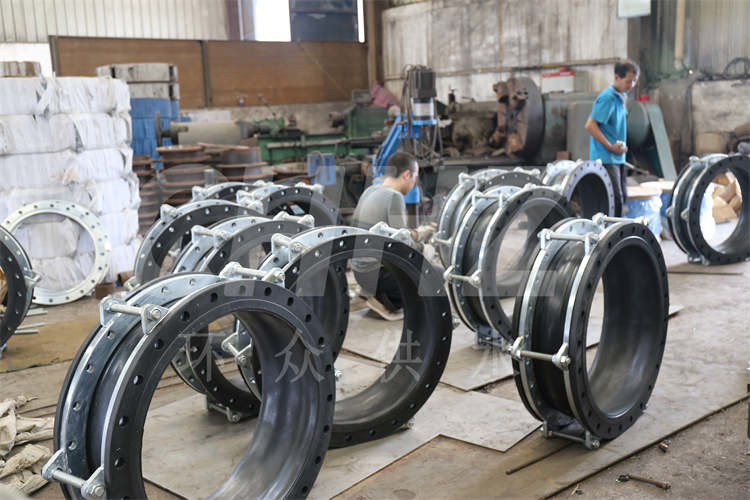
The installation of food-grade rubber hose connectors is a critical aspect of ensuring the integrity and safety of fluid handling systems in food processing, pharmaceutical, and other related industries. The following article outlines the essential steps and best practices for the proper construction and installation of food-grade rubber hose connectors, emphasizing adherence to industry standards and regulations to guarantee the hygienic and reliable operation of these systems.
Selection of Food-Grade Rubber Hose Connectors Prior to installation, it is crucial to select food-grade rubber hose connectors manufactured from materials approved for use in contact with food products. These materials typically include EPDM, silicone, and other compliant elastomers that are resistant to microbial growth, maintain their physical properties in the presence of food products, and are free from toxic substances that could contaminate consumables. Manufacturers' certifications and compliance with relevant standards, such as FDA and EU regulations, should be verified to ensure the suitability of the selected connectors for food processing applications.
Preparation of Glass Tubing Joints and Connectors The glass tubing joints that are to be connected with the rubber hose connectors should be thoroughly inspected and cleaned prior to installation. Any sharp edges, irregularities, or contaminants on the tubing should be removed to prevent damage to the connectors and ensure a secure fit. Similarly, the rubber hose connectors themselves should be inspected for any defects, and they must be cleaned to eliminate any traces of dust, debris, or manufacturing residues that could compromise the quality and hygiene of the installation.
Lubrication and Assembly To facilitate the assembly process and ensure a smooth fit, a food-grade lubricant should be applied to the glass tubing joints and the interior of the rubber hose connectors. Care should be taken to use lubricants that comply with the relevant food safety regulations to avoid introducing contaminants into the system. The connectors should then be carefully positioned and pushed onto the glass tubing joints, ensuring a secure and leak-free connection without damaging the tubing or the connectors.
Securing and Testing Once the rubber hose connectors are in place, they should be secured using appropriate clamps or fittings to prevent dislodgment during operation. The integrity of the connections should be checked by subjecting the system to a pressure test, ensuring that there are no leaks or disruptions in the fluid flow. Any signs of leakage or instability should be addressed promptly to avoid compromising the safety and hygiene of the installation.
Periodic Inspection and Maintenance After installation, regular inspections and maintenance of the rubber hose connectors and the associated tubing joints should be conducted to identify and address any wear, degradation, or damage that could affect the performance or integrity of the system. This includes replacing worn connectors, re-tightening clamps, and addressing any environmental factors that could impact the functionality of the installation.
In conclusion, the proper construction and installation of food-grade rubber hose connectors is essential for ensuring the safety and hygiene of fluid handling systems in food processing and pharmaceutical environments. Adherence to industry standards, careful material selection, thorough preparation, precise assembly, and regular maintenance are all critical factors in achieving a reliable and compliant installation that meets the stringent requirements of the food and pharmaceutical industries.
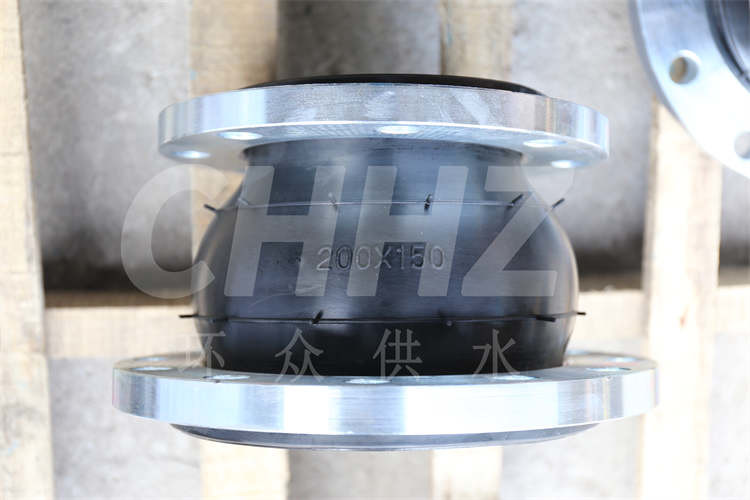