Rubber Expansion Joint Manufacturing Process
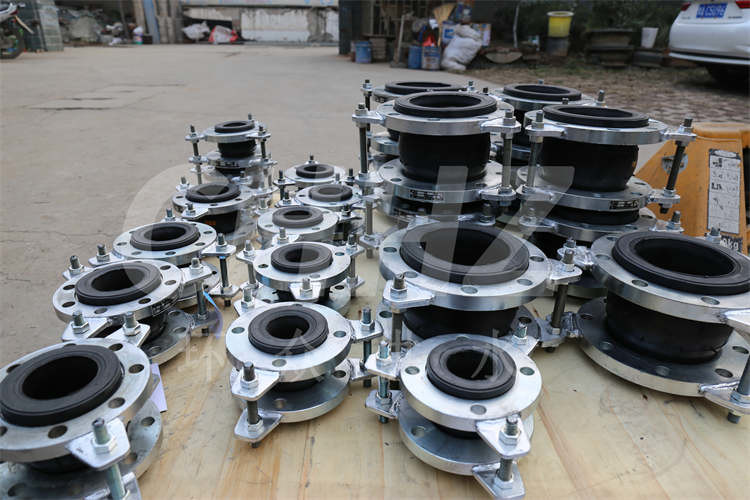
Rubber expansion joints are crucial components in various industrial applications, offering flexibility and vibration absorption in piping systems. The manufacturing process of rubber expansion joints involves several key steps to ensure the production of high-quality, durable, and reliable products. This article provides an overview of the essential stages in the manufacturing process of rubber expansion joints.
1. Material Selection and Preparation:The manufacturing process begins with the careful selection of high-quality rubber materials that exhibit excellent flexibility, resilience, and chemical resistance. Natural rubber, synthetic rubber compounds, and reinforcing materials such as fabric or metal components are commonly used. These materials are then meticulously inspected and prepared, ensuring that they meet the required specifications and standards for durability and performance.
2. Molding and Forming:The prepared rubber materials are then placed into molds, where they undergo molding and shaping processes. Compression molding or injection molding techniques are commonly employed to achieve the desired shape and dimensions of the expansion joints. During this stage, the material is subjected to heat and pressure to facilitate curing and bonding, resulting in the formation of the characteristic bellows or corrugations that enable flexibility and movement in the expansion joints.
3. Reinforcement Assembly:Incorporating reinforcing elements into the rubber expansion joints is essential to enhance their structural integrity and durability. Depending on the design and application requirements, layers of fabric, wire mesh, or metal rings may be integrated to provide additional strength and resistance to pressure, vibration, and media flowing through the piping system. The reinforcement assembly is carefully integrated during the manufacturing process to ensure optimal performance under various operating conditions.
4. Vulcanization and Curing:Vulcanization and curing are critical stages in the manufacturing process, during which the rubber material undergoes chemical and thermal treatments to attain the desired physical and mechanical properties. Vulcanization, typically carried out using heat and sulfur-based compounds, enhances the elasticity, resilience, and heat resistance of the rubber, while curing ensures the complete cross-linking of polymer chains, resulting in a stable and durable material structure.
5. Surface Treatment and Quality Assurance:Upon completion of the manufacturing process, the rubber expansion joints undergo surface treatment and finishing to address any imperfections and ensure a smooth, uniform, and clean exterior. Quality assurance protocols, including visual inspection, dimensional checks, and performance testing, are integral to verify the compliance of the finished products with stringent quality standards and specifications.
In conclusion, the manufacturing process of rubber expansion joints encompasses meticulous material selection, molding, reinforcement assembly, vulcanization, and quality assurance measures to produce reliable and high-performance components. By adhering to stringent manufacturing standards and quality control procedures, manufacturers can deliver rubber expansion joints that meet the demanding requirements of industrial piping systems, ensuring optimal flexibility, durability, and long-term functionality.
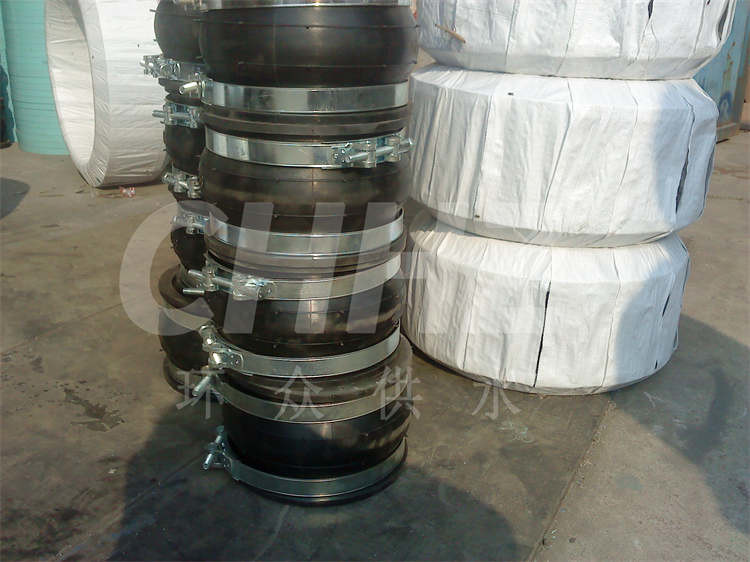