Rubber Joint Bonding

Rubber joints play a crucial role in various piping systems, providing flexibility and absorbing vibrations while maintaining the integrity of the interconnected pipelines. One important aspect of ensuring the effectiveness of rubber joints is proper bonding. The bonding process involves adhering the rubber joint to the adjacent surfaces, ensuring a secure and enduring connection. This article explores the significance of rubber joint bonding, the methods involved, and the key considerations for achieving a reliable bond.
Significance of Bonding:Effective bonding of rubber joints to the adjoining surfaces is essential for the overall performance and longevity of the piping system. Proper bonding enhances the joint's ability to withstand internal pressure, movement, and environmental factors, thereby preventing leaks, reducing the risk of joint dislodgment, and maintaining the system's structural integrity.
Methods of Bonding:1. Adhesive Bonding: This method involves the use of specialized adhesives or bonding agents that are compatible with rubber materials and the substrate to which the joint is being bonded. Adhesive bonding provides a strong, durable bond when applied correctly, promoting optimal joint performance.2. Vulcanization: In certain applications, rubber joints are vulcanized to the adjacent surfaces using heat and pressure, producing a chemical bond between the rubber and the substrate. Vulcanization offers enhanced bonding strength and chemical resistance, making it suitable for high-stress or corrosive environments.3. Mechanical Fastening: In addition to adhesive bonding or vulcanization, mechanical fastening methods such as clamping or bolting may be employed to secure rubber joints to the adjoining components, providing additional reinforcement and stability.
Key Considerations for Reliable Bonding:1. Surface Preparation: Proper surface preparation is critical for successful bonding. The surfaces to be bonded must be clean, dry, and free from contaminants or residues that could compromise the adhesion of the rubber joint.2. Compatibility of Materials: Selecting adhesives or bonding methods that are compatible with the specific rubber material and the substrate is essential to ensure optimal bonding strength and long-term durability.3. Application Technique: Following the recommended application techniques, including proper adhesive application, pressure, and curing conditions, is vital for achieving a strong and uniform bond between the rubber joint and the adjoining surfaces.4. Environmental Considerations: Considering the environmental factors to which the bonded joint will be exposed, such as temperature variations, chemical exposure, and UV radiation, is crucial when selecting bonding methods and materials to ensure resilience against degradation.
In summary, the bonding of rubber joints is a critical aspect of ensuring the functionality, reliability, and service life of piping systems. By employing suitable bonding methods and adhering to best practices, engineers and operators can achieve robust and enduring connections, ultimately contributing to the efficient and safe operation of industrial pipelines.
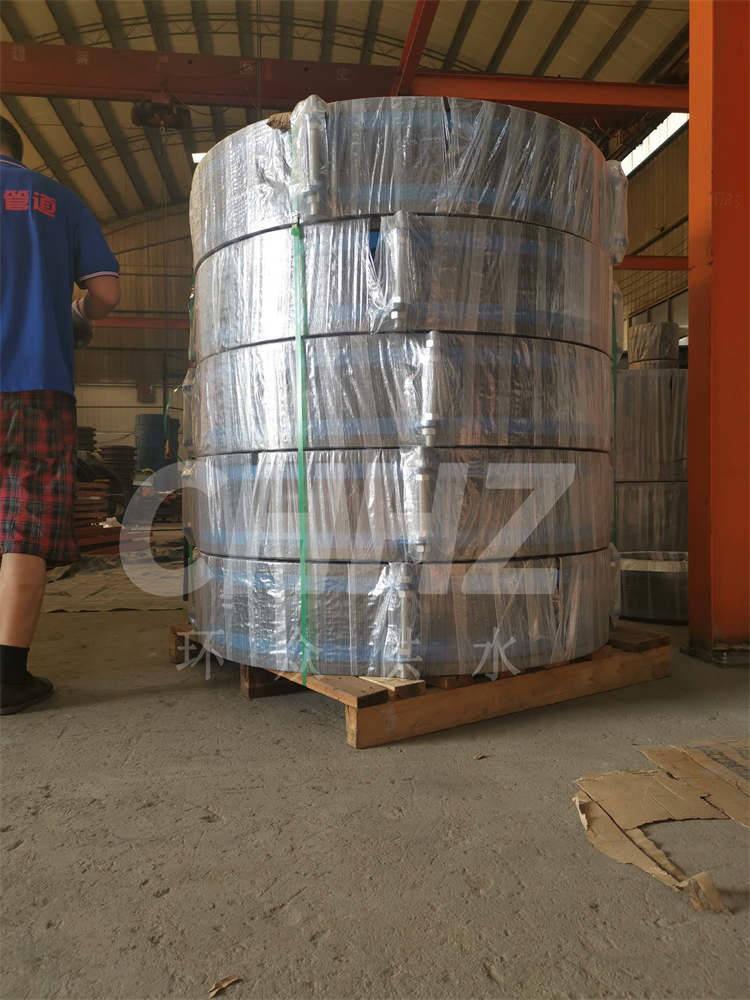