Rubber Joint Accident: Ensuring Safety in Industrial Settings
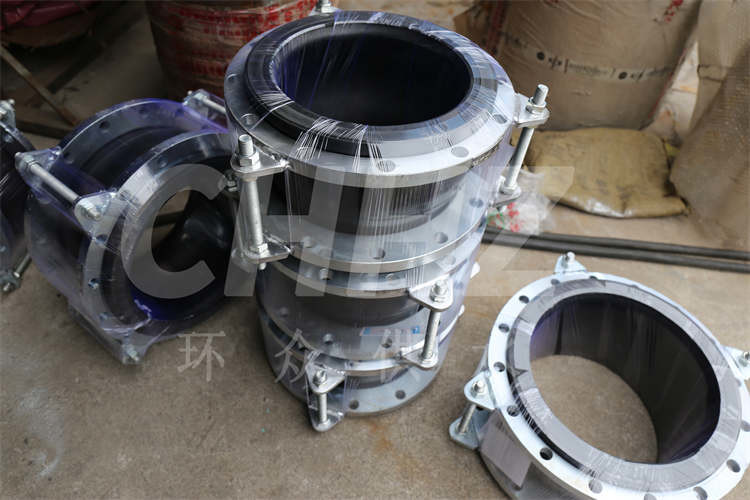
Rubber joints are essential components in industrial piping systems, providing flexibility and vibration absorption. However, in the event of an accident involving rubber joints, it is crucial to analyze the potential causes, assess the impact, and outline preventive measures to ensure safety in industrial settings.
Potential Causes of Rubber Joint Accidents:1. Material Degradation: Over time, rubber joints may experience material degradation due to exposure to harsh chemicals, extreme temperatures, or prolonged operational stress, leading to a loss of integrity and eventual failure.2. Improper Installation: Incorrect installation, such as inadequate anchoring or misalignment of piping, can create excessive stress on rubber joints, compromising their performance and increasing the risk of failure.3. Overpressure Situations: Sudden overpressure within the piping system, caused by factors such as hydraulic surges or equipment malfunctions, can exceed the designed limits of the rubber joints, resulting in ruptures or leaks.
Impact of Rubber Joint Accidents:1. Safety Risks: Accidents involving rubber joints can pose significant safety risks to personnel, as the release of hazardous substances, along with potential fires or explosions, may result in injuries and damage to the surrounding environment.2. Operational Disruption: The failure of rubber joints can lead to unplanned downtime, causing interruption to industrial processes, loss of production, and potential financial implications.
Preventive Measures and Safety Protocols:1. Regular Inspection and Maintenance: Implementing a comprehensive inspection and maintenance program for rubber joints is essential to identify signs of wear, degradation, or damage, allowing for timely replacements and repairs.2. Correct Material Selection: Ensuring that rubber joints are made from appropriate materials with resistance to chemicals, heat, and pressure, in alignment with the specific requirements of the industrial environment, can minimize the risk of failure.3. Proper Installation and Alignment: Adhering to industry best practices and standards for the installation and alignment of rubber joints, including correct anchoring, alignment, and support, is essential for enhancing their reliability and longevity.4. Pressure Monitoring and Control: Implementing effective pressure monitoring systems and measures to control and mitigate pressure surges within the piping system can help prevent overpressure situations that may compromise the integrity of rubber joints.5. Emergency Response Preparedness: Developing and implementing emergency response protocols, including evacuation procedures, containment measures, and firefighting systems, is crucial to mitigate the impact of potential accidents involving rubber joints.
In conclusion, addressing the potential causes, impact, and preventive measures related to accidents involving rubber joints is paramount to ensuring safety and operational reliability in industrial settings. By proactively implementing mitigation strategies and safety protocols, industrial facilities can minimize the risk of accidents and prioritize the well-being of personnel while sustaining efficient operations.
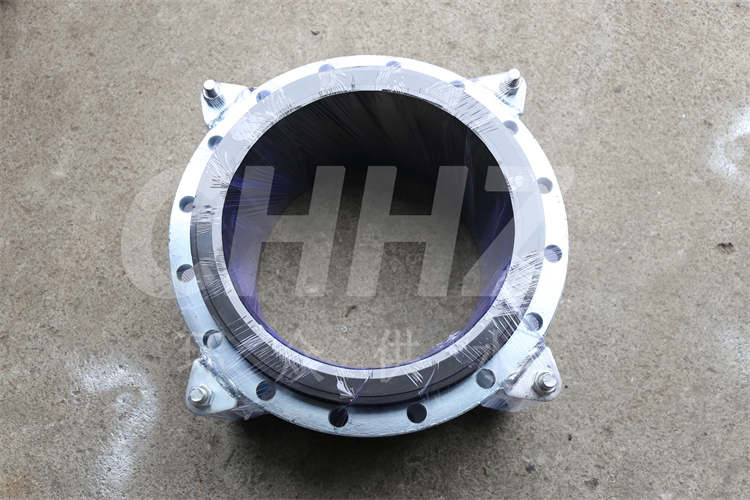