Rubber Joint Wear Resistance: Importance and Key Factors
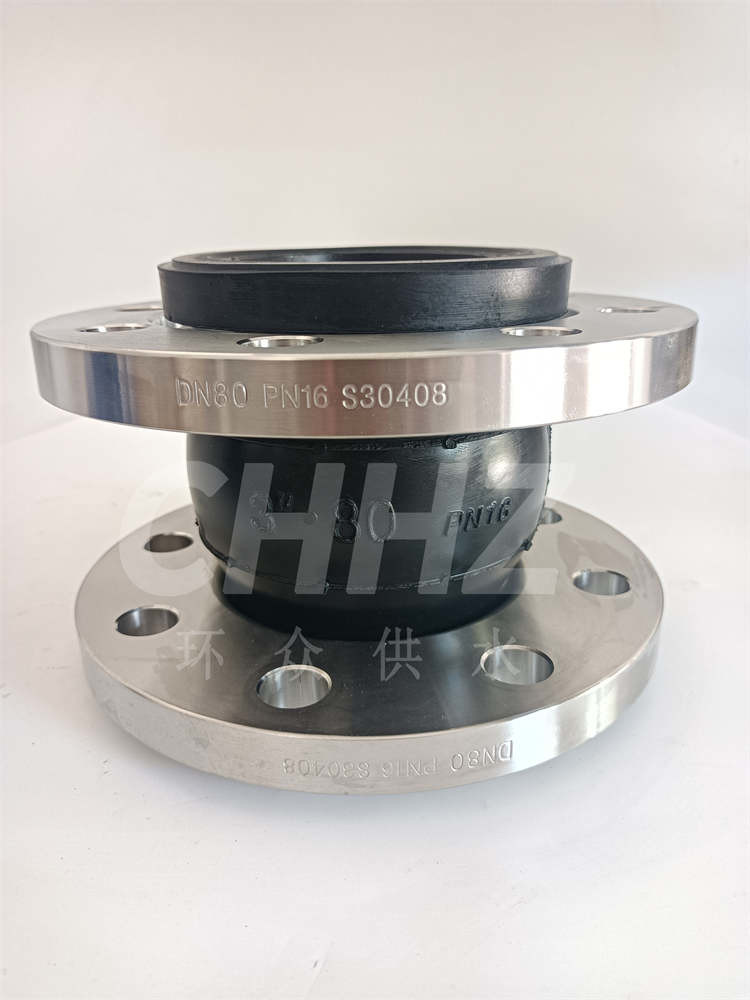
Rubber joints are essential components in piping systems, providing flexibility and absorbing movement and vibration. As such, the wear resistance of rubber joints is a critical factor in ensuring the durability and reliability of the overall system. This article aims to explore the importance of wear resistance in rubber joints and highlight key factors that contribute to their longevity and performance.
The wear resistance of rubber joints is significant as it directly impacts their ability to withstand friction, abrasion, and deterioration over time. In piping systems, rubber joints are subjected to various forms of wear, including mechanical abrasion from fluid flow, environmental factors such as exposure to chemicals or UV radiation, and operational stresses. As a result, the wear resistance of rubber joints is essential to maintaining their functional integrity and preventing premature failure.
Several key factors contribute to the wear resistance of rubber joints. The quality of the rubber material itself is a fundamental consideration. High-quality elastomers with superior wear-resistant properties, such as resistance to abrasion and tearing, are essential for ensuring the longevity of rubber joints. Additionally, the specific formulation and compound of the rubber material play a crucial role in determining its resistance to wear and deterioration.
Furthermore, the design and construction of rubber joints also influence their wear resistance. Factors such as the reinforcement of the rubber material, the thickness of the joint walls, and the presence of protective layers or coatings can enhance wear resistance and extend the service life of the joints. Innovative design features, such as incorporating anti-abrasive additives or specialized surface treatments, can further enhance the wear resistance of rubber joints.
The operating conditions and environmental factors to which rubber joints are exposed also significantly impact their wear resistance. Piping systems operating in harsh environments or conveying abrasive fluids require rubber joints that are specifically engineered to withstand these conditions. Resistance to chemical exposure, temperature variations, and environmental elements such as ozone and UV radiation are crucial for maintaining the wear resistance of rubber joints.
Proper installation and maintenance practices are essential for preserving the wear resistance of rubber joints. Adequate installation techniques and ensuring secure anchoring of the joints help prevent unnecessary wear and displacement. Additionally, regular inspection and maintenance of rubber joints, including monitoring wear patterns and addressing any signs of deterioration or damage, are crucial for prolonging their wear resistance and overall longevity.
In conclusion, the wear resistance of rubber joints is paramount for ensuring the durability and reliability of piping systems. By considering factors such as high-quality rubber material, robust design features, resistance to environmental factors, and proper installation and maintenance practices, the wear resistance of rubber joints can be effectively enhanced. Ultimately, prioritizing wear resistance contributes to the longevity and performance of rubber joints, thereby sustaining the integrity of piping systems.
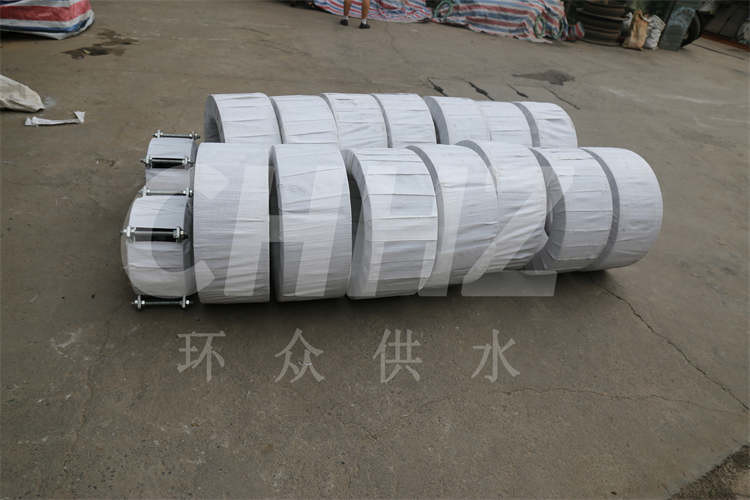