Rubber Joint Inspection: A Guide for Proper Packaging
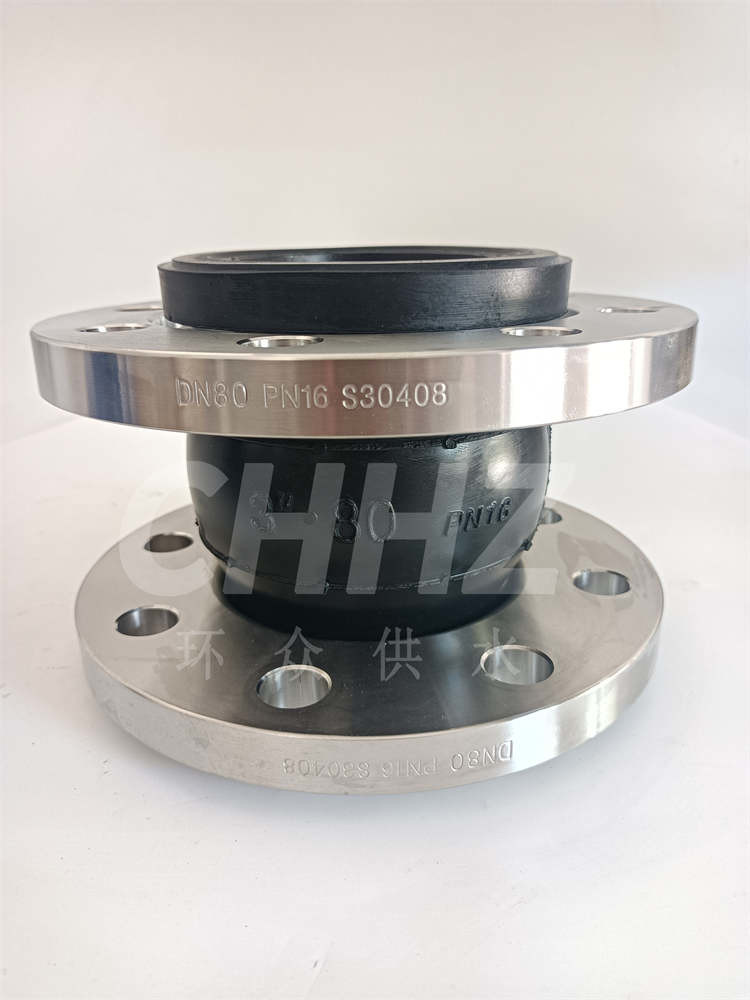
Proper packaging is essential to protect rubber joints during transportation and storage. Rubber joints are susceptible to damage from mishandling, environmental conditions, and improper storage, which can compromise their performance and longevity. This article provides guidance on the correct packaging of rubber joints to ensure their integrity and functionality.
When preparing rubber joints for packaging, it is vital to inspect them for any signs of damage, wear, or deformation. Cracks, tears, or abrasions on the rubber material, as well as dislodged hardware or corrosion on the metal components, should be addressed before packaging. Any compromised joints should be repaired or replaced to prevent further deterioration during transit and storage.
Selecting appropriate packaging materials is crucial to safeguard the rubber joints. Sturdy and durable cardboard cartons are commonly used to encase the joints, providing protection against impacts and external forces. The cartons should be of adequate size to accommodate the joints without allowing excessive movement, and they should be sealed securely to prevent exposure to environmental elements.
Prior to placing the rubber joints in the cartons, a cushioning material such as foam inserts or bubble wrap should be used to provide an additional layer of protection. This cushioning material helps to absorb shocks and vibrations during handling and transportation, reducing the risk of damage to the joints.
Furthermore, the cartons should be clearly labeled with information about the contents, including the type and size of the rubber joints, as well as any handling instructions or necessary safety precautions. Proper labeling assists in identifying the contents and facilitates safe and efficient handling and storage practices.
When stacking or storing packaged rubber joints, it is important to ensure that they are kept in a dry, clean, and well-ventilated environment. Exposure to moisture, extreme temperatures, or direct sunlight should be avoided, as these environmental factors can degrade the rubber material and compromise the joints' integrity.
In addition to packaging for transportation and storage, it is equally important to consider the handling and unpacking of rubber joints upon receipt. Clear instructions for unpacking and handling should be provided to minimize the risk of damage during the unpacking process and when transferring the joints to their intended storage location.
By following these recommended packaging practices, the integrity and functionality of rubber joints can be preserved throughout the transportation and storage process. Proper packaging not only safeguards the joints from potential damage but also ensures that they are delivered in optimal condition, ready for installation and use. Implementing these best practices for packaging rubber joints supports the overall reliability and performance of fluid handling systems, contributing to safe and efficient operations.
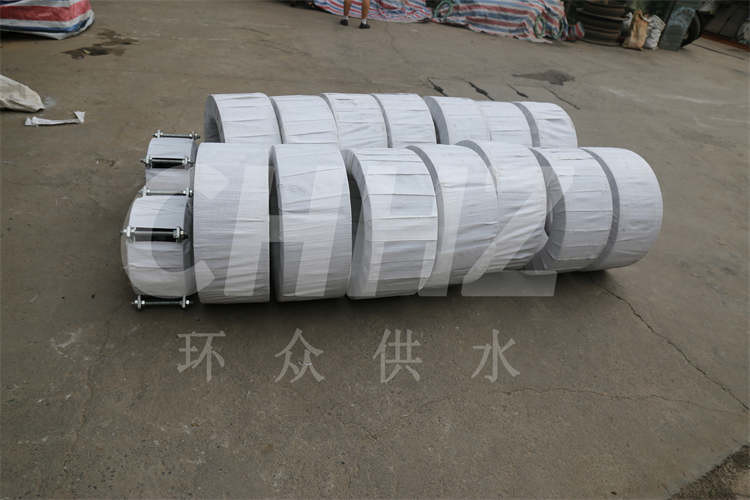