Installing rubber joints
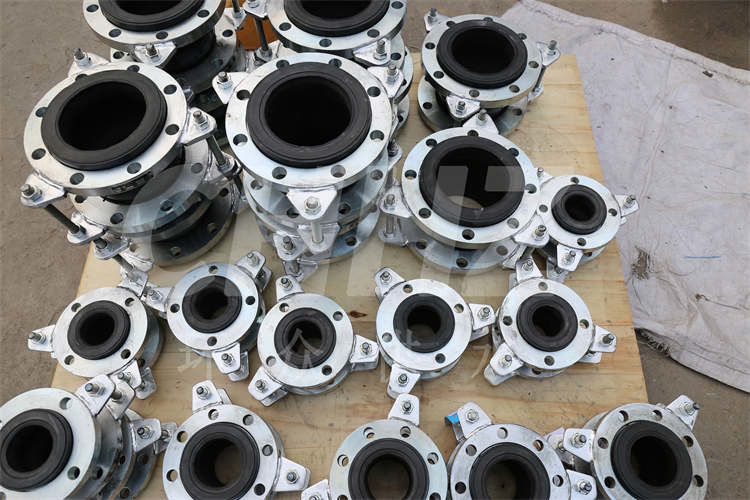
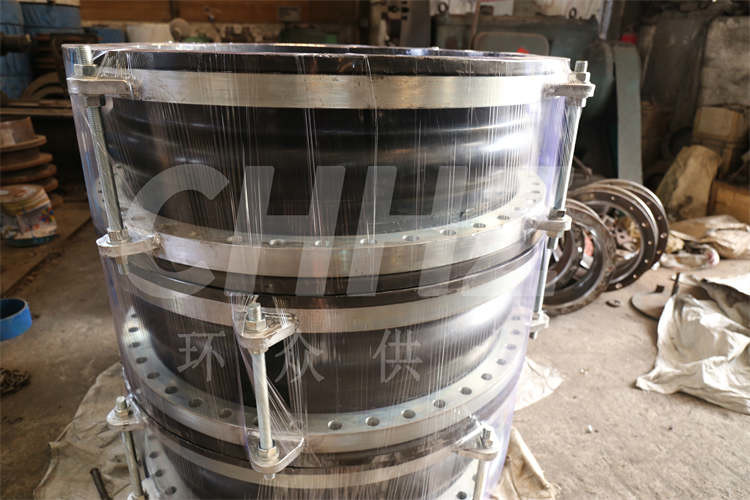
Installing rubber joints is a critical process in various industrial and mechanical systems, ensuring proper functionality, safety, and longevity of the equipment. Proper installation techniques are essential to maintain the integrity and performance of rubber joints in applications such as pipelines, ductwork, and machinery. This article outlines the key steps involved in the installation of rubber joints to ensure effective operation and reduced maintenance requirements in industrial settings.
1. Inspection and Preparation:Before installing rubber joints, it is crucial to inspect the components to ensure they are free from any defects or damage. This includes checking for any signs of wear, tears, or deterioration in the rubber material. Additionally, the mating flanges or connection points where the rubber joints will be installed should be thoroughly cleaned and prepared to ensure a secure and tight seal.
2. Correct Alignment and Positioning:Proper alignment of the rubber joints is vital to ensure optimal performance. Carefully align the joints with the mating flanges or connecting elements, ensuring that they are centered and correctly oriented. This alignment is crucial for preventing stresses or strains on the joints during operation, which could lead to premature failure.
3. Secure Attachment:Once the rubber joints are correctly aligned, secure attachment to the mating flanges or connection points should be carried out using appropriate fasteners, such as bolts and nuts. It is essential to tighten the fasteners evenly and gradually to avoid distortion or damage to the rubber joint. Following manufacturer recommendations for torque specifications is crucial to achieve the desired level of compression and seal integrity.
4. Consider Expansion and Misalignment:In installations where movement, vibration, or thermal expansion is expected, provisions should be made to accommodate these factors. Flexible rubber joints are designed to compensate for axial, lateral, and angular movements as well as absorb vibrations, making them suitable for various dynamic applications. Adequate clearance and support should be provided to allow for movement without inducing stress on the joints or adjacent components.
5. Pressure Testing:Once the rubber joints are installed, it is advisable to conduct a pressure test to ensure the integrity of the joints and the overall system. This test involves pressurizing the system to the designed operating pressure while inspecting for any leaks, bulges, or abnormal behavior of the rubber joints. Addressing any issues discovered during the pressure test before the system is put into service is crucial to prevent operational problems and potential safety hazards.
By following these installation guidelines, industrial and mechanical systems can benefit from the reliable performance and durability of rubber joints. Properly installed rubber joints contribute to the overall efficiency, safety, and integrity of the systems they are incorporated into, ultimately reducing maintenance costs and preventing unexpected downtime. Adhering to best practices for rubber joint installation is essential for ensuring the long-term functionality and operational reliability of industrial equipment and pipelines.
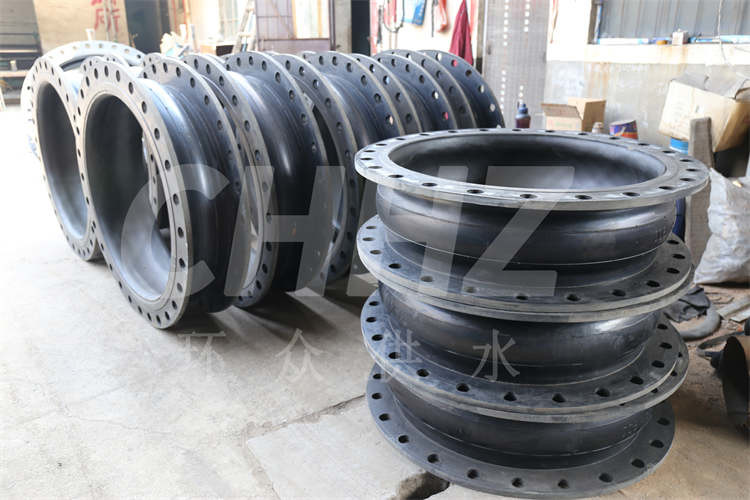