How duckbill check valve work
Check valves, also known as non-return or one-way valves, are designed to allow fluid to flow one way in a pipeline. They’re constructed of a clapper which hangs from a hinge, the clapper shaft or pin, which is mounted to the underside of the bonnet, inside the valve body. The basic design of a check valve inhibits backflow in a line.
Because of their simple design, check valves generally operate without automation or human interaction and instead rely on the flow velocity of the fluid to open and close. This means they generally do not have a method of outside operation, like a handle or lever. The minimum upstream pressure required to operate the valve is called the “cracking pressure”. Check valves are generally designed specifically with this number in mind and, depending on the size and style of check valve, this number is 1 psi to 5 psi.
The degree of opening on a check valve is determined by the flow rate. The higher the flow rate, the more open the valve will be until it reaches its maximum, full open position. On many check valves, the full open position is approximately 85 degrees.
There are a variety of types of check valves, including:
- Swing check or tilting disc check valves – Consist of a clapper with a disc that is convex on the upstream inlet side and flat on the downstream outlet side. For API 600 valves, this disc swings on a hinge or trunnion that is mounted to the bottom of the valve bonnet. For API 6D valves, the typical construction is a cast pocket in the valve body with a drop in shaft/pin and bushing arrangement that the clapper will turn on. This traditional type of construction requires some sort of restraint to keep the clapper in the pocket. Newer designs include shaft/pin bosses that are drilled through with the shaft/pin inserted into the bosses to keep the clapper in place. Generally, large check valves are swing check valves.
- Ball check valves – Consist of a spherical ball clapper which is sometimes spring-loaded to provide sealing at pressures below the cracking pressure. Because of the spherical design, these valves can easily wear from prolonged use and require frequent maintenance; therefore, they should be installed in places that are easy for repair teams to access.
- Diaphragm check valves – Consist of a rubber diaphragm clapper that flexes open when the pressure on the upstream side is greater than the pressure on the downstream side, and closes when this pressure is equalized or lowered below a set pressure differential.
- Stop-check valves – Usually constructed similar to a swing check valve, stop-check valves have an additional external control mechanism (e.g., an actuator, lever/handwheel, etc.) that allows the valve to be deliberately closed regardless of flow pressure.
- Duckbill valve – This type of check valve allows flow to proceed through a soft tube that feeds into the downstream side of the valve, wherein backpressure collapses the tube and cuts off the flow.
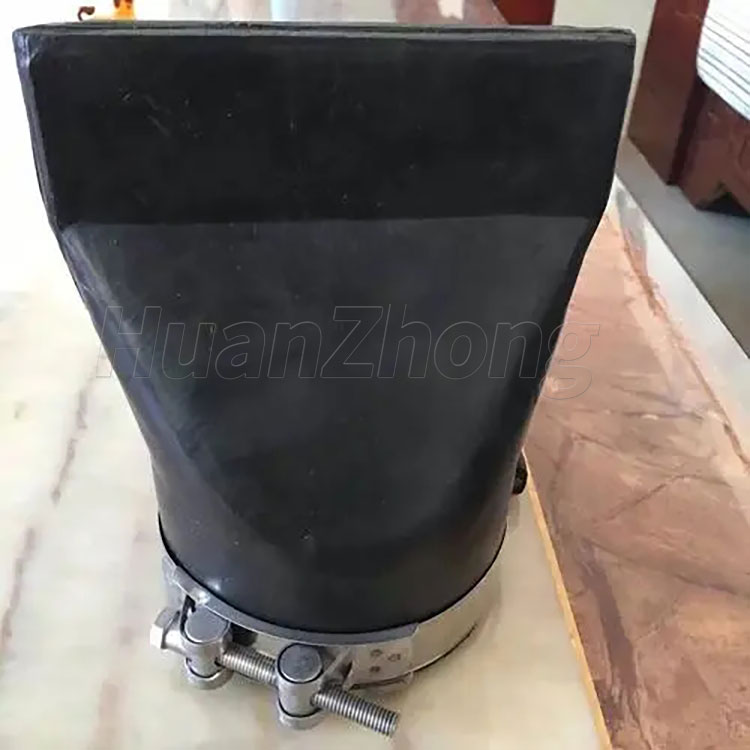