Rubber Flexible Joint Mold Casting Process
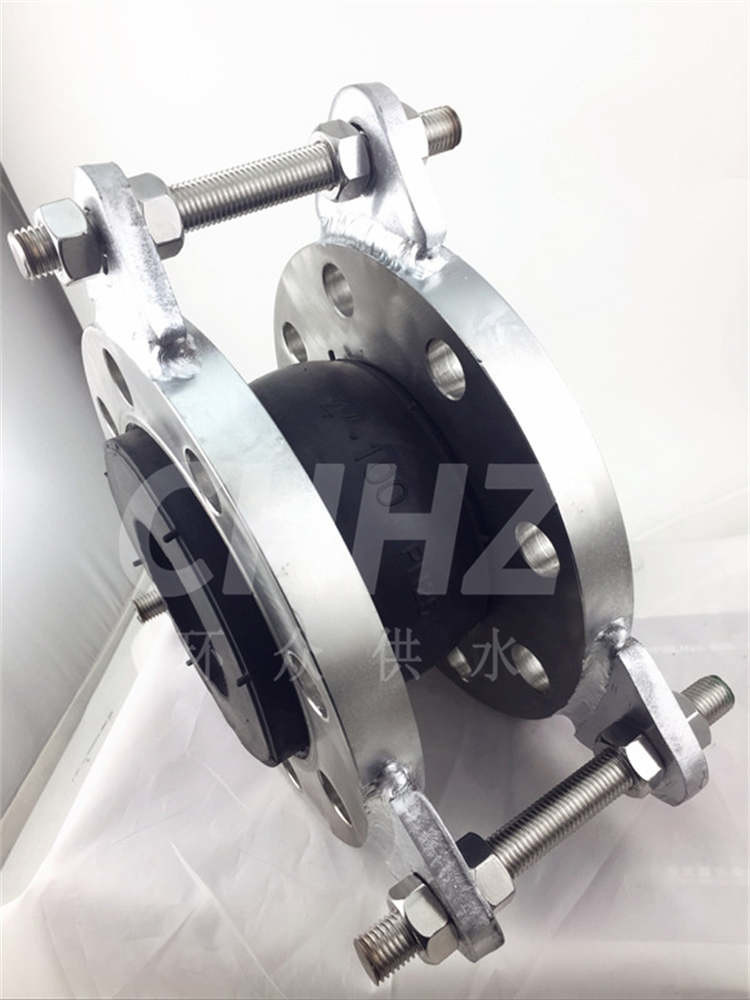
Introduction: The rubber flexible joint mold casting process plays a critical role in the production of rubber flexible joints used in piping systems for various industrial applications. This article aims to delve into the manufacturing process, emphasizing the importance of precision, quality materials, and expert craftsmanship in creating durable and reliable rubber flexible joints.
Material Selection: The first step in the mold casting process involves the careful selection of high-quality elastomeric compounds suitable for manufacturing rubber flexible joints. These compounds must exhibit resilience, flexibility, and resistance to environmental factors and chemical corrosion, ensuring the integrity and longevity of the final product. Additionally, reinforcing materials such as fabric or steel may be incorporated to enhance the joint's strength and durability.
Mold Design and Preparation: The mold design for rubber flexible joints is crucial to ensuring the accurate and consistent replication of the desired joint specifications. Precise measurements and intricate detailing are incorporated into the mold design to accommodate the specific dimensions and features of the joint. Once the design is finalized, the mold is meticulously prepared, considering factors such as mold release agents, venting, and gating systems to facilitate the casting process and ensure the quality of the final product.
Casting Process: The casting process begins with the precise mixing of the selected elastomeric compounds and any reinforcing materials, ensuring a homogenous and uniform blend. The prepared mold is then filled with the compound, and a combination of heat and pressure may be applied to facilitate curing and achieve the desired physical properties. The precise control of temperature, pressure, and curing time is critical in obtaining a rubber flexible joint that meets performance standards and quality requirements.
Post-Casting Finishing and Inspection: Following the curing process, the newly cast rubber flexible joint undergoes finishing procedures to remove any imperfections, excess material, or molding artifacts. This includes trimming, buffing, and surface treatment to achieve the desired aesthetic and functional characteristics. Subsequently, the joints undergo thorough inspection to verify dimensional accuracy, material integrity, and compliance with quality standards.
Quality Assurance and Testing: Quality assurance measures play a crucial role in ensuring that every rubber flexible joint meets stringent performance and safety standards. Samples from each production batch may undergo rigorous testing, including pressure and stress tests, to confirm the joint's ability to withstand the demands of its intended application. This process serves as a vital checkpoint to identify any deviations and uphold the reliability and durability of the finished product.
Conclusion: The mold casting process for rubber flexible joints exemplifies the meticulous craftsmanship and attention to detail required in manufacturing components for industrial piping systems. The utilization of high-quality materials, precision mold design, controlled casting techniques, and thorough quality assurance measures collectively contribute to the production of durable, resilient, and reliable rubber flexible joints essential for diverse industrial applications.
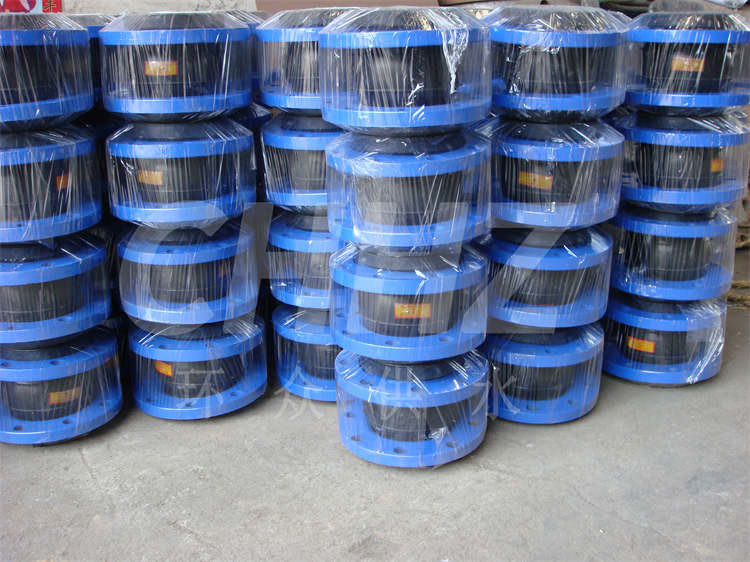