How to Connect Injection Molded Rubber Hoses
Introduction: Connecting injection molded rubber hoses is a critical aspect of various industrial applications. This article aims to provide a comprehensive guide on the methods and techniques used to effectively connect injection molded rubber hoses, emphasizing the importance of precision, material compatibility, and reliable sealing mechanisms to ensure optimal performance and safety.
Selection of Connection Method: When connecting injection molded rubber hoses, it is essential to choose an appropriate connection method based on the specific requirements of the application. Common connection methods include threaded fittings, flanged connections, quick couplings, and barbed fittings. The selection is based on factors such as pressure rating, accessibility, ease of installation, and environmental conditions in which the hoses will operate.
Preparation of Injection Molded Rubber Hoses: Before connecting injection molded rubber hoses, it is crucial to prepare the hose ends for the connection process. This involves inspecting the hose ends for any irregularities, ensuring that they are clean and free from debris, and verifying that the dimensions and material properties are suitable for the intended connection method. Additionally, applying lubricants compatible with the rubber material can facilitate easier and secure fitting.
Threaded Fittings: For hoses connected using threaded fittings, the hose ends need to be carefully threaded into the corresponding female fittings. It is important to apply the appropriate sealant or thread compound to ensure a reliable seal and prevent leakage. Adequate torque should be applied to achieve proper engagement without damaging the hose or the fitting.
Flanged Connections: When utilizing flanged connections, the hose ends are matched with the flanges of the corresponding equipment or piping. This process requires precise alignment to ensure a proper seal, and the use of gaskets or sealing rings is common to prevent fluid leakage. Bolting the flanges securely, evenly, and in a specified sequence is essential to maintain the integrity of the connection.
Quick Couplings: Connecting injection molded rubber hoses using quick couplings involves aligning the hose ends with the coupling's receptacle and applying force to engage the locking mechanism. Quick couplings are designed for rapid installation and disconnection, providing convenience and versatility in applications requiring frequent hose changes or maintenance.
Barbed Fittings: Barbed fittings are commonly used for flexible hoses, wherein the hose ends are stretched and forced over barbed spigots, creating a secure and sealed connection. Proper selection of the barb size and material compatibility is crucial to ensure tight gripping and prevent disconnection under pressure.
Verification and Testing: Following the connection of injection molded rubber hoses, it is imperative to verify the integrity of the connections. This may involve pressure testing, visual inspection, and leak detection to ensure that the connections are secure and capable of withstanding the operational conditions.
Conclusion: Effectively connecting injection molded rubber hoses requires careful consideration of the connection method, meticulous hose preparation, and adherence to quality assurance practices. By employing precise techniques and compatible materials, manufacturers and operators can achieve reliable and leakage-free hose connections crucial for the safe and efficient operation of industrial systems.
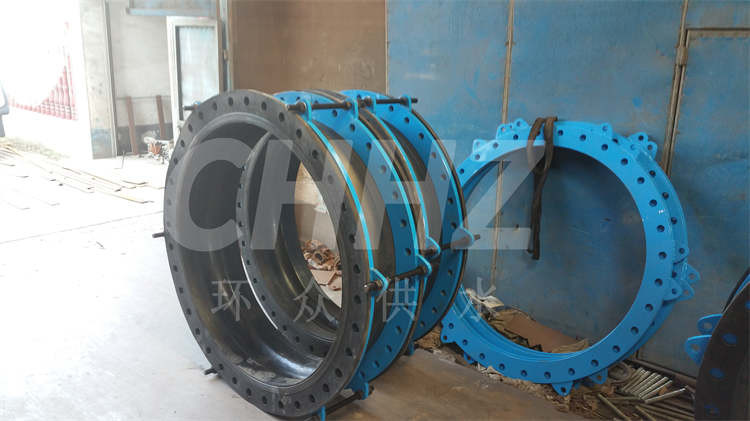