Manufacturing Rubber Joints: Ensuring Quality and Reliability
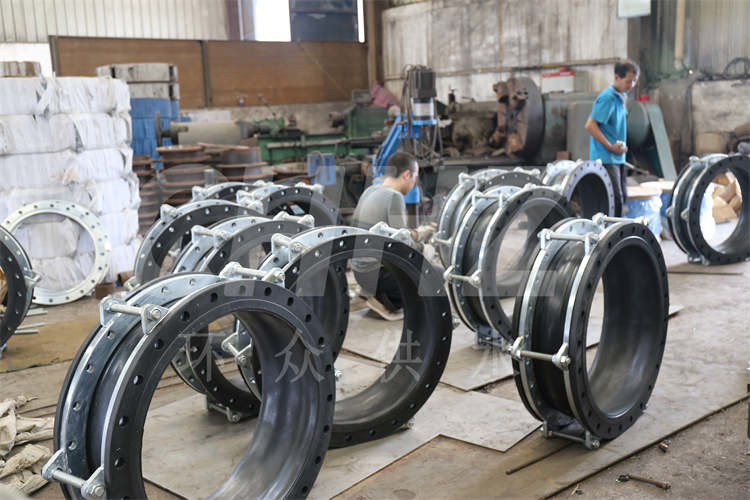
The production of rubber joints involves a meticulous process that aims to create durable and versatile components for a wide range of industrial applications. This article delves into the key aspects of manufacturing rubber joints, highlighting the importance of precision, material selection, and quality control in ensuring the functionality and reliability of these essential components.
Material Selection: The manufacturing process commences with the careful selection of rubber compounds that exhibit the necessary properties for the intended application. Factors such as elasticity, resilience, chemical resistance, and thermal stability are meticulously evaluated to ensure that the chosen rubber material aligns with the performance requirements of the joint.
Precision Molding and Vulcanization: Once the rubber material is chosen, precision molding techniques are employed to form the joints with exacting specifications. The use of molds ensures consistent dimensions and shapes, essential for achieving compatibility and seamless integration with the connected components. Following molding, vulcanization – a process of heat and pressure treatment – is applied to enhance the strength, durability, and resilience of the rubber joints.
Reinforcement and Flexibility: In certain applications, rubber joints may require internal reinforcing elements, such as fabric or metal inserts, to augment their structural integrity and resistance to internal pressure. This reinforcement allows the joints to withstand varying degrees of movement, pressure, and environmental stresses while maintaining their flexibility and damping characteristics.
Compatibility and Sealing: Rubber joints are often designed to facilitate the connection and sealing of different components, such as piping systems or mechanical assemblies. Accordingly, precise engineering and manufacturing processes are employed to ensure that the joints adhere to dimensional standards and provide reliable sealing, effectively preventing leaks and maintaining system integrity.
Quality Assurance and Testing: Stringent quality control measures are fundamental throughout the manufacturing process. Comprehensive testing procedures, including dimensional checks, material property assessments, and performance evaluations, are conducted to verify the consistency and compliance of rubber joints with specified standards and customer requirements.
Customization and Application-Specific Solutions: Manufacturers often offer customization options to tailor rubber joints to the specific needs of diverse industries and applications. This flexibility enables the production of bespoke solutions that meet unique operational demands, whether in plumbing systems, automotive engineering, industrial machinery, or infrastructure projects.
Environmental and Safety Considerations: The manufacturing of rubber joints prioritizes environmental responsibility by incorporating sustainable practices and adhering to regulatory guidelines. Furthermore, the components are engineered to deliver safe and reliable performance, particularly in critical applications where safety and operational integrity are paramount.
In summary, the manufacturing process for rubber joints encompasses meticulous material selection, precision molding, reinforcement, sealing, rigorous quality control, customization, and a commitment to environmental and safety standards. By adhering to these principles, manufacturers can consistently produce rubber joints that meet the diverse needs of industries, ensuring reliable performance, durability, and operational safety across a spectrum of applications.
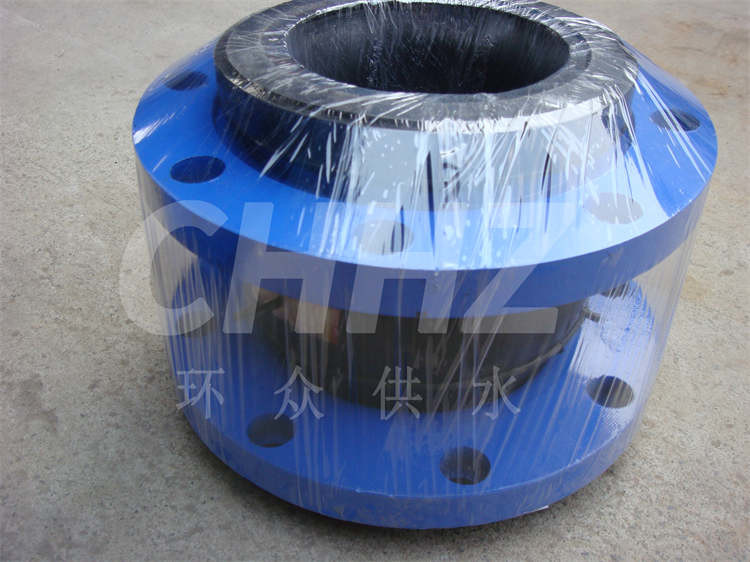