Rubber Expansion Joints: Understanding their Application in Engineering
Rubber expansion joints are pivotal components in engineering projects, serving to accommodate movement, absorb vibrations, and maintain the integrity of piping systems and structures. This article aims to elucidate the significance and application of rubber expansion joints in engineering projects while highlighting their diverse functions and benefits.
Movement Absorption: In engineering applications, the dynamic nature of piping systems and structures necessitates the incorporation of flexible elements capable of accommodating movement due to thermal expansion, vibrations, or seismic activities. Rubber expansion joints provide the necessary flexibility to absorb these movements, mitigating stress on connected components and sustaining system longevity.
Vibration Dampening: Industrial processes and machinery often generate significant vibrations that can propagate through interconnected piping systems. Rubber expansion joints effectively dampen these vibrations, preventing their transmission to other components and minimizing the risk of structural fatigue and equipment damage.
Stress Relief in Piping Systems: The installation of rubber expansion joints within piping networks alleviates the stress induced by thermal expansion and contraction, thereby averting potential damage to pipes, supports, and connected equipment. By distributing movement-induced forces, rubber expansion joints contribute to the longevity and operational reliability of the overall system.
Versatile Application Range: Rubber expansion joints find extensive use in various engineering domains, including HVAC systems, power generation facilities, chemical processing plants, water treatment facilities, and industrial infrastructure. Their adaptability to diverse environments and operating conditions underscores their relevance across a spectrum of engineering projects.
Sealing and Leak Prevention: In addition to their flexibility and vibration-dampening capabilities, rubber expansion joints serve as critical sealing elements within piping systems. Their design and construction facilitate effective sealing, reducing the likelihood of leaks and ensuring operational integrity in fluid-handling applications.
Customization and Material Selection: Engineering projects often necessitate the customization of rubber expansion joints to suit specific dimensional and performance requirements. Manufacturers offer a range of materials, such as EPDM, neoprene, and natural rubber, allowing for tailored solutions that address environmental conditions, temperature extremes, and chemical exposure.
Maintenance and Service Life: Incorporating high-quality rubber expansion joints in engineering designs contributes to reducing maintenance requirements and extending the service life of piping systems and structures. Properly selected and installed expansion joints minimize the need for costly repairs and downtime, optimizing the overall efficiency of engineered systems.
In conclusion, the deployment of rubber expansion joints is an integral aspect of engineering projects, contributing to the durability, reliability, and safety of industrial systems and structures. By understanding the unique functions and benefits of rubber expansion joints, engineers and project stakeholders can make informed decisions regarding their inclusion in designs, ensuring the seamless operation and longevity of critical engineering applications.
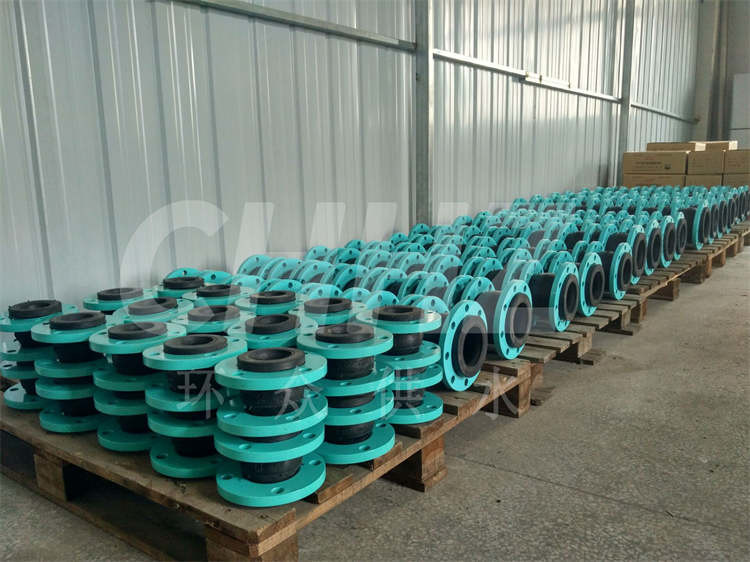