Design of vulcanized rubber joint mold
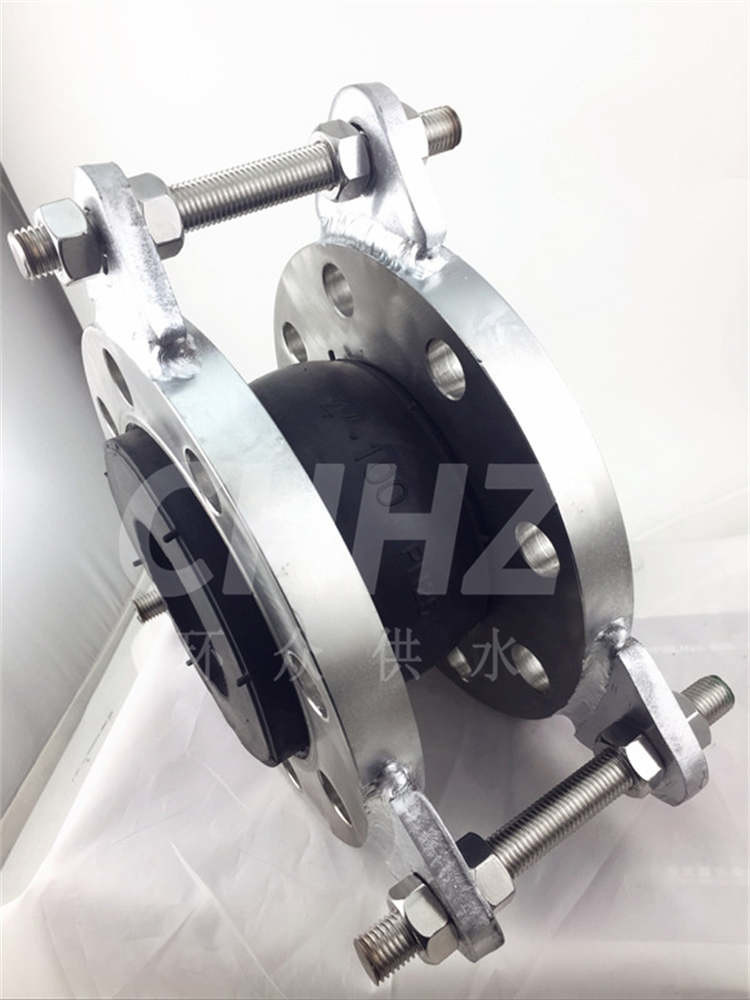
Introduction:The design of molds for vulcanized rubber joints is critical to ensuring the production of high-quality rubber joints that meet industry standards. This article will discuss the key considerations and best practices in designing molds for vulcanized rubber joints.
Material Selection:The selection of materials for the mold is crucial. The mold should be made of durable, heat-resistant materials, such as high-grade steel or aluminum, to withstand the high temperatures and pressures involved in the vulcanization process. Additionally, the mold material should have good thermal conductivity to ensure uniform heat distribution and promote the curing of the rubber.
Design Considerations:
Several design considerations must be taken into account during the mold design process:
Mold cavity and core design: The mold cavity should be designed to accurately replicate the dimensions and features of the desired rubber joint. The core should allow for the proper flow of rubber material to achieve uniform filling and prevent air entrapment.
Venting: Proper venting within the mold is essential to allow the escape of air and gases during the vulcanization process, preventing defects such as air pockets or blowholes in the rubber joint.
Draft angles and parting lines: Incorporating appropriate draft angles and designing well-defined parting lines ensures easy demolding of the cured rubber joint, reducing the likelihood of damage.
Cooling channels: Integrating cooling channels into the mold design facilitates efficient heat dissipation and helps maintain consistent temperatures during the vulcanization process, contributing to the quality of the rubber joint.
Surface Finish and Texture:The surface finish and texture of the mold are essential to achieving the desired surface characteristics of the rubber joint. A polished finish with the appropriate texturing promotes the release of the cured rubber joint from the mold while imparting the desired surface appearance and texture.
Mold Maintenance and Durability:Regular maintenance and cleaning of the mold are critical to prolong its lifespan and ensure consistent production of high-quality rubber joints. The mold should be designed for ease of maintenance, with features such as removable inserts and accessibility to cleaning and inspection.
Conclusion:The design of molds for vulcanized rubber joints requires careful consideration of material selection, mold geometry, surface finish, and maintenance requirements. By adhering to best practices in mold design and construction, manufacturers can produce high-quality rubber joints that meet industry standards and customer expectations.
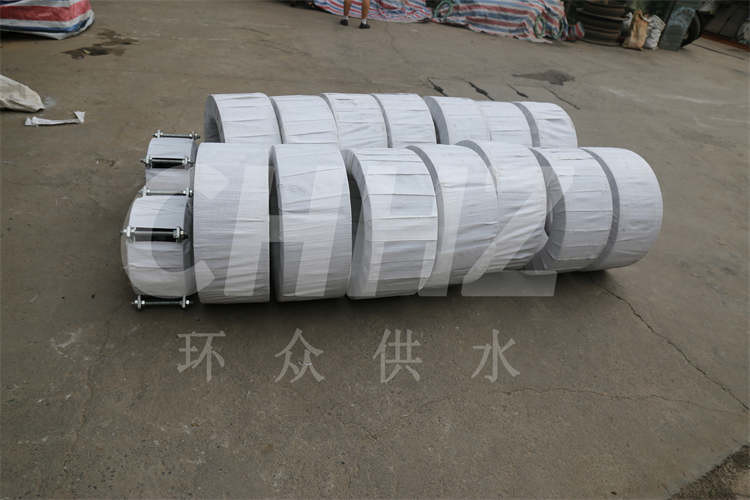