High-pressure rubber cable joint production
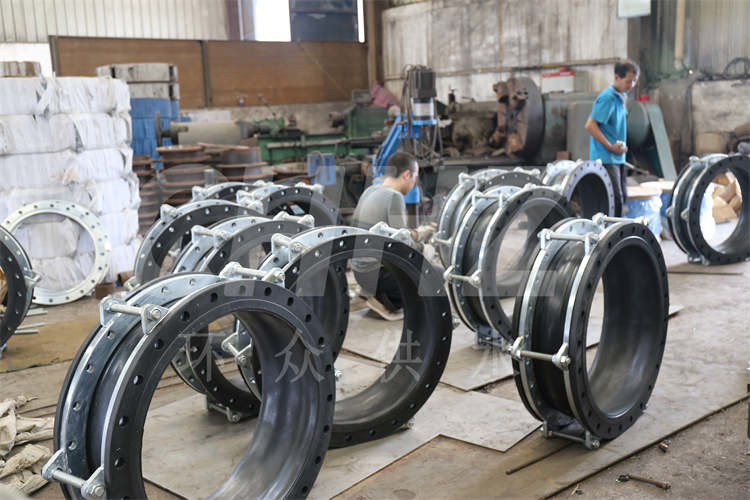
Introduction:High-pressure rubber cable joints are essential components in various electrical systems and industrial applications. This article will discuss the key steps and considerations in the production of high-pressure rubber cable joints to ensure safety, reliability, and performance.
Material Selection:Selecting the appropriate materials is crucial for the production of high-pressure rubber cable joints. The rubber used must possess excellent insulating properties, temperature resistance, and mechanical strength to withstand high pressures and provide reliable electrical insulation. Additionally, the conductor material must be chosen for its conductivity, strength, and resistance to corrosion.
Preparation of Components:The production process begins with the preparation of components. This includes cutting and stripping the rubber insulation, preparing the conductor ends, and ensuring the cleanliness of all components to promote proper bonding and electrical conduction.
Molding Process:The molding process involves carefully positioning the prepared conductors and rubber insulation within the mold to achieve the desired joint configuration. The mold must be designed to provide uniform pressure distribution, prevent air entrapment, and facilitate the proper flow and curing of the rubber material.
Vulcanization:Once the assembly is in the mold, the vulcanization process takes place. This involves subjecting the joint to elevated temperatures and pressures, allowing the rubber material to cure and bond firmly to the conductors. Proper time, temperature, and pressure control are critical to ensure the formation of a durable and reliable joint.
Testing and Quality Control:After vulcanization, the joint undergoes rigorous testing to verify its electrical insulation, mechanical strength, and resistance to pressure. This includes high-voltage testing, tensile testing, and inspection for any defects or irregularities. Quality control measures are essential to identify and rectify any issues, ensuring the joint meets safety and performance standards.
Sealing and Insulation:To further enhance the joint's reliability, sealing compounds and insulating materials are applied to protect the joint from moisture, contaminants, and mechanical stress. Proper sealing and insulation help to maintain the joint's integrity and electrical performance over its operational lifespan.
Conclusion:The production of high-pressure rubber cable joints requires meticulous attention to material selection, preparation, molding, vulcanization, testing, and quality control. By adhering to stringent production standards and quality assurance procedures, manufacturers can produce high-quality cable joints that meet the demanding requirements of electrical systems and industrial applications.
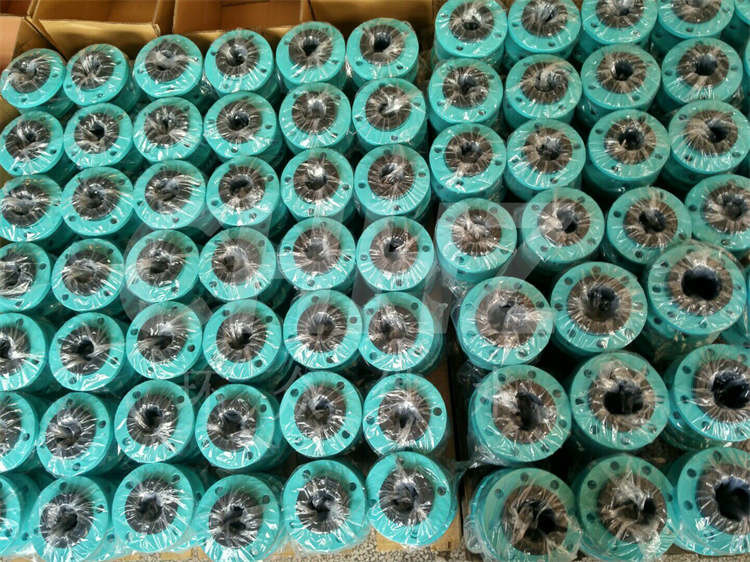