Rubber Flexible Joints in Cosmetics Manufacturing
Rubber flexible joints play a crucial role in the cosmetics manufacturing industry, ensuring smooth operations in the production and packaging of various beauty and personal care products. These specialized connectors are designed to accommodate the unique demands of cosmetics manufacturing processes, providing versatility, durability, and reliability. In this article, we will delve into the significance of rubber flexible joints in cosmetics manufacturing, their functionality, and the considerations for their optimal usage.
Importance of Rubber Flexible Joints: In cosmetics manufacturing, where precision, hygiene, and efficiency are paramount, rubber flexible joints are indispensable for maintaining seamless operations. These joints are utilized in a wide range of equipment, such as mixers, filling machines, and packaging lines, where they facilitate the transfer of fluids, gases, and semi-solid materials. By accommodating the movement, vibration, and thermal expansion associated with these processes, rubber flexible joints help to protect equipment, reduce stress on pipelines, and prevent leaks, ultimately contributing to the overall safety and integrity of the cosmetics production environment.
Functionality and Design: Rubber flexible joints are engineered to withstand the rigorous conditions found in cosmetics manufacturing facilities. They are designed to provide flexibility, allowing for movement and misalignment, while effectively dampening vibrations and noise. These joints are also resilient to various chemicals and temperatures, ensuring compatibility with the diverse range of substances used in cosmetics formulations. Additionally, their ability to absorb shocks and reduce the transmission of mechanical stress helps to prolong the lifespan of equipment and minimize the risk of damage or malfunction.
Considerations for Optimal Usage: Selecting the appropriate rubber flexible joints for cosmetics manufacturing applications requires careful consideration of several factors. Compatibility with the types of fluids and chemicals used in the production process is crucial to ensure the longevity and integrity of the joints. Additionally, ensuring that the joints are constructed from materials compliant with industry regulations and standards, such as FDA requirements for food-grade materials, is essential to maintain product safety and quality. Furthermore, regular inspection and maintenance of rubber flexible joints are essential to identify signs of wear, deterioration, or potential failure, thereby preventing operational disruptions and maintaining a safe and efficient manufacturing environment.
Maintenance and Replacement: Monitoring the condition of rubber flexible joints and implementing a proactive maintenance schedule is imperative for cosmetics manufacturers. Routine inspections should be conducted to check for signs of wear, corrosion, and degradation of the joints' material properties. Any detected issues should be promptly addressed, and worn-out joints should be replaced to prevent potential leaks, contamination, or production downtime. By adhering to a proactive maintenance approach, manufacturers can ensure the continued reliability and performance of rubber flexible joints in cosmetics manufacturing.
In conclusion, rubber flexible joints are integral components in cosmetics manufacturing, providing essential flexibility and protection in various processes and equipment. Through their ability to accommodate movement, vibration, and thermal fluctuations, while withstanding the demands of chemicals and temperature variations, these joints contribute to the efficiency, safety, and reliability of cosmetics production operations. By recognizing their importance and implementing prudent maintenance practices, cosmetics manufacturers can ensure the continued smooth functioning of their production processes, thereby upholding the standards of quality and safety in the beauty and personal care products they deliver to consumers.
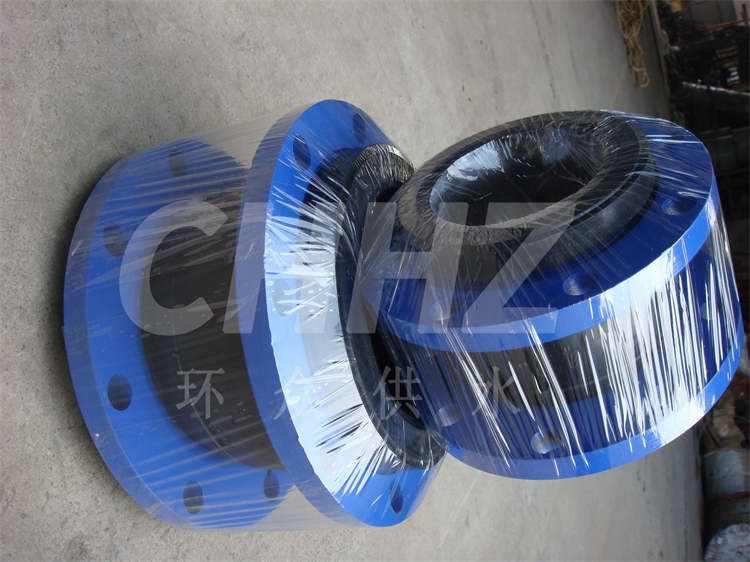