Rubber Gasket Molds in Flexible Connectors: Ensuring Versatile and Reliable Solutions
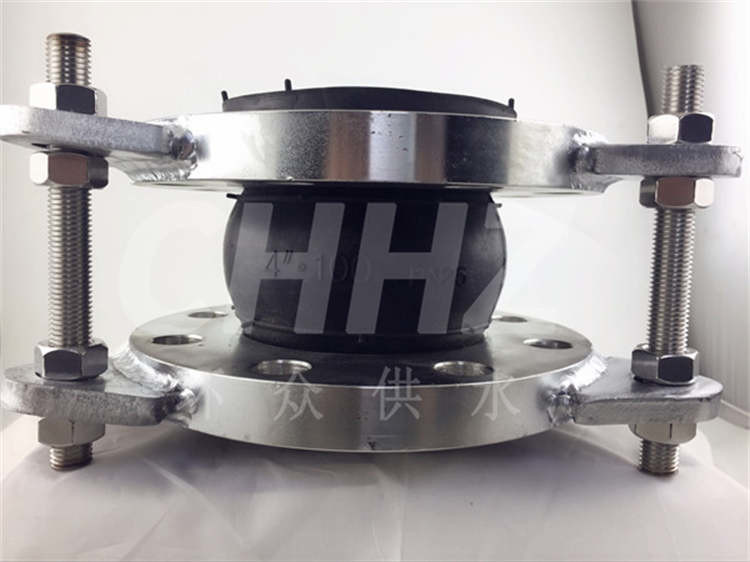
Rubber gasket molds play a pivotal role in the manufacturing of flexible connectors, providing essential components that enable the efficient and reliable operation of various systems across industries. These molds are instrumental in creating high-quality rubber gaskets that serve as sealing and cushioning elements in flexible connectors, ensuring their adaptability to diverse applications and environments. In this article, we will explore the significance of rubber gasket molds in the production of flexible connectors, their manufacturing process, and the critical aspects of their functionality and application.
Significance of Rubber Gasket Molds: Rubber gasket molds are integral to the production of flexible connectors, which are widely used in fluid and gas handling systems, machinery, and automotive applications. These molds enable the fabrication of custom-designed gaskets with precise specifications, ensuring optimal sealing and resilience in connectors subjected to varying pressures, temperatures, and environmental conditions. The versatility and reliability of rubber gasket molds contribute to the seamless performance of flexible connectors in critical functions, such as preventing leaks, dampening vibrations, and accommodating movement and misalignment.
Manufacturing Process: The manufacturing process of rubber gasket molds involves precision engineering and material selection to meet the specific requirements of flexible connectors. Initially, a mold design is created based on the dimensions and specifications of the intended gasket, considering factors such as size, shape, and material composition. The mold is then used to shape and form the rubber gasket, utilizing compression or injection molding techniques to achieve the desired characteristics, including flexibility, elasticity, and resistance to chemical and environmental factors. Quality control measures are implemented throughout the process to ensure consistency and uniformity in the production of gaskets that meet stringent performance standards.
Functionality and Application: Rubber gasket molds result in the creation of gaskets that play critical roles in flexible connectors across a wide spectrum of industries. These gaskets serve as seals to prevent fluid or gas leakage in pipelines, couplings, and valves, contributing to the integrity and safety of fluid-carrying systems. Furthermore, they act as cushioning elements in mechanical assemblies, absorbing shocks and vibrations to protect equipment and enhance operational stability. The adaptability of rubber gasket molds allows for the production of gaskets tailored to specific applications, including high-temperature environments, corrosive chemicals, and dynamic operational conditions, ensuring reliable performance across diverse industries.
Material Considerations: The selection of materials for rubber gasket molds is based on the application requirements and performance criteria of the flexible connectors they serve. Factors such as the chemical compatibility of the rubber material with the conveyed fluids, temperature resistance, and mechanical properties are carefully considered to ensure the suitability and longevity of the gaskets. Additionally, compliance with industry standards and regulations, such as ASTM specifications and FDA guidelines for food-grade materials, is essential in meeting quality and safety requirements in various sectors.
In conclusion, rubber gasket molds are essential components in the manufacture of flexible connectors, providing the vital sealing and cushioning elements that enable versatile and reliable solutions in diverse industrial applications. Through precision molding techniques and material selection, these molds facilitate the production of high-quality gaskets that meet the exacting demands of fluid handling systems, machinery, and automotive technologies. Their role in ensuring effective sealing, vibration isolation, and adaptability to challenging operating conditions underscores the significance of rubber gasket molds as foundational components in the creation of resilient and reliable flexible connectors.
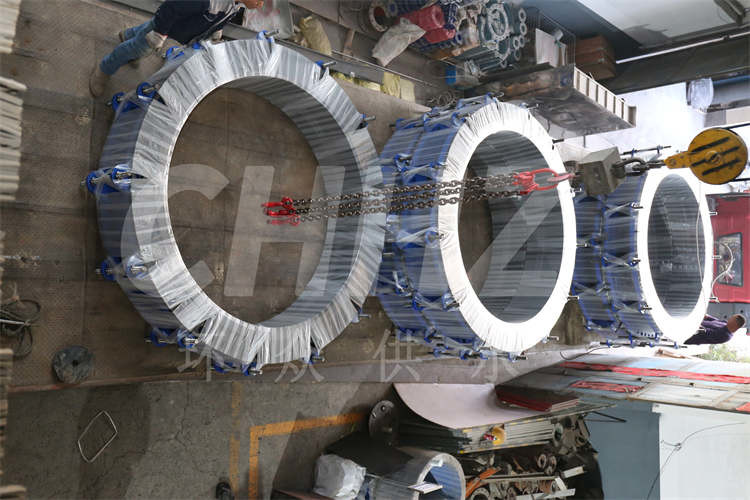