Engineering Insights on Common Rubber Hose Connections
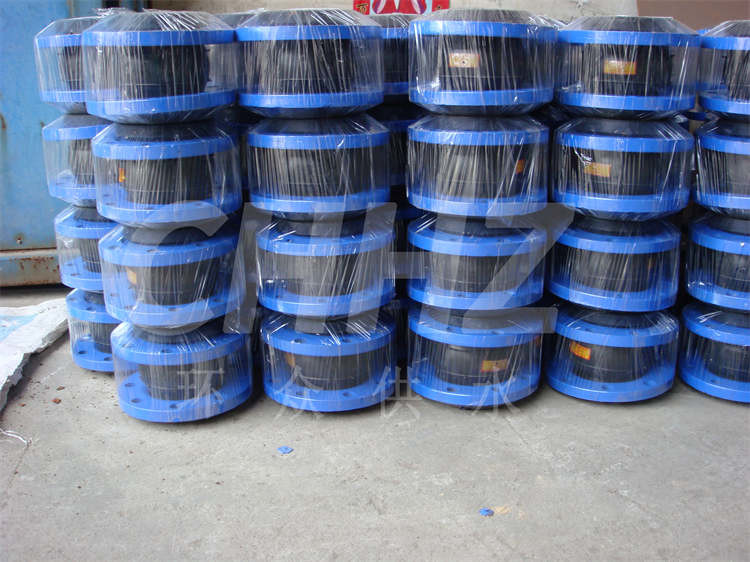
Rubber hose connections are a ubiquitous component in various engineering applications, providing crucial flexibility and durability in fluid transfer systems. This article delves into the technical aspects and practical considerations surrounding the application, design, and maintenance of common rubber hose connections.
Diverse Applications Rubber hose connections are widely employed across different engineering disciplines, from automotive and machinery manufacturing to industrial and hydraulic systems. Their flexibility, resistance to abrasion, and ability to accommodate vibration and movement make them suitable for applications requiring dynamic fluid transfer, such as hydraulic systems, pneumatic systems, and cooling circuits.
Design and Material Considerations The success of rubber hose connections hinges on appropriate design and material selection. Engineers must assess factors such as operating pressure, temperature range, fluid compatibility, and environmental conditions to select the most suitable rubber hose for a given application. Furthermore, the reinforcement of rubber hoses with textiles, wire braids, or other materials plays a pivotal role in determining their strength and performance under operating conditions.
Installation Best Practices Proper installation is paramount for the reliability and performance of rubber hose connections. Care must be taken to ensure correct hose routing, minimizing kinks, twists, and bends that could impair fluid flow or compromise hose integrity. Correct fitting of end connections and secure clamping are also critical to prevent leakages and maintain the structural integrity of the hose assembly.
Maintenance and Inspection Protocols Establishing a routine maintenance schedule and inspection protocols is essential to monitor the condition of rubber hose connections. Periodic visual checks for signs of wear, rubbing, or degradation, as well as assessments of fitting tightness and secure attachment, are crucial for identifying potential issues and preventing unexpected system failures.
Performance and Failure Analysis When evaluating the performance and failure modes of rubber hose connections, engineers should consider factors such as pressure spikes, excessive bending or twisting, and exposure to harsh operating environments. Analyzing the root causes of failures can inform design improvements and selection of more robust hose materials or reinforcement techniques to enhance longevity and reliability.
Compliance with Standards and Regulations Compliance with industry standards and regulatory requirements is integral to the design, production, and application of rubber hose connections. Adhering to standards such as SAE J517 for hydraulic hoses or ASTM D380 for rubber hose testing ensures that the hose assemblies meet performance and safety benchmarks, providing confidence in their reliability and durability.
In conclusion, the proper selection, installation, maintenance, and evaluation of rubber hose connections are essential aspects of engineering design and operation. With a comprehensive understanding of material properties, application requirements, and best practices in installation and maintenance, engineers can ensure the robustness and effectiveness of rubber hose connections across diverse engineering applications.
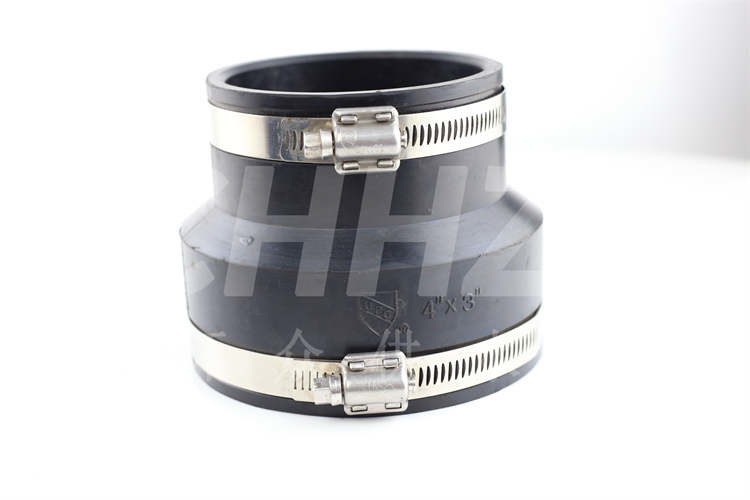