Advancements in Rubber Hose Engineering Technology
Rubber hose engineering technology has witnessed significant advancements, revolutionizing the performance, durability, and versatility of rubber hose connections across various industrial applications. This article outlines the key developments in rubber hose engineering technology, highlighting improvements in design, materials, and manufacturing processes that have contributed to enhanced functionality and reliability.
Advanced Material Science The development of high-performance synthetic rubber compounds has been a pivotal breakthrough in rubber hose engineering. Advanced elastomers with superior resistance to abrasion, chemicals, heat, and environmental elements have extended the operational lifespan of rubber hoses, enabling their deployment in demanding applications such as oil and gas extraction, mining, and heavy machinery.
Reinforcement Technologies Innovations in reinforcement technologies, including the integration of high-tensile steel wire braids, textile yarns, and synthetic fibers, have bolstered the strength and resistance of rubber hose assemblies to withstand high pressure, pulsation, and flexing. These advancements have expanded the operational range of rubber hoses, making them indispensable in critical hydraulic systems, pneumatic circuits, and fluid transport applications.
Fluid Dynamics and Flow Optimization Engineering advancements have focused on optimizing the internal design of rubber hoses to minimize fluid friction, pressure drops, and turbulence. This has led to the development of smoother bore surfaces, improved geometries, and enhanced construction techniques, resulting in increased flow efficiency and reduced energy consumption in hydraulic and pneumatic systems utilizing rubber hose connections.
Industry-specific Customizations The evolution of rubber hose engineering has facilitated the customization of hose assemblies to meet the unique requirements of specific industries. Tailored solutions for applications such as automotive fuel delivery, chemical processing, food and beverage transfer, and pharmaceutical production have emerged, offering specialized materials and designs to ensure compliance with industry standards and regulations.
Smart Manufacturing and Testing Advancements in manufacturing technologies, including automated extrusion, vulcanization, and assembly processes, have enhanced the consistency and quality of rubber hose production. Additionally, sophisticated testing methods such as impulse testing, burst testing, and environmental exposure assessments have become integral in validating the performance, durability, and safety of rubber hose assemblies prior to deployment in real-world applications.
Innovations in End Connections and Accessories The integration of quick-connect fittings, swivel joints, protective sleeves, and IoT-enabled monitoring devices has expanded the functionality and adaptability of rubber hose connections. These innovations improve ease of installation, facilitate maintenance, and enable real-time performance monitoring, contributing to operational efficiency and predictive maintenance strategies.
In summary, the continuous evolution of rubber hose engineering technology has propelled the versatility, resilience, and performance of rubber hose connections across diverse industrial domains. With ongoing research and development initiatives, the future holds promise for further innovations, driving the advancement of rubber hose technology to meet the evolving needs of modern engineering applications.
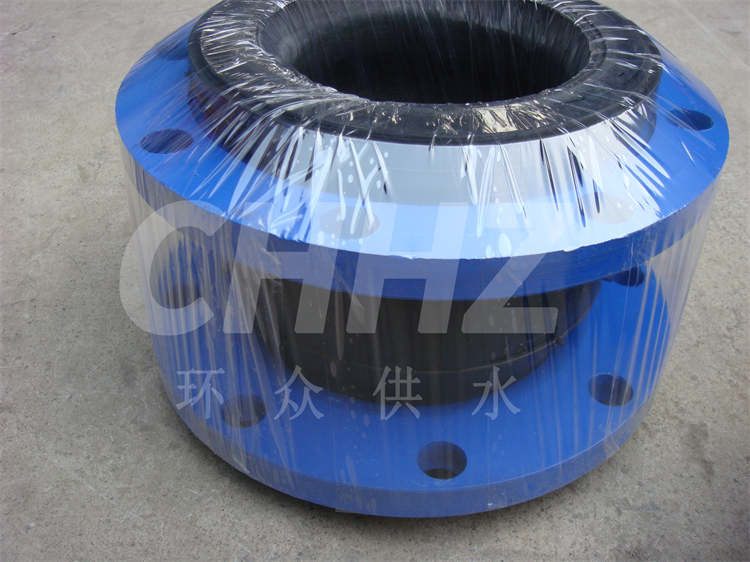