Rubber joints
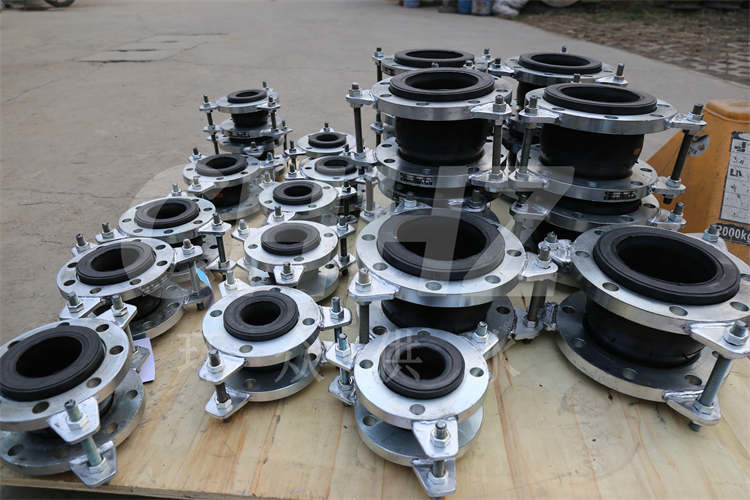
Rubber joints, also known as rubber expansion joints, are essential components in valve assembly systems. These fittings serve a vital purpose in providing flexibility, vibration isolation, and compensation for misalignment in piping systems, including those associated with valves. The effective integration of rubber joints with valve components is crucial for ensuring the reliable and efficient operation of industrial systems. Customizing rubber joints for valve assemblies involves several key considerations to address specific operational requirements.
Material Selection: Selecting the appropriate rubber material for the joint is essential to ensure compatibility with the media, pressures, and temperatures encountered in valve applications. Common rubber materials used for joints include EPDM, NBR, neoprene, and natural rubber. The material selection process takes into account factors such as chemical resistance, temperature range, and mechanical properties to optimize performance.
Connector Design: The design of rubber joints for valve applications entails the consideration of connector type and configuration. This includes determining the dimensions, shape, and attachment method of the rubber joint to ensure seamless integration with the valve components. Flexible connectors such as flanged, threaded, or grooved ends are tailored to meet specific valve requirements, allowing for easy installation and reliable operation.
Operating Conditions: Customization of rubber joints for valve assemblies involves a comprehensive analysis of the operating conditions to determine the appropriate design parameters. This includes addressing factors such as pressure rating, temperature range, flow velocity, and external forces to ensure that the rubber joints are engineered to withstand the anticipated conditions and provide optimal performance and longevity.
Quality Assurance: Custom rubber joints for valve applications undergo rigorous quality control measures to ensure compliance with industry standards and specifications. This includes testing for pressure resistance, chemical compatibility, and dimensional accuracy to validate the reliability and safety of the joints within valve systems. Quality assurance processes contribute to the overall integrity and performance of the rubber joints in demanding operational environments.
Installation and Maintenance: Customized rubber joints are designed to facilitate easy installation and maintenance within valve assemblies. Considerations for alignment, accessibility, and serviceability are incorporated into the joint design to streamline the integration process and minimize downtime during maintenance activities. Clear installation guidelines and support materials are provided to ensure the proper implementation of rubber joints in valve systems.
In conclusion, the customization of rubber joints for valve assemblies is a critical aspect of optimizing the performance and reliability of industrial systems. By addressing material selection, connector design, operating conditions, quality assurance, and installation/maintenance considerations, custom rubber joints are tailored to meet the specific requirements of valve applications, contributing to the overall efficiency and durability of industrial valve systems.
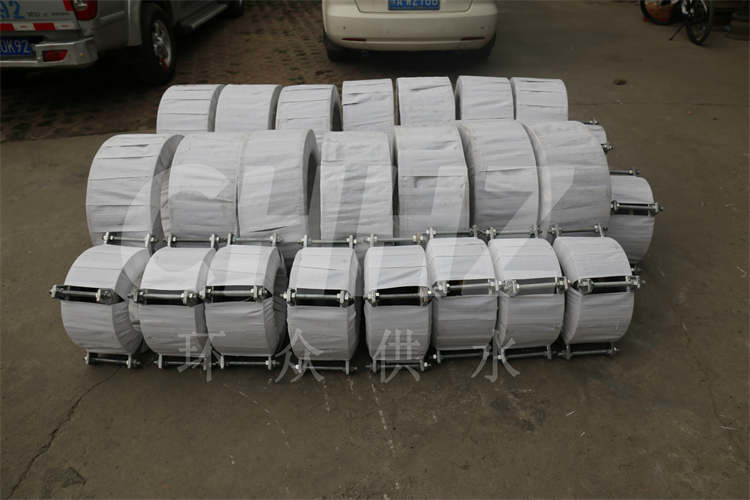