The connection between rubber joints and valves
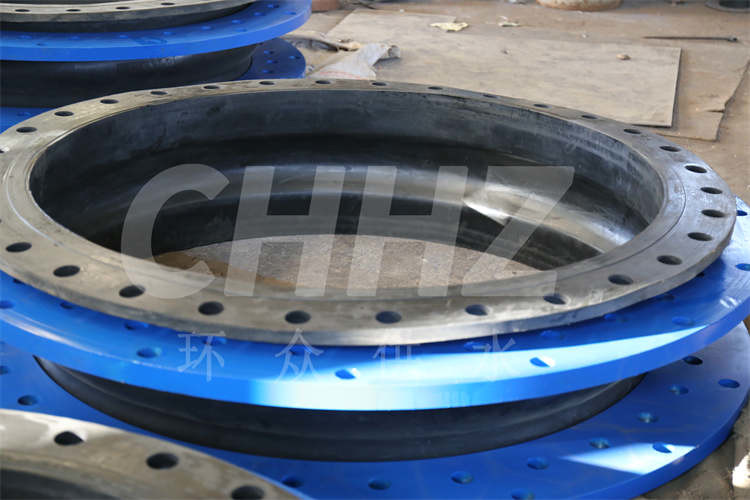
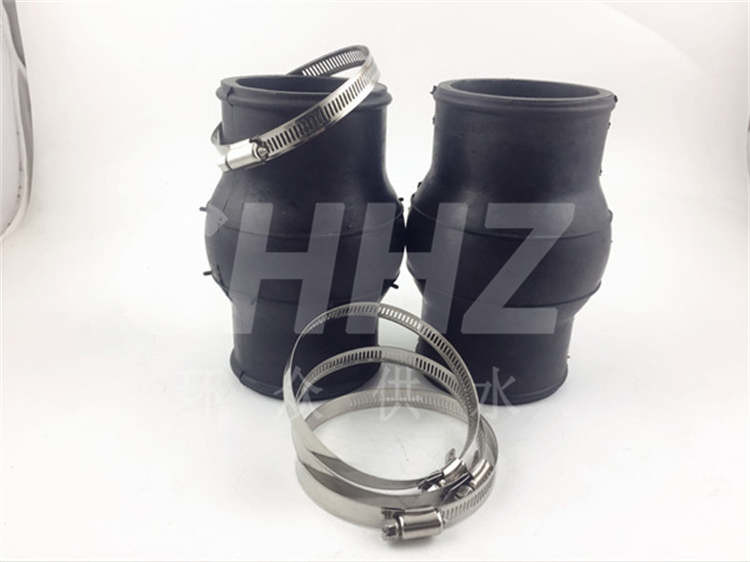
The connection between rubber joints and valves is crucial for ensuring the efficient and reliable operation of piping systems. A proper connection method not only facilitates the transfer of fluids but also minimizes stress on the components, reduces vibration, and prevents leakage. Here, we will discuss some common techniques for effectively connecting rubber joints to valves in industrial applications.
Flanged Connection: Flanged connections represent one of the most prevalent methods for joining rubber joints to valves. This approach involves the attachment of a flanged rubber joint to a flanged valve using bolts and nuts, creating a secure and sealed interface between the two components. By aligning the bolt holes and applying gaskets, the connection achieves proper alignment and provides a tight seal, thereby preventing fluid leakage and ensuring system integrity. Flanged connections offer versatility and ease of installation, making them suitable for a wide range of piping systems.
Threaded Connection: In applications where space constraints or specific design considerations come into play, threaded connections may be employed to connect rubber joints to valves. This method involves screwing the threaded end of a rubber joint directly onto the threaded outlet or inlet of a valve, creating a robust and compact connection. Threaded connections offer simplicity and convenience, particularly in smaller pipe diameters, and are well-suited for applications where frequent disassembly and reassembly are required.
Welded Connection: For applications demanding a permanent and integral connection, welding the rubber joint to the valve provides a reliable and durable solution. This method entails the fusion of the rubber joint flange to the valve flange, or the direct welding of the rubber joint body to the valve body, ensuring a strong and leak-proof bond. Welded connections offer superior resistance to vibration, thermal expansion, and mechanical loads, making them suitable for high-pressure and high-temperature applications.
Victaulic or Grooved Connection: In scenarios that demand flexibility and ease of installation, Victaulic or grooved connections present an alternative method for connecting rubber joints to valves. This approach involves the use of grooved mechanical couplings that clamp onto the ends of the rubber joint and the valve, providing a secure and flexible joint. Victaulic connections accommodate movement and misalignment, making them ideal for applications subject to vibration, thermal expansion, or seismic activity.
Compression-Type Couplings: Another method for connecting rubber joints to valves involves the use of compression-type couplings, which utilize a compressive force to secure the connection. This technique is particularly suited for non-standard pipe sizes or irregular configurations, as it provides adaptability and ease of installation without the need for specialized tools or extensive preparation.
In conclusion, the connection between rubber joints and valves encompasses various techniques, including flanged, threaded, welded, Victaulic/grooved, and compression-type couplings. Each method offers distinct advantages in terms of installation ease, sealing reliability, flexibility, or permanence, catering to the diverse requirements of industrial piping systems. By selecting the appropriate connection method based on system parameters, operators can ensure the seamless integration of rubber joints with valves, promoting the efficient and trouble-free operation of the overall piping network.
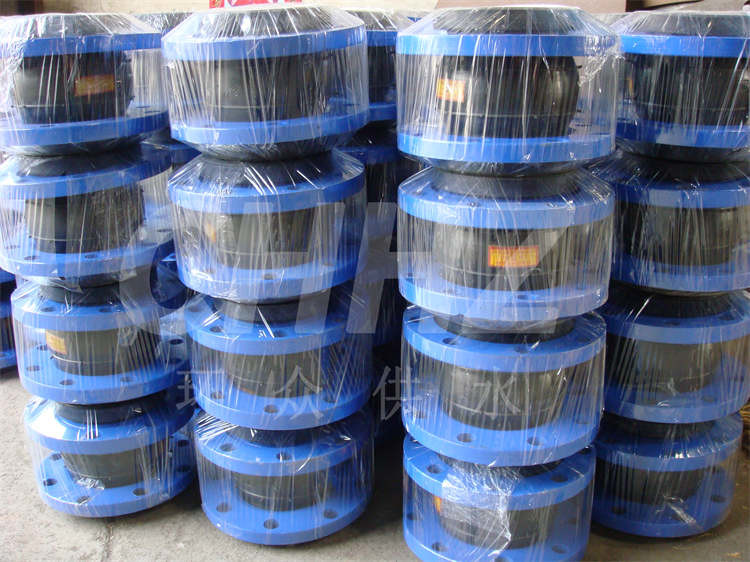