Processing of Flexible Rubber Joints
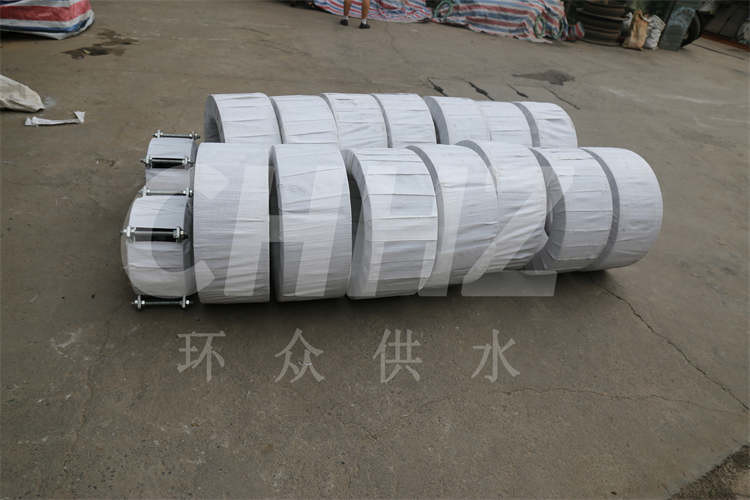
Flexible rubber joints, also known as expansion joints, play a crucial role in many piping systems, providing flexibility and vibration isolation. Understanding the processing methods for flexible rubber joints is essential for ensuring their quality and performance. In this article, we will explore the manufacturing processes involved in producing flexible rubber joints.
Material Selection: The manufacturing process of flexible rubber joints begins with the careful selection of suitable elastomeric materials. Natural rubber, synthetic rubber compounds, and various polymers are commonly used due to their resilience, flexibility, and resistance to chemical and environmental factors. The material selection is based on the specific requirements of the application, including temperature range, pressure, and compatibility with the fluid being conveyed.
Molding and Vulcanization: The production of rubber joints involves the use of precision molds that shape the raw rubber material into the desired form. Compression or injection molding techniques are employed to create the intricate shapes and structures of the joints. Following molding, the rubber components undergo vulcanization, a process that imparts strength, resilience, and resistance to the material through the application of heat and pressure.
Fabric Reinforcement: In many cases, flexible rubber joints are reinforced with fabric layers to enhance their mechanical strength and resistance to pressure. High-strength fibers such as polyester or aramid are embedded within the rubber during the molding process to provide structural support and prevent ballooning or deformation under operating conditions.
Flange and End Fitting Attachment: To facilitate the connection of flexible rubber joints to piping systems, flanges or end fittings are integrated into the manufacturing process. Flanges are molded directly onto the joint ends, providing the means for secure bolting to the adjoining pipes or equipment. End fittings are also attached to the joints to accommodate threaded or grooved connections, offering versatility in installation methods.
Quality Control and Testing: Throughout the manufacturing process, stringent quality control measures are implemented to ensure the dimensional accuracy, material consistency, and structural integrity of the rubber joints. Additionally, comprehensive testing procedures, including pressure testing, leakage testing, and mechanical performance testing, are conducted to verify the reliability and performance of the finished products.
Surface Treatment and Coating: In some applications, flexible rubber joints undergo surface treatment and coating processes to enhance their chemical resistance, weatherability, and abrasion resistance. Protective coatings or linings may be applied to the interior surfaces of the joints to mitigate the effects of corrosive fluids or abrasive particles.
In conclusion, the manufacturing processes of flexible rubber joints encompass material selection, molding, reinforcement, end fitting attachment, quality control, testing, and surface treatment. By adhering to rigorous production standards and employing advanced techniques, manufacturers can ensure the production of high-quality rubber joints that meet the diverse requirements of modern industrial and commercial piping systems.
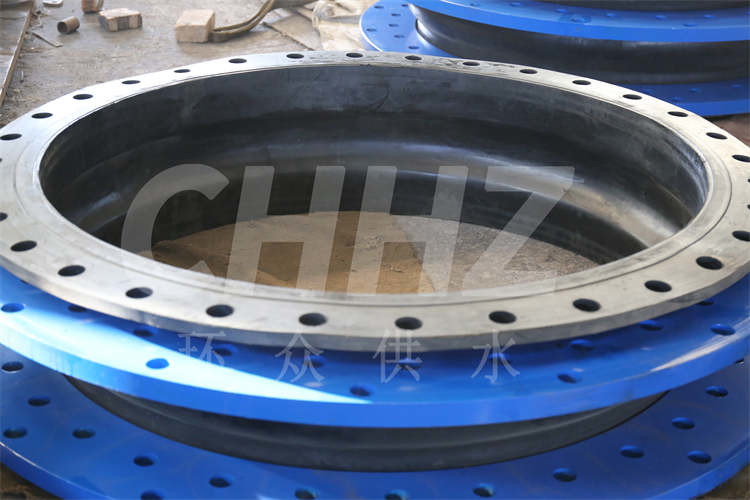